WHMIS and Chemical Management
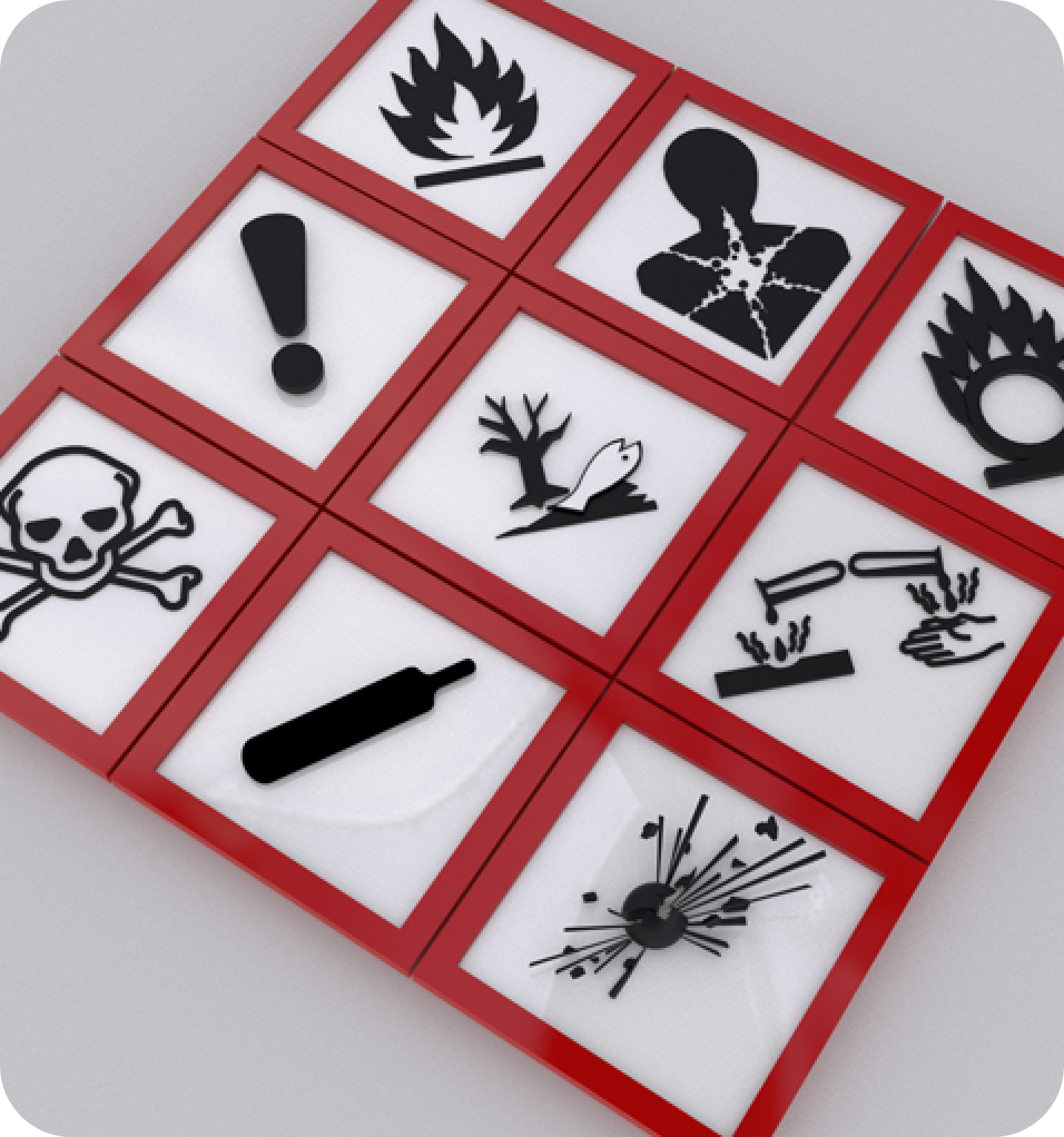
Highlighted words reveal definitions when selected.
Every workplace has hazardous products - ranging from cleaning products to full chemical production. Taking steps to manage chemicals present at the workplace will reduce health and safety risks, lower environmental impact, and reduce operation costs. If chemicals are not used, stored and handled properly, they can cause injury, illness, disease, fire, explosions, property damage, or harm to the environment. For example, chemical exposure occurs when we breathe them in, absorb them through the skin, or when they are unintentionally swallowed.
The workplace hazardous materials information system (WHMIS) is a standardized system which includes rules for hazard classification, labelling, safety data sheets (SDSs), and worker education and training. It provides workers with important health and safety information about hazardous products in the workplace.
Employer Responsibilities
Employers must:
- Conduct a risk assessment and develop written rescue and evacuation procedures where employees use, store, or handle hazardous products at a work site and there is a potential need to evacuate or rescue workers. [OHS Regs., s. 38]
- Establish and maintain a chemical control program that is appropriate for the risks to worker health and safety. [OHS Regs., s. 12(1)(h)] [OHS Regs., s. 42(2)]
- Eliminate hazardous products in the workplace, or substitute with a less hazardous product, if possible. Where elimination or substitution is not possible, use engineering and administrative controls to make sure that hazardous products are used, stored and handled safely. Consult the SDS or consumer product safety information for advice on suitable controls. [OHS Regs., s. 42(3), (4) and (5)]
- Make sure hazardous products are used, stored, and handled only when all safety and legislative requirements are satisfied. For hazardous products, WHMIS requirements include labels, identifiers, SDS, and worker education and training. Where WHMIS requirements are not met, an employer is only permitted to store a hazardous product at the workplace while they are actively looking for the required information. [WHMIS Regs., s. 4]
- Develop policies and procedures to protect a worker from exposure to a reproductive toxin (when pregnant or trying to conceive) or a sensitizer, if applicable. Actions must include informing workers of the hazard, identifying ways to reduce or eliminate exposure, and may include protective reassignment. [OHS Regs., s. 42(10) and (12)]
- Clean up spills involving solvents, oils, greases, paints and other flammable products with an approved non-combustible absorbent product. Store used absorbents in a covered metal container outside of work areas, until it can be disposed of. [OHS Regs., s. 42(13) and (14)]
Supplier Labels
Employers must:
- Make sure every hazardous product received at the workplace has a WHMIS label affixed, printed, or attached to it. Where a supplier label is missing, use a workplace label. [WHMIS Regs., s. 7(1)] [WHMIS Regs., s. 7(7)]
- Affix, print, or attach a label (similar to a supplier label) to an unpackaged hazardous product or hazardous product that is transported as a bulk shipment. [WHMIS Regs., s. 7(8)]
- Not remove, deface, modify, or alter a supplier label unless it is a small container (three millilitres or less) and the label interferes with normal use. [WHMIS Regs., s. 7(2) and (6)]
- Update labels or information on the container when significant new data becomes available. [WHMIS Regs., s. 7(4)]
- Replace labels when they cannot be read (illegible) or have been removed [WHMIS Regs., s. 7(5)].
Workplace Labels
Employers must:
- Use a workplace label for a hazardous product produced at the workplace, unless the product is about to be labelled for sale. [WHMIS Regs s. 8(1) and (3)]
- Update workplace labels when new significant data becomes available. [WHMIS Regs., s. 8 (2)]
- Make sure a workplace label is used when a hazardous product is decanted or transferred to another container unless the container: [WHMIS Regs., s. 9(1)]
- Will be used exclusively by and be kept under the control of the worker who filled the container;
- Is used only during the same shift in which it was filled;
- The content is identified; and
- The entire amount of the product stored in the container is needed for immediate use. [WHMIS Regs., s. 9(2)]
Laboratory Labels
Employers must:
- Make sure a hazardous product that meets the definition of a laboratory sample under the regulations has a supplier label that contains: [WHMIS Regs., s. 12(1)]
- The chemical name (or generic chemical name) of ingredients that are regulated by WHMIS;
- The statement “Hazardous Laboratory Sample”; and
- An emergency telephone number that will allow a person to get information required to be disclosed on an SDS, 24 hours a day, 7 days a week.
- Use a workplace label to identify a hazardous product a container other than the original container received from the supplier, or is produced in the workplace or a laboratory unless: [WHMIS Regs., s. 12(2)]
- It is laboratory sample;
- Intended solely for use, analysis, testing, research, development, or evaluation in a laboratory;
- It is not removed from the laboratory;
- It is clearly identifiable to workers at the workplace; and
- Workers are educated and trained about the safe use, storage, handling, and disposal of the hazardous product; and the mode of identification used.
- Make sure worker education and training allows the worker to easily identify and locate: [WHMIS Regs., s. 12(3)]
- The information required on the SDS;
- A label or document that includes the information required on a hazardous product a container other than the original container, or is produced in the workplace or a laboratory; and
- Other information necessary to ensure the safe use, storage, handling, and disposal of the laboratory sample.
- Make sure that a copy of a supplier or employer SDS is available to workers. [WHMIS Regs., s. 13(7) and (8)]
Safety Data Sheets
Employers must:
- Make sure every hazardous product received at the workplace has a SDS that complies with the Canadian WHMIS regulatory requirements. [WHMIS Regs., s. 13(1)]
- Where possible, obtain an updated SDS when the revision date on the SDS is three or more years old. [WHMIS Regs., s. 13(2)] An updated SDS is not required if the new SDS does not apply to the original product, or if there is written confirmation from the supplier that the SDS has not changed. [WHMIS Regs., s. 13(3)]
- Add any significant new data to the existing SDS, if an updated SDS is not available. [WHMIS Regs., s. 13(4)]
- Make sure that all hazardous products produced at the workplace have a SDS, and that the SDS is updated as soon as practical and not later than 90 days after new significant data becomes available. [WHMIS Regs., s. 14]
- Make SDSs readily available to workers who may be exposed to a hazardous product, and to the OHS Committee or Worker Health and Safety Representative. [WHMIS Regs., s. 15(a) and (b)]
- Consult with the OHS Committee or Worker Health and Safety Representative on how to best make the SDSs readily available [WHMIS Regs., s. 15(c)]
- Employers may provide workers with an SDS that is in a different format from the supplier SDS, as long as the required information is disclosed, the new format is approved by the OHS Committee or Worker Health and Safety Representative, and the new format SDS indicates that the supplier SDS is available at the workplace. [WHMIS Regs., s. 13(5)]
- Notify workers who may be exposed to a hazardous product and the OHS Committee or Worker Health and Safety Representative when significant new data becomes available. [WHMIS Regs., s. 16]
- Where a hazardous product is made at a workplace, disclose necessary information to an OHS Officer, worker, OHS Committee or Worker Health and Safety Representative relating to the sources of the toxicological data used to create the employer’s SDS. [WHMIS Regs., s. 25]
These Regulations also provide a mechanism for maintaining confidential business information by registering a hazardous product with Health Canada under the Hazardous Materials Information Review Act. However, even with approval by this Act, confidential business information must be provided to a healthcare professional treating a person in an emergency. The health professional must keep this information confidential at the employer’s request. [WHMIS Regs., s. 23] [WHMIS Regs., s. 17...22] [WHMIS Regs., s. 24]
Chemical storage
Employers must:
- Make sure that the amount of a hazardous product in a work area does not exceed the amount reasonably needed for work in progress, normally in one shift. [OHS Regs., s. 57(1)]
- Store hazardous products in a way that will not allow them to mix with incompatible products if a container was to leak, break or otherwise become damaged. [OHS Regs., s. 58]
- Store bulk quantities of a hazardous product in a designated area that is separate from the work area. The designated storage area must be: [OHS Regs., s. 57(2)] [OHS Regs., s. 59(2)]
- Designed and built to safely contain the product stored inside;
- Clearly labelled using signs, placards, or a similar method;
- Designed and maintained to allow the safe movement of workers, equipment and materials;
- Adequately ventilated and lit; and
- In a location not normally occupied by workers. The location must not include a lunchroom, eating area, change room, clothing storage locker, or in the passenger compartment of a vehicle.
- When dispensing or transferring flammable liquids inside a flammable storage room, the room must: [OHS Regs., s. 60]
- Ventilated at a rate of at least 18 cubic metres per hour, for each square metre of floor area, but not less than 250 cubic metres per hour;
- Provide a markup air duct, passing through a fire separation, shall be equipped with an approved fire damper;
- Provided with exhaust that vents directly outdoors; and
- Equipped with self-closing doors.
Routine and emergency wash facilities
Employers must:
- Assess the need for emergency washing facilities based on a risk assessment of the workplace. This risk assessment must consider the SDS, consumer safety information, or other information. [OHS Regs., s. 63(d)]
- Provide emergency washing facilities that meet ANSI requirements, such as emergency water baths, showers, jump tanks, eyewash stations, or another effective means of treatment, in a work area where a worker may come into contact with a hazardous product. [OHS Regs., s. 42(11)] [OHS Regs., s. 63(a)]
- Only use potable (drinking quality) water in a plumbed emergency eyewash station or shower. [OHS Regs., s. 63(b)]
- Only use potable water or isotonic saline solution in a non-plumbed emergency eyewash station or shower. [OHS Regs., s. 63(b)]
- Make sure access to an emergency eyewash or shower facility is not blocked by material or equipment. [OHS Regs., s. 63(c)]
- Make sure that flushing fluid is tempered to ensure that a person can safely, comfortably and effectively flush the affected area for as long as needed.
- Provide and maintain a suitable facility for changing clothes and showering where there is a high risk of a worker being contaminated by a hazardous product, and allow time during normal working hours for use of this facility without loss of pay. [OHS Regs., s. 62(2)] [OHS Regs., s. 64(2)(b)]
- Provide suitable protective clothing and head coverings, and make sure they are handled and cleaned in a way that prevents exposure. [OHS Regs., s. 64(2)(a)(c)]
Worker exposure
Employers must:
- Keep the amount of an airborne hazard as low as reasonably practical, and monitor the quality of the air where a hazardous product could make the air dangerous to the health and safety of workers. [OHS Regs., s. 42(1)] [OHS Regs., s. 42(7)(a)]
- Make sure, exposure to a hazardous product is kept a low as is reasonably practical, and where a threshold limit value (TLV) has been set by the ACGIH, exposure must not exceed the TLV. These TLVs include: [OHS Regs., s. 42(7)(c)(d)(e)]
- Time weighted average (TWA);
- Short-term exposure limit (STEL) and three times the TWA for more than 30 minutes in total during the work period; and
- Ceiling limit (C) and five times the TWA.
- Make sure that a TLV is adjusted for unusual work shifts (e.g. shift that are not 8 hours a day in a 24 hour period), if applicable. [OHS Regs., s. 42(8)]
Health surveillance
Employers must:
- Assess the need and extent of health surveillance for workers. [OHS Regs., s. 43(1)]
- Based on the result of the assessment, establish and maintain a health surveillance program to monitor the health of workers exposed to a hazardous product. [OHS Regs., s. 43 (2), and (3)]
- Make sure that an occupational health surveillance program is communicated to workers. [OHS Regs., s. 43(4)]
- When a worker is participating in health surveillance, make sure that medical exams are scheduled during normal work hours and that workers do not lose pay. [OHS Regs., s. 43(5) and (6)]
- Provide, without loss of pay, temporary alternative work, where a physician has advised OHS Division that a hazardous product negatively impacted the health of a worker and they require temporary removal or accommodation. [OHS Regs., s. 43(7)]
- Keep records related to the health surveillance program and make these records available to workers who request them. [OHS Regs., s. 43(8)]
Worker education and training
Employers must:
- Keep workers informed of the nature and degree of harm expected from using, storing, or handling a hazardous product, including information received from the supplier (or the employer, if the product is produced on-site) and any other information know to the employer. [WHMIS Regs., s. 5] [OHS Regs., s. 42(7)(b)]
- Make sure workers are educated about the purpose and relevance of information contained in supplier labels, workplace labels, and SDSs. [WHMIS Regs., s. 6(1)(a) and (b)]
- Make sure that workers are trained on how to use, store, handle and dispose of a hazardous product safely, including when the product is contained in piping, vessels, tanks, conveyors, or another similar means. [WHMIS Regs., s. 6(1)(c) and (d)]
- When a hazardous product is contained in piping, vessels, tanks, conveyors or another similar means, make sure worker training includes the meaning of colour coding, labels, placards, or other methods of identification. [WHMIS Regs., s. 10]
- Make sure that workers are trained in how to respond in an emergency and the unintended release of emissions into the air. [WHMIS Regs., s. 6(1)(e) and (f)]
- Make sure worker education and training is specific to the workplace and its hazards prevention and control program. It must also be developed in consultation with the OHS Committee, Worker Health and Safety Representative, or Designate. [WHMIS Regs., s. 6(2)]
- Make sure that workers are able to apply the information learned to work safely with the hazardous product and respond to an emergency, including a worker exposure or spill. Evaluation methods could include using written tests, practical demonstration, or another suitable method. [WHMIS Regs., s. 6(3)]
- Review education and training programs at least annually or more often if there has been a change in the work or new hazard information is available. This review must be done in consultation with the OHS Committee or the Worker Health and Safety Representative or Designate. [WHMIS Regs., s. 6(4)]
Substance specific legislation
Employer must also follow specific regulations related to:
- Silica [OHS Regs., s. 46] [OHS Regs., s. 47]
- Asbestos [OHS Regs., s. 48] and Asbestos Abatement Regulation
- Lead [OHS Regs., s. 49]
- Painting, coating and working with plastics and resins [OHS Regs., s. 69]
- Abrasive blasting [OHS Regs., s. 118...126]
- Hazardous materials during demolition and salvage[OHS Regs., s. 398]
- Excavation, underground work and rock crushing [OHS Regs., s. 413]
- Fire protection [OHS Regs., s. 443] [OHS Regs., s. 444]
- Combustible substances [OHS Regs., s. 446]
- Welding, cutting and burning [OHS Regs., s. 449...457]
- Confined space entry [OHS Regs., s. 511...516]
Worker Responsibilities
Workers must:
- Take reasonable care to protect his or her health and safety and that of workers and persons at or near the workplace. [OHS Act, s. 6)]
- Properly wear or use personal protective equipment (PPE), safeguards and safety and devices provided for their protection in accordance with the manufacturer’s instructions and training provided by the employer. [OHS Act, s. 7(a)(a.1)] and [OHS Regs., s. 17]
- Participate in training and hazard assessments, if provided.
- Not use equipment or perform work tasks where the required training has not yet taken place.
- Immediately report concerns and hazards to the supervisor or employer. [OHS Regs., s. 17(3)]
Related topics
- Ventilation
- Confined space entry
- Emergency response
- Hazard recognition evaluation and control
- Personal protective equipment
Hazardous products
Means a product, material, mixture or substance classified under one or more of the hazard classes defined under the Canadian Hazardous Product Act.Label
Means a written, printed or graphic information elements relating to a hazardous substance which are designed to be affixed to, printed on or attached to the hazards our substance or the container in which it is packaged. [WHMIS Regs., s. 2(l)]Safety Data Sheet
A safety data sheet (SDS) provided by a supplier that contains information required by the Hazardous Products Act (Canada), including potential hazards of a hazardous substance, instructions on how to work safely with it, and actions to take in an emergency. A SDS should not be confused with the label; as it contains much more detailed information.Before using a hazardous product, it's essential to conduct a risk assessment by reading and fully understanding the SDS.[WHMIS Regs., s. 2(s]
Education
Means the delivery of general information to workers including information applicable to more than one workplace or job. [WHMIS Regs., s. 2(e)]Training
Refers to the delivery of workplace and job specific information to workers. [WHMIS Regs., s. 2(w)]Bulk shipment
Means a shipment of a hazardous product that is contained, without intermediate containment or intermediate packaging, in:A vessel that has a water capacity equal to or greater than 450 litres;
A freight container, a road vehicle, a railway vehicle or a portable tank;
The hold of a ship; or
A pipeline. [WHMIS Regs., s. 2(a)]
new significant data
Means new data regarding the hazard presented by a hazardous product that changes its classification in a category of a hazard class or results in its classification in another hazard class, or changes the ways to protect against the hazard presented by the hazardous product. [WHMIS Regs., s. 2(t)]Readily available
Means:Present in an appropriate place that is known to the workers;
Accessible to workers at all times; and
In the form of either a physical copy that can be handled or an electronic copy that is easily available in hard copy to workers likely to be exposed to a hazardous product. [WHMIS Regs., s. 2(q)]
OHS Officer
An occupational health and safety officer appointed under this Act and includes a medical practitioner providing services under section 20 while he or she is providing those services. [OHS Act, s. 2(i)]Threshold Limit Values (TLVs)
Threshold limit values represent conditions under which it is believed that nearly all workers may be repeatedly exposed, day after day, over a working lifetime, without adverse health effects.
ACGIH (American Conference of Governmental Industrial Hygienists)
The American Conference of Governmental Industrial Hygienists (ACGIH) is a scientific organization that develops occupational exposure limits for chemical and physical hazards. These limits can be found in their TLVs® and BEIs® book.In Newfoundland and Labrador, acceptable occupational exposure limits are established by the ACGIH.
Time weighted average (TWA)
The time weighted average concentration for a conventional 8 hour workday and a 40 hour workweek, to which it is believed that nearly all workers may be repeatedly exposed day after day, over a working lifetime, without adverse health effects.Short-term exposure limit (STEL)
A 15 minute time weighted average exposure that should not be exceeded at any time during the workday, even if the 8 hour TWA is within the TLV-TWA.
The TLV-STEL is this the concentration at which it is believed that nearly all workers can be exposed continuously for a short period of time without suffering from (1) irritation; (2)chronic or irreversible tissue damage;(3) dose-rate-dependent toxic effects; or (4) narcosis if sufficient degree to increase the likelihood of accidental injury, impaired self-rescue or materially reduced work efficacy.
Exposures up to the TLV-STEL should be less than 15 minutes, should occur no more than four times per day, and there should be at least 60 minutes between successive this range.
Ceiling limit (C)
The concentration that should not be exceeded during any part of the working exposure.OHS Division
Occupational Health and Safety Division, of Digital Government and Service NL regulates occupational health and safety in all provincial workplaces in the province of Newfoundland and Labrador. To date there are approximately 20,000 employers employing about 220,000 workers in the province.
The Division is supported by a complement of staff including OHS officers, industrial hygienists, engineers and radiation specialists to perform various multi-disciplinary activities such as:
- Investigating workplace accidents and statistics
- Conducting compliance inspections and detailed audits of workplaces
- Enforcing Occupational Health and Safety Legislation
https://www.gov.nl.ca/dgsnl/department/branches/divisions/ohs/
Supplier labels
A label provided by a supplier that contains information required by the Canadian Hazardous Products Act. [WHMIS Regs., s. 2(u)]Workplace label
A label which includes:A product identifier which is identical to that found on the safety data sheet of the corresponding hazardous product; Information for the safe handling of the hazardous product which is conveyed in a manner appropriate to the workplace; and That a safety data sheet for the hazardous product, where one has been obtained from a supplier or prepared by the employer, is available. [WHMIS Regs., s. 2(x)]
Occupational Health and Safety Committee
Where 20 or more workers are employed at a workplace, the employer shall establish an occupational health and safety committee to monitor the health, safety and welfare of the workers employed at the workplace. [OHS Act, s. 37]A committee shall consist of 2 to 12 persons. Where the employer and workers cannot agree on the size of the committee, the minister may establish its size. [OHS Act, s. 38]
At least half of the members are to be persons representing the workers who are not connected with the management. The persons representing the workers are to be elected by other workers or appointed in accordance with the constitution of the union of which the workers are members.
The employer shall appoint sufficient employer representatives to ensure that the committee may function.
The employer and worker members of a committee shall elect a co-chairperson from their respective groups.
The employer shall post the names of the committee members in a prominent place at the workplace.
A committee:
- Shall seek to identify aspects of the workplace that may be unhealthy or unsafe;
- Shall participate in a workplace inspection that an employer is required by the regulations to conduct;
- May make recommendations to principal contractors, employers, workers, self-employed persons and the Assistant Deputy Minister or an Officer for the enforcement of standards to protect the health, safety and welfare of workers at the workplace;
- Shall receive complaints from workers as to their concerns about the health and safety of the workplace and their welfare;
- Shall establish and promote health and safety educational programs for workers;
- Shall maintain records as to the receipt and disposition of complaints received from workers;
- Shall co-operate with the Assistant Deputy Minister or an Officer who is exercising his or her duties under the act; and
- Shall perform those other duties and follow those procedures that may be prescribed by the regulations. [OHS Act, s. 39]
Worker Health and Safety Representative
Where less than 20 workers are employed at a workplace, the employer shall ensure that a worker not connected with the management of the workplace is designated as the worker health and safety representative to monitor the health, safety and welfare of workers employed at the workplace.[OHS Act, s. 41]
The worker health and safety representative is to be elected by other workers at the workplace or appointed in accordance with the constitution of the labour union of which the workers are members. [OHS Act, s. 42]
The employer shall post the name of the worker health and safety representative in a prominent place at the workplace. [OHS Act, s. 43]
A worker health and safety representative has the same duties as those imposed upon a committee where that is reasonably practicable. [OHS Act, s. 44]
A worker health and safety representative shall consult with his or her employer while performing his or her duties. [OHS Act, s. 44]
Workplace Health and Safety Designate
Where less than 6 persons are engaged at a workplace and the designation of a worker health and safety representative is impracticable, the employer may designate a workplace health and safety designate to monitor the health, safety and welfare of workers employed at the workplace. [OHS Act, s. 42]The workplace health and safety designate shall be appointed by the employer. The workplace health and safety designate may be either a worker connected with the management of the workplace; or the employer, if the designation of a worker connected with the management of the workplace is not practicable. [OHS Act, s. 42]
If the assistant deputy minister or an officer is of the opinion that a workplace health and safety designate cannot adequately monitor the health, safety and welfare of workers employed at the workplace, the assistant deputy minister or officer shall order, in writing, that a worker health and safety representative be designated. [OHS Act, s. 42]
The employer shall provide and pay for training for the workplace health and safety designate. The training provided shall meet the requirements that the Workplace Health and Safety Compensation Commission may set. An employer shall compensate a worker for participating in training as if the training were regular work. [OHS Act, s. 42]
The workplace health and safety designate shall participate in the training provided. [OHS Act, s. 42]
The employer shall post the name of the worker health and safety designate in a prominent place at the workplace. [OHS Act, s. 43]
A worker health and safety designate has the same duties as those imposed upon a committee where that is reasonably practicable. [OHS Act, s. 44]
A worker health and safety designate, where the workplace health and safety designate is not the employer, shall consult with his or her employer while performing his or her duties. Where the workplace health and safety designate is the employer, he or she shall consult with the workers while performing his or her duties. [OHS Act, s. 44]
Personal protective equipment
Any equipment or device which protects a worker's body from injury, illness or death. PPE acts as a barrier to protect the worker from the hazard.PPE should only be used:
- Where other controls are not available or adequate.
- As a short-term measure before controls are implemented.
- During activities such as maintenance, clean up, and repair where other controls are not feasible or effective.
- During emergency situations.
OCCUPATIONAL HEALTH AND SAFETY ACT
R.S.N.L. 1990, c. O-3
Section 2 Definitions
2. In this Act
(a) "assistant deputy minister" means an assistant deputy minister appointed under section 9 of the Executive Council Act for the proper conduct of this Act;
(b) "board" means the Labour Relations Board referred to in the Labour Relations Act;
(c) "committee" means an occupational health and safety committee referred to in this Act;
(d) "council" means the Occupational Health and Safety Council referred to in this Act;
(d.1) "department" means the department presided over by the minister;
(e) "division" means the Occupational Health and Safety Division;
(f) "employer" means a person who employs one or more workers;
(g) "minister" means the minister appointed under the Executive Council Act to administer this Act;
(h) "occupation" means employment prescribed by the regulations as an occupation;
(i) "officer" means an occupational health and safety officer appointed under this Act and includes a medical practitioner providing services under section 20 while the medical practitioner is providing those services;
(j) "principal contractor" means the person primarily responsible for the carrying out of a project and includes the person who owns the thing in respect of which the project is being carried out;
(k) "self-employed person" means a person who is engaged in an occupation on the person's own behalf;
(k.1) "supervisor" means a person authorized or designated by an employer to exercise direction and control over workers of the employer;
(l) "supplier" means a person who rents or leases tools, appliances or equipment to be used by a worker;
(m) "worker" means a person engaged in an occupation; and
(n) "workplace" means a place where a worker or self-employed person is engaged in an occupation and includes a vehicle or mobile equipment used by a worker in an occupation.
[S.N.L. 1999, c. 28, s. 1; 2006, c. 16, s. 1; 2009, c. 19, s. 1; 2023, c. 15, s. 1]
Section 6 Workers' general duty
6. A worker, while at work, shall take reasonable care to protect the worker's own health and safety and that of workers and other persons at or near the workplace.
[S.N.L. 2023, c. 15, s. 6]
Section 7 Specific duties of workers
7. A worker
(a) shall co-operate with the worker's employer and with other workers in the workplace to protect
(i) the worker's own health and safety,
(ii) the health and safety of other workers engaged in the work of the employer,
(iii) the health and safety of other workers or persons not engaged in the work of the employer but present at or near the workplace;
(a.1) shall use devices and equipment provided for the worker's protection in accordance with the instructions for use and training provided with respect to the devices and equipment;
(b) shall consult and co-operate with the occupational health and safety committee, the worker health and safety representative or the workplace health and safety designate at the workplace; and
(c) shall co-operate with a person exercising a duty imposed by this Act or regulations.
[S.N.L. 1999, c. 28, s. 3; 2001, c. 10, s. 26; 2004, c. 52, s. 2; 2023, c. 15, s. 7]
Section 37 Committees
37. Where 20 or more workers are employed at a workplace, the employer shall establish an occupational health and safety committee to monitor the health, safety and welfare of the workers employed at the workplace.
[S.N.L. 1999, c. 28, s. 9; 2023, c. 15, s. 24]
Section 38 Membership of committees
38. (1) A committee shall consist of the number of persons that may be agreed to by the employer and the workers but shall not be less than 2 nor more than 12 persons.
(2) At least half of the members of a committee are to be persons representing the workers at the workplace who are not connected with the management of the workplace.
(3) The persons representing the workers on the committee are to be elected by other workers at the workplace or appointed in accordance with the constitution of the union of which the workers are members.
(4) Where the employer and workers cannot agree on the size of the committee, the minister may establish its size.
(5) The employer shall appoint sufficient employer representatives to ensure that the committee may function.
(6) The employer and worker members of a committee shall elect a co- chairperson from their respective groups.
(7) The employer shall post the names of the committee members in a prominent place at the workplace.
Section 39 Duties of committees
39. A committee established under section 37
(a) shall seek to identify aspects of the workplace that may be unhealthy or unsafe;
(a.1) shall participate in a workplace inspection that an employer is required by the regulations to conduct;
(b) may make recommendations to principal contractors, employers, workers, self-employed persons and the assistant deputy minister or an officer for the enforcement of standards to protect the health, safety and welfare of workers at the workplace;
(c) shall receive complaints from workers as to their concerns about the health and safety of the workplace and their welfare;
(d) shall establish and promote health and safety educational programs for workers;
(e) shall maintain records as to the receipt and disposition of complaints received from workers under paragraph (c);
(f) shall co-operate with the assistant deputy minister or an officer who is exercising duties under the Act; and
(g) shall perform those other duties and follow those procedures that may be prescribed by the regulations.
[S.N.L. 2001, c. 10, s. 29; 2023, c. 15, s. 26]
Section 40 Meetings of committee
40. Meetings of a committee shall take place during regular working hours at least once every 3 months and a worker is not to suffer loss of pay or other benefits while engaged in a meeting of a committee.
Section 41 Worker representative
41. (1) Where less than 20 workers are employed at a workplace, the employer shall ensure that a worker not connected with the management of the workplace is designated as the worker health and safety representative to monitor the health, safety and welfare of workers employed at the workplace.
(2) The employer shall provide and pay for training for the worker health and safety representative.
(3) The training provided under subsection (2) shall meet the requirements the Workplace Health Safety and Compensation Commission may set.
(4) The worker health and safety representative shall participate in the training provided under this section.
(5) An employer shall compensate a worker for participating in training under this section as if the training were regular work.
[S.N.L. 2001, c. 10, s. 30; 2004, c. 47, s. 27; 2023, c. 15, s. 27]
Section 42 Election of representative
42. The worker health and safety representative is to be elected by other workers at the workplace or appointed in accordance with the constitution of the labour union of which the workers are members.
Section 43 Posting name
43. The employer shall post the name of the worker health and safety representative or the workplace health and safety designate in a prominent place at the workplace.
[S.N.L. 2004, c. 52, s. 9]
Section 44 Duties of representative
44. (1) A worker health and safety representative or the workplace health and safety designate has the same duties as those imposed upon a committee under section 39, where that is reasonably practicable.
(2) A worker health and safety representative or the workplace health and safety designate, where the workplace health and safety designate is not the employer, shall consult with the employer while performing duties under subsection (1).
(3) Where the workplace health and safety designate is the employer, the workplace health and safety designate shall consult with the workers while performing duties under subsection (1).
[S.N.L. 2004, c. 52, s. 10; 2023, c. 15, s. 28]
Occupational Health and Safety Regulations, 2012
N.L.R. 5/12
Part III GENERAL DUTIES
Section 12 Occupational health and safety program
12. (1) An occupational health and safety program required under section 36.1 of the Act shall be signed and dated by the employer and by the person or persons responsible for the management of the employer's operations in the province and shall include:
(a) a statement of the employer's commitment to cooperate with the occupational health and safety committee and workers in the workplace in carrying out their collective responsibility for occupational health and safety;
(b) a statement of the respective responsibilities of the employer, supervisors, the occupational health and safety committee and workers in carrying out their collective responsibility for occupational health and safety;
(c) procedures to identify the need for, and for the preparation of written safe work procedures to implement health and safety practices, including practices required by the Act and the regulations, or as required by an officer;
(d) written work procedures appropriate to the hazards and work activity in the workplace;
(e) a plan for orienting and training workers and supervisors in workplace and job-specific safe work practices, plans, policies and procedures, including emergency response, that are necessary to eliminate, reduce or control hazards;
(f) provisions for establishing and operating an occupational health and safety committee, including provisions respecting
(i) maintenance of membership records,
(ii) procedural rules,
(iii) access by the committee to management staff with the authority to resolve health and safety issues and to information about the employer's operations required under the Act and the regulations, and
(iv) a plan for training committee members as required under the Act;
(g) a system for the recognition, evaluation and control of hazards that includes:
(i) evaluation and monitoring of the workplace to identify potential hazards and the associated risks,
(ii) procedures and schedules for regular inspections by management and committee members,
(iii) procedures for the identification, reporting and control or correction of hazards,
(iv) procedures for the prompt investigation of hazardous occurrences to determine the cause of the occurrence and the actions necessary to prevent a recurrence,
(v) identification of the circumstances where the employer is required to report hazards to the committee and the procedures for doing so, and
(vi) measures for the accountability of persons responsible for the reporting and correction of hazards;
(h) a plan for the control of biological and chemical substances handled, used, stored, produced or disposed of at the workplace and where appropriate, the monitoring of the work environment to ensure the health and safety of workers and other persons at or near the workplace;
(i) a system to ensure that persons contracted by the employer or for the employer's benefit comply with the program developed under this section and the Act and regulations;
(j) an emergency response plan;
(k) maintenance of records and statistics, including occupational health and safety committee minutes, reports of occupational health and safety inspections and investigations, with procedures to allow access to them by persons entitled to receive them under the Act; and
(l) provision for monitoring the implementation and effectiveness of the program.
(2) An employer that is required to establish and maintain an occupational health and safety program under section 36.1 of the Act shall
(a) implement the occupational health and safety program; and
(b) review and, where necessary, revise the occupational health and safety program as follows:
(i) at least every 3 years,
(ii) where there is a change of circumstances that may affect the health and safety of workers, and
(iii) where an officer requests a review.
Section 17 General duties of workers
17. (1) A worker shall make proper use of all necessary safeguards, protective clothing, safety devices, lifting devices or aids, and appliances
(a) designated and provided for the worker’s protection by the employer; or
(b) required under these regulations to be used or worn by a worker.
(2) A worker shall follow the safe work procedure in which the worker has been instructed.
(3) A worker shall immediately report a hazardous work condition that may come to the worker’s attention to the employer or supervisor.
[N.L.R. 43/22, s. 4]
Part V GENERAL HEALTH AND SAFETY REQUIREMENTS
Section 38 Emergency plan risk assessment
38. (1) An employer shall conduct a risk assessment in a workplace in which a need to rescue or evacuate workers may arise.
(2) Where the risk assessment required by subsection (1) shows a need for evacuation or rescue, appropriate written procedures shall be developed and implemented and a worker assigned to coordinate their implementation.
(3) Written rescue and evacuation procedures are required for but not limited to
(a) work at high angles;
(b) work in confined spaces or where there is a risk of entrapment;
(c) work with hazardous substances;
(d) underground work;
(e) work in close proximity to power lines;
(f) work on or over water; and
(g) workplaces where there are persons who require physical assistance to be moved.
(4) Where a workplace is a low risk workplace in the opinion of an employer, the employer shall post information about escape routes and conduct emergency drills the employer considers appropriate.
[N.L.R. 43/22, s. 10]
Part VI OCCUPATIONAL HEALTH REQUIREMENTS
Section 42 Hazardous substances
42. (1) An employer shall monitor the use or presence of substances at the workplace that may be hazardous to the health and safety of workers.
(2) In accordance with subsection (1), an employer shall implement a chemical and biological control program commensurate with the associated risks.
(3) In accordance with subsection (1), an employer shall eliminate hazardous substances from the workplace and where this is not practicable substitute a less hazardous substance.
(4) Where hazardous substances exist, an employer shall employ engineering and administrative controls to ensure their safe use.
(5) An employer shall ensure that a substance produced, used or handled at a workplace which by reason of toxicity, flammability or reactivity creates a risk to the health or safety of workers is controlled in accordance with the Safety Data Sheet or manufacturer's specifications.
(6) Where the minister determines that the use or presence of a hazardous substance at a place of employment may be injurious to the health of workers, the minister may inquire into the substance and may prohibit, restrict or modify the use of the substance until a time that an employer establishes to the minister that its use or presence is not injurious to the health of workers.
(7) An employer shall ensure that
(a) atmospheric contamination of the workplace by hazardous substances is kept as low as is reasonably practicable;
(b) a worker is informed of the nature and degree of health effects of the hazardous substances to which the worker is exposed;
(c) exposure of a worker to hazardous substances is as minimal as is reasonably practicable, and where a threshold limit value has been established by the ACGIH, exposure shall not exceed the threshold limit value;
(d) except as otherwise determined by the division, a worker is not exposed to a substance that exceeds the ceiling limit, short-term exposure limit or 8-hour TWA (time weighted average) limit prescribed by ACGIH; and
(e) where a substance referred to in paragraph (d) has an 8-hour TWA limit, a worker's exposure to the substance does not exceed
(i) 3 times the 8-hour TWA limit for more than a total of 30 minutes during the work period, and
(ii) 5 times the 8-hour TWA limit.
(8) Where extended work periods exist where the work period is more than 8 hours in a 24 hour day, the 8 hour exposure shall be adjusted accordingly as outlined in the ACGIH "Threshold Limit Values (TLVs)" Manual.
(9) Adjustment of TLVs, as required, shall be done in consultation with the occupational health and safety committee, the worker health and safety representative or the workplace health and safety designate, as appropriate.
(10) Where a worker is exposed to a substance which is designated as a reproductive toxin or a sensitizer, an employer shall develop policy and procedures appropriate to the risk, which may include protective reassignment.
(11) Where workers may be exposed to contact with chemicals harmful to the skin, facilities shall be available for the worker to effectively cleanse the contaminated body areas, including, where corrosive chemicals are involved, emergency water baths, showers, jump tanks, eyewash facilities or other effective means of treatment.
(12) The policy and procedures required by subsection (10) shall include
(a) informing workers about the reproductive toxin and identifying ways to minimize exposure to the toxin for a worker who has advised the employer of pregnancy or intent to conceive a child; and
(b) identifying ways to eliminate exposure to a sensitizer for a worker who is or may become sensitized to that substance.
(13) Solvents, oils, greases, paints or other flammable substances shall be cleaned up by using an approved non-combustible grease and oil absorbent which shall be placed in covered metal containers before disposal.
(14) Containers referred to in subsection (13) shall not be stored in work areas.
[S.N.L. 2019, c. 8, s. 20]
Section 43 Health surveillance
43. (1) In accordance with subsection 42(2), an employer shall assess the need for and extent of health surveillance of the employer’s workers.
(2) Based on the results of the assessment under subsection (1), an employer shall establish and maintain a program for the surveillance of the health of workers, which shall be in accordance with the following guidelines
(a) the International Code of Ethics for Occupational Health Professionals; and
(b) the International Labour Organization's Technical and Ethical Guidelines for Health Surveillance.
(3) In addition, to subsections (1) and (2), the minister may
(a) designate a workplace or class of workplaces as requiring an occupational health surveillance program; or
(b) make requirements for modifications to an occupational health surveillance program.
(4) An employer shall ensure that an occupational health surveillance program in a workplace is communicated to employees of that workplace.
(5) The minister may require a worker to undergo a medical examination as part of a health surveillance program where it may be necessary for the prevention of occupational disease.
(6) A medical examination shall be performed during normal working hours without loss of pay to workers.
(7) Where the minister has been advised by a physician that a worker has been adversely affected by a hazardous substance in the workplace and requires temporary removal or workplace accommodation from that workplace or hazard, the minister may require the employer to provide without loss of pay to the worker temporary alternative work for the time period required.
(8) An employer shall keep records of a health surveillance program for a period of time specified by the minister, and these records shall be made available to
(a) an employee who requests information pertaining to the employee’s health surveillance records; and
(b) where a physician is no longer able to keep medical records pertaining to an occupational exposure, the minister shall be notified in advance to make alternate arrangements that are in accordance with the guidelines of the College of Physicians and Surgeons of Newfoundland and Labrador regarding the retention and storage of medical records.
[N.L.R. 43/22, s. 12]
Section 46 Silica regulation
46. (1) In this section
(a) "blasting" means the cleaning, smoothing, roughening or removing of part of the surface of an article by the use as an abrasive of a jet of sand, metal shot or grit or other material propelled by compressed air or steam or by a wheel;
(b) "blasting chamber" means a blasting enclosure into which workers enter;
(c) "blasting enclosure" means a chamber, barrel, cabinet or other similar enclosure designed for the purpose of blasting in it;
(d) "cleaning of castings" means, where done as an incidental or supplemental process in connection with the making of metal castings, the freeing of the castings from adherent sand or other substance, and includes the removal of cores and the general smoothing of the castings where the freeing is done, but does not include the freeing of castings from scale formed during annealing or heat treatment;
(e) "sandblasting" means the process of projecting sand by means of compressed air or steam or by a wheel;
(f) "silica dust" means dust of respirable particle size and composed substantially of uncombined silica (Silicon Dioxide SiO2);
(g) "silica flour" means the ground material produced by the milling of siliceous rocks or other siliceous substances, including diatomite (Kieselguhr, diatomaceous earth);
(h) "uncombined silica" means silica which is not combined chemically with another element or compound; and
(i) "use of a parting material" means the application of a material to a surface of a pattern or of a mould to facilitate the separation of the pattern from a mould or the separation of parts of the mould.
(2) The provisions of this section apply wherever workers are employed in a silica process, including
(a) sandblasting;
(b) the cleaning of castings;
(c) the blasting, fettling, grinding or dressing of a surface containing silica, including the engraving or abrasive cleaning of gravestones, buildings or structures of siliceous stones or rocks;
(d) a process in which silica flour is used;
(e) the manufacture of silica-containing refractory bricks or silica-containing substances and the dismantling or repair of the refractory lining of furnaces;
(f) a process which the chief occupational medical officer has reason to believe creates a risk to the health of workers by silica dust; and
(g) a process that includes the getting, cutting, splitting, crushing, grinding, milling, drilling, sieving, or other mechanical manipulation of gravel or siliceous stone or rock where there is potential for exceeding 1% free silica or 50% of TLV.
(3) An employer shall ensure that at every silica process except sandblasting to which subsection (12) applies, the entry into the air of silica dust is prevented where reasonably practicable by the provision of
(a) total or partial enclosure of the process;
(b) efficient local exhaust ventilation;
(c) jets or sprays of water or other suitable wetting agent; and
(d) another method considered suitable by the assistant deputy minister.
(4) An employer shall ensure that
(a) enclosure apparatus and exhaust ventilation equipment used or likely to be used to contain silica dust is maintained and is inspected at least once in every 7 days and is certified by a competent person at least once in every calendar year; and
(b) effective means is provided to collect silica dust removed by exhaust ventilation equipment and to prevent its re-entry into a workroom, and every filtering or settling device situated in a workroom is completely separated from the general air of that workroom in an enclosure ventilated to the open air.
(5) Where it is not reasonably practicable to prevent the entry into the air of silica dust, the employer shall provide for the isolation of the worker from the air containing silica dust.
(6) Where it is not reasonably practicable to prevent the entry into the air of silica dust nor practicable to isolate the worker from the air containing silica dust, and for all cleaning and maintenance work, the employer shall provide for the use of each worker who may be exposed to silica dust
(a) approved respiratory protective equipment; and
(b) protective clothing, including coveralls and headgear, that, when worn, exclude silica dust and that is maintained and cleaned in a safe manner.
(7) A worker shall not be required to perform work for which respiratory protective equipment and clothing is provided unless fully instructed in the need for and proper use of that equipment and clothing.
(8) An employer shall ensure that all places where silica dust may accumulate are regularly cleaned using vacuum methods wherever practicable.
(9) An employer shall ensure that the standard for dust levels does not exceed the threshold limit value (TLV) established by the ACGIH.
(10) A worker who in the course of the worker’s employment is likely to be engaged in a silica process shall be warned by the employer of the danger to the worker’s health of inhaling silica dust and that the risk of injury is made greater by smoking.
(11) Persons under the age of 18 shall not be employed in a silica process nor in cleaning or maintenance work likely to involve exposure to silica dust except work that is a recognized part of apprenticeship or comparable course of training.
(12) An employer shall ensure that
(a) sandblasting is not done outside a blasting enclosure to an article which it is practicable to introduce into a blasting enclosure;
(b) sand or other substance containing more than 1% by weight of respirable dust is not introduced into a blasting enclosure;
(c) sandblasting is not done except with the written permission of the officer and in accordance with the conditions and to the extent that the officer may prescribe; and
(d) sandblasting is not done underground,
and sandblasting shall not be undertaken nor performed by an employer, worker or self-employed person other than those registered for that purpose with the division.
(13) An employer shall ensure where practicable that castings, gravestones and other articles which are liable to give rise to silica dust by blasting are not blasted except in a blasting enclosure, and that work is not performed in a blasting enclosure except blasting and work immediately incidental to that and the cleaning and repairing of the enclosure and of plant and appliances situated in that enclosure.
(14) An employer shall ensure that every blasting enclosure which is liable to contain silica dust is
(a) constructed, operated and maintained to prevent the escape of dust;
(b) provided with an efficient dust extraction system, which is kept in continuous operation whenever the blasting enclosure is in use whether or not blasting is actually taking place, and a blasting chamber is in operation when a worker is inside the chamber;
(c) specially inspected by a competent person once in every week in which it is used for blasting, and the enclosure, the apparatus connected with it and the ventilating plant associated with it is thoroughly examined and tested by a competent person once every month, and all results of required inspection, examinations and tests are recorded and all defects remedied without avoidable delay; and
(d) provided with efficient apparatus for separating where practicable the abrasive from other dust, and the abrasive is not again introduced into the blasting apparatus until it has been separated.
(15) An employer shall provide and maintain for workers who work in a blasting chamber, whether in blasting or other work, protective blasters' helmets supplied with clean and not unreasonably cold air of not less than 6 cubic feet a minute, and the helmets shall be used by workers whenever they are in the blasting chamber.
(16) Suitable gauntlets and coveralls shall be provided for the use of, and shall be worn by, all workers while performing blasting or assisting at blasting, and suitable provision shall be made for the storage, regular cleaning by vacuum and maintenance in good condition of the gauntlets and coveralls.
(17) When a worker is engaged in the cleaning of a blasting apparatus or enclosure, ventilating or separating plant, or the surrounds, all practical measures shall be taken to prevent the inhalation of silica dust or its dissemination into the air and all the cleaning shall be by vacuum or hosing by water whenever practicable.
(18) An employer shall ensure that silica flour
(a) is not manufactured except under standards prescribed by the division;
(b) is not used for a purpose for which a less hazardous substance may be substituted; and
(c) is not used in the manufacture of scouring powder or abrasive soaps or as an abrasive in a process.
(19) The examining physician shall record in the log the date and nature of the certificate the examining physician issues to each worker the examining physician has medically examined.
[N.L.R. 43/22, s. 13]
Section 47 Silica medical surveillance
47. (1) An employer shall establish and maintain a system for the surveillance of the health of employees arising from silica dust exposure in accordance with the silica health surveillance guidance document prescribed by the minister.
(2) An employee who requires silica related health surveillance is one who:
(a) works in an industry where the employee is potentially affected by a silica process as defined in this subsection 46(2);
(b) is potentially exposed to silica levels in excess of the ACGIH TLV- TWA; and
(c) has been determined, through the company's silica control program, to require silica health surveillance as prescribed in the general health surveillance section.
(3) An employer shall not regularly employ a worker in a silica process unless the employer has been assured by a medical practitioner by a written notification that the worker is medically fit for the work being undertaken.
(4) An employer shall keep at the place of employment to be readily available to an officer a log recording the name of every worker referred for medical examination.
(5) The initial health assessment shall be carried out under the direction of a physician and shall include
(a) an occupational history;
(b) a respiratory questionnaire;
(c) a pulmonary/lung function test;
(d) a chest x-ray (Full size PA view); and
(e) a medical history and physical examination emphasizing the respiratory system.
(6) A periodic health assessment shall comply with the following requirements:
(a) the frequency of chest x-rays shall be in accordance with the silica health surveillance document;
(b) the medical examination emphasizing the respiratory system shall be repeated annually unless prescribed otherwise by the physician; and
(c) the pulmonary /lung functions tests including FEV1, FVC, and DLCO standardized for alveolar volume shall be repeated annually unless prescribed otherwise by the physician.
(7) Where an employee is undergoing health surveillance for silica, the physician shall ensure, as soon as practicable, that
(a) the employee is notified of the results, together with a necessary explanation of these results;
(b) the employer is notified of the general outcome of a worker's health surveillance and is advised on the need for remedial actions; and
(c) the minister is notified of a prescribed adverse health effect that had been detected which is consistent with exposure to silica.
(8) Where an employer has been advised by the physician on the need for remedial action, the employer shall, as soon as practicable, re-evaluate the assessment of the employee's exposure to silica and implement the control measures required.
(9) An employer shall ensure employees are informed of the purpose and procedures for health surveillance and make arrangements for employees to participate in the health surveillance program.
[N.L.R. 43/22, s. 14]
Section 48 Asbestos
48. (1) When work or manufacturing processes cause or are likely to cause workers to be exposed to asbestos, or dusts containing asbestos, means shall be provided to control asbestos dust from exceeding the threshold limit value established by the ACGIH or lower where practically attainable.
(2) Dust arising from the cutting and shaping of block and pipe insulation materials, whether by power saws or hand saws, shall be controlled by adequate local exhaust ventilation with the discharged air passed through an effective filter.
(3) Where mortar containing asbestos is mixed, dust concentrations shall be controlled by adequate local exhaust ventilation with discharged air passed through an effective filter or other effective means.
(4) Where work is being done with asbestos containing materials, dust concentrations shall be controlled through adequate local exhaust ventilation with discharged air passed through an effective filter or other effective means.
Section 49 Lead exposure control plan
49. (1) An employer shall develop an exposure control plan for lead where
(a) a worker at a work site may be exposed to airborne lead in excess of its occupational exposure limit for more than 30 days in a year; or
(b) a worker's exposure to lead at a work site could result in an elevated body burden of lead through a route of entry.
(2) The exposure control plan shall include
(a) a statement of purpose and the responsibilities of individuals;
(b) methods of hazard identification, assessment and control;
(c) worker education and training;
(d) safe work practices as required;
(e) descriptions of personal and work site hygiene practices and decontamination practices;
(f) processes of health monitoring, including biological testing;
(g) methods of documentation and record keeping; and
(h) procedures for maintenance of the plan, including annual reviews and updating.
(3) A worker shall follow the exposure control plan and practice the personal and work site hygiene practice established by the employer to minimize lead exposure at the work site.
(4) Where there is potential for a worker to be exposed to lead in harmful amounts at a work site, an employer shall ensure that air monitoring and surface testing for lead is regularly conducted to confirm that the controls in place are effective.
(5) Where a worker at a work site could reasonably be expected to have an elevated body burden of lead, an employer shall establish a system for the surveillance of the health of their employees arising from lead exposure in accordance with the lead health surveillance guidance document as prescribed by the minister.
(6) An employer shall ensure that a worker who has been exposed to lead is informed of the health surveillance requirements.
Section 57 Permitted quantities
57. (1) The amount of a hazardous substance in a work area shall not exceed the quantity reasonably needed for work in progress, normally in one work shift.
(2) Bulk or reserve quantities of a hazardous substance shall be stored in a designated area separate from the work area.
Section 58 Incompatible substances
58. Substances which are incompatible shall not be stored in a manner that would allow them to mix in the event of container leakage, breakage or other similar circumstance.
Section 59 Storage of hazardous substances
59. (1) A hazardous substance shall be stored in a designated area, in a manner which ensures that it can not readily fall, become dislodged, suffer damage, or be exposed to conditions of extreme temperature.
(2) A designated storage area for a hazardous substance shall be
(a) designed and constructed to provide for the safe containment of the contents;
(b) clearly identified by signs, placards or similar means;
(c) designed and maintained to allow the safe movement of workers, equipment and material;
(d) provided with adequate ventilation and lighting; and
(e) in a location not normally occupied by workers, including a lunchroom, eating area, change room, clothing storage locker or passenger compartment of a vehicle.
Section 60 Dispensing
60. Where a flammable liquid is dispensed or transferred inside a flammable liquids storage room,
(a) the storage room shall be mechanically ventilated at a rate of at least 18 m3/hr a square metre of floor area (1 cfm/sq ft), but not less than 250 m3/hr (150 cfm);
(b) exhaust air shall be discharged to the outdoors, and makeup air provided;
(c) makeup air duct passing through a fire separation shall be equipped with an approved fire damper; and
(d) doors shall be self-closing.
Section 62 Washing facilities
62. (1) An employer shall provide and maintain for the use of workers
(a) adequate and suitable facilities for personal washing; and
(b) a supply of clean hot and cold or warm water, soap and clean towels or other suitable means of cleaning or drying.
(2) Where there is a high risk of contamination of workers by hazardous substances, infectious or offensive materials as a part of the regular work processes at a place of employment, an employer shall
(a) where reasonably practicable, provide and maintain suitable, adequate and clean facilities for changing and showering; and
(b) allow sufficient time during normal working hours for a worker to use those facilities without loss of pay or other benefits.
Section 63 Emergency washing facilities
63. An employer shall ensure that
(a) appropriate emergency washing facilities are provided in a work area where a worker's eyes or skin may be exposed to harmful or corrosive materials or other materials which may burn or irritate;
(b) only a potable water supply is used in a plumbed emergency eyewash facility and that only potable water or an isotonic saline flushing solution is used in a portable (non-plumbed) eyewash unit;
(c) access to emergency eyewash and shower facilities is not blocked by material or equipment; and
(d) selection of emergency washing facilities is based upon an assessment of the risks present in the workplace.
Section 64 Work clothing and accommodations
64. (1) An employer shall provide and maintain, for the use of workers, clean, adequate, appropriately located and suitable accommodations for street clothing not worn during working hours and where it is necessary to protect the street clothing from becoming wet, dirty or contaminated by work clothing, separate accommodation shall be provided.
(2) Where a worker's work clothing or skin is likely to be contaminated by hazardous substances, an employer shall
(a) provide protective clothing and head cover appropriate to the work and hazard;
(b) provide a suitably located changing area; and
(c) ensure that the clothing and head cover are handled and cleaned or disposed of in a manner that prevents worker exposure to hazardous substances.
Section 69 Painting, coating and working with plastics/resins
69. (1) This section applies to a workplace in which there is spraying or the use of paint or a similar coating, fibre-reinforced resin, thermoplastic material, an expandable resin form or other similar materials.
(2) Spraying a flammable or other hazardous product is prohibited within a general work area unless effective controls have been installed to control the fire, explosion and toxicity hazards.
(3) Where practicable, a coating shall not be applied to a material that is about to be welded.
(4) A work area or enclosure where hazardous materials are handled or used shall be posted with suitable signs or placards warning workers of the hazards within the identified restricted access area and stating the precautions for entry into the area.
(5) Where practicable, a ventilated spray booth or other enclosure designed to control worker exposure shall be used during
(a) an operation or process which involves spraying paint or resin;
(b) lay-up or moulding of reinforced plastic; or
(c) an application of a paint, coating or insulation containing a sensitizer including an isocyante compound, or similar operations using toxic materials.
(6) The air velocity through a horizontal flow spray booth, a vertical flow, down-draft or other enclosure required by subsection (5) shall be as prescribed by a standard acceptable to the minister.
(7) In outdoor applications of materials or processes listed in subsection (5), an air velocity across the work area of at least 50 fpm shall be assured, by mechanical means where necessary, to carry vapours and aerosols away from the breathing zone of a worker.
(8) A ventilation system subject to heavy concentrations of over-spray from the operation shall have an arrester filter which is maintained in good operating condition and replaced when the pressure drop across the filter exceeds the design criteria.
(9) A worker who is or may be exposed to an airborne contaminant generated by a spray operation involving a sensitizing agent shall be provided with and shall wear air-supplied respiratory protection.
(10) Only a qualified person authorized by the employer may operate
(a) an airless spray unit of the type which atomizes paint and fluid at pressure;
(b) a spray paint powered by compressed air in excess of 10 psi; or
(c) a chopper spray gun unit.
(11) An airless spray gun shall have
(a) a means to electrically bond the gun to the paint reservoir and pump;
(b) a guard that protects against trigger activation where the gun is dropped; and
(c) a trigger function configured to require two distinct operations by the user to activate the release of paint or fluid through the nozzle, or a safety device which prevents the nozzle tip from coming into contact with the worker.
(12) Emissions from operations involved in heating plastics to temperatures which may release thermal decomposition products shall be removed from the workplace by local exhaust ventilation when there is a risk of harm to a worker from exposure to these emissions.
(13) A resin foam installation process performed indoors shall be controlled or contained so that an unprotected worker is not exposed to emissions by using an enclosure or portable local exhaust ventilation or by scheduling arrangements.
(14) A resin foam installation process performed outdoors and relying on natural ventilation shall be completed in an area restricted to authorized personnel wearing adequate personal protective equipment.
(15) Safe work procedures shall be developed for lead paint removal operations, including provisions for warning unauthorized persons, worker training, containment, ventilation, work practices, personal protective equipment worker decontamination and safe means of disposal.
Part VIII MACHINERY AND EQUIPMENT
Section 118 Abrasive blasting and high pressure washing definitions
118. For the purpose of this section and sections 119 to 126,
(a) "cabinet" means an enclosure designed to permit abrasive blasting, high pressure washing or a similar operation to be conducted safely inside the enclosure by a worker who is outside the enclosure;
(b) "enclosure" means a temporary or permanent enclosure of a work area provided with exhaust ventilation and makeup air to reduce exposure of workers inside the enclosure and prevent the uncontrolled release of air contaminants from the enclosure; and
(c) "high pressure washing" or "jetting" means the use of water or other liquid delivered from a pump at a pressure exceeding 34 MPa (5,000 psi), with or without the addition of solid particles, to remove unwanted matter from a surface or to penetrate into the surface of a material for the purpose of cutting that material.
Section 119 Risk assessment
119. An employer shall ensure that a risk assessment is done before any abrasive blasting activity, high pressure washing process, or related cleanup is started which may cause release of a harmful level of an air contaminant from a surface or coating containing a toxic heavy metal or hazardous substance.
Section 120 Work procedures outside a cabinet
120. Where abrasive blasting, high pressure washing or a similar operation is conducted by a worker outside a cabinet, written safe work procedures addressing the hazards and necessary controls shall be prepared and implemented by the employer.
Section 121 Substitution of abrasive blasting materials
121. Abrasive blasting materials containing crystalline silica shall be replaced with less toxic materials, where practicable.
Section 122 Cleanup
122. (1) Used abrasive blasting materials which contain a hazardous substance shall be removed from the work area using effective procedures designed to minimize the generation of airborne dust and wearing suitable personal protective equipment.
(2) Removal under subsection (1) shall take place by the end of each shift except where
(a) a risk assessment establishes that the risks from removal exceed the risks from leaving the materials in place;
(b) a worker will not be exposed to the materials before removal occurs; or
(c) the materials cannot be separated from the environment in which the abrasive blasting takes place.
(3) Where removal is delayed under subsection (2), an employer shall assess the risks arising from delay and develop written safe work procedures.
Section 123 Engineering controls
123. Engineering controls, including an enclosure or local exhaust ventilation with dust collection, shall be used to maintain airborne contaminant levels below exposure limits, where practicable.
Section 124 Exhaust ventilation
124. (1) Where abrasive blasting or a similar operation is conducted within a structure, the process shall be isolated in a separate, properly ventilated enclosure or cabinet to minimize worker exposure to air contaminants generated by the process.
(2) Where abrasive blasting or a similar operation is conducted inside an enclosure or cabinet, the enclosure or cabinet shall have exhaust ventilation that
(a) maintains air pressure below the air pressure outside the enclosure or cabinet, to prevent the escape of air contaminants from the enclosure or cabinet to other work areas; and
(b) minimizes worker exposure inside the enclosure.
Section 125 Restricted work zones
125. (1) Where abrasive blasting or a similar operation is conducted outside a structure, the process shall be restricted to a work zone which is identified by warning signs or similar means as a contaminated area.
(2) Only a properly protected worker who is necessary to perform the work shall be permitted inside an enclosure or a restricted work zone where abrasive blasting or a similar operation is conducted.
Section 126 Operating procedures
126. (1) The operating controls for a sandblasting machine or jetting gun shall be
(a) located near the nozzle in a position where the operator's hands are when using the device;
(b) a continuous pressure type that immediately stops the flow of material when released; and
(c) protected from inadvertent activation.
(2) Where hand operated controls are impracticable, subsection (1)(a) does not apply and an operator shall use a foot operated control or equivalent safety device, of a design acceptable to the minister.
(3) A jetting gun shall not be modified except as authorized by the manufacturer.
(4) A worker shall not hand hold an object while it is being cleaned or cut by a jetting gun.
(5) High pressure hoses, pipes, and fittings shall be supported to prevent excessive sway and movement.
(6) A nozzle or jetting gun operator shall wear personal protective clothing and equipment on the body, hands, arms, legs and feet, including the metatarsal area, made of canvas, leather or other material which will protect the worker's skin from injury in the event of contact with the flow from the nozzle.
(7) Except where the process is isolated from the operator in a separate cabinet, suitable respiratory protective equipment shall be provided and worn whenever abrasive blasting or a similar operation is conducted.
Part XVII CONSTRUCTION, EXCAVATION AND DEMOLITION
Section 398 Hazardous materials
398. Before work begins on the demolition or salvage of machinery, equipment, buildings or structures, the employer or owner shall
(a) inspect the site to identify asbestos, lead, biological or other heavy metal or toxic, flammable or explosive materials that may be handled, disturbed or removed;
(b) make the results of the inspection available at the worksite, including drawings, plans or specifications showing the location of hazardous substances;
(c) ensure that hazardous materials found are safely contained or removed; and
(d) where hazardous materials that were not identified in the inspection under paragraph (a) are discovered during demolition work, ensure that all work ceases until those materials are contained or removed.
Part XVIII EXCAVATION, UNDERGROUND WORK AND ROCK CRUSHING
Section 413 Air quality
413. (1) An employer shall ensure that
(a) the respirable air in all underground workings is free from hazardous amounts of dusts, vapours and gases, and does not contain less than 20% oxygen; and
(b) appropriate tests for harmful vapour, gases, fumes, mists, dusts or explosive substances and oxygen deficiency are made and recorded
(i) before entry,
(ii) after an interruption in the work procedures, and
(iii) at appropriate intervals.
(2) An employer who employs workers at a mine or quarry where silica is mined or quarried, or where it is present, shall comply with the Silica Code of Practice.
(3) The tests required under paragraph (1)(b) shall be performed by a person who has appropriate training in the proper use of testing and monitoring equipment.
(4) A worker employed in surface rock-excavating workings shall be protected from harmful dust concentrations by
(a) the use of suppression;
(b) dust removal by mechanical means; or
(c) another acceptable engineering control.
(5) Where a worker is exposed to dusting resulting from loading, transporting or conveying rock at surface operations, the dust shall be reduced to non-harmful concentrations by the application of water or by other effective methods.
(6) An employer shall ensure that dust caused by drilling or handling rock at underground rock-excavating workings is effectively suppressed by a means acceptable to the division.
(7) A rock drill, that is, a machine or device for drilling a hole in rock for the purpose of blasting, usually powered by compressed air but in which electricity or steam may be used, shall be equipped with a water jet, spray or other device acceptable to the minister to effectively suppress drilling dust.
(8) Subsection (7) does not apply to hand-drilling procedures.
(9) A water spray shall be used in every development heading unless written permission has been received from the assistant deputy minister to work the heading without a water spray.
(10) Effective dust-control measures shall be employed during the handling and loading of broken rock.
(11) Mechanical ventilation shall be provided to produce a minimum air volume of 15.24 cubic metres a minute a square metre of working face in the work area.
Part XX FIRE PREVENTION AND CONTROL
Section 443 Fire protection
443. (1) The design and occupancy of structures and the provision of fire alarm and detection equipment and fire protection equipment, in places of employment, shall comply with the Fire Prevention Act, 1991 and an employer shall ensure that work is carried out according to the applicable provisions of that Act and the National Fire Code.
(2) Fire alarm and detection equipment and fire protection equipment shall be maintained according to the manufacturer's instructions and any other requirements of provincial legislation.
(3) An employer that has
(a) controlled products as defined in the Workplace Hazardous Materials Information System (WHMIS) Regulations, 2018 ;
(b) explosives;
(c) pesticides;
(d) radioactive material;
(e) consumer products; or
(f) hazardous waste
in quantities which may endanger fire-fighters at a workplace shall ensure that the local fire department is notified of the nature and location of the hazardous materials or substances and methods to be used in their safe handling.
(4) Subsection (3) does not apply to a workplace:
(a) where materials are kept on site for less than 5 days, where the employer ensures that an alternate and effective means of notification of the fire department, appropriate to the hazard, is in place in the event of a fire or other emergency; or
(b) which is not within the service area of a fire department.
[S.N.L. 2019, c. 8, s. 20]
Section 444 Fire and explosion
444. (1) Where a worker is employed in or about a bilge, tank, compartment or cargo space of marine equipment or in an area where there is a possibility of the presence of a volatile or flammable substance, gas or vapour, an employer shall institute a system of inspections and tests to determine the presence of that substance, gas or vapour before work is commenced.
(2) Where a volatile or flammable substance, gas or vapour is present or arises from the work process, the hazard shall be removed or controlled by ventilation or other effective means.
(3) Where work or manufacturing processes involve the use of a flammable liquid, vapour or gas, the concentration of the liquid, vapour or gas in the work area shall be maintained below the lower explosive limit (LEL) of the substance involved.
(4) A container used to carry, transfer, or store a flammable solvent shall meet the requirements of the CSA Standards and shall be electrically grounded or bonded while the contents are transferred from one container to another.
(5) Waste material contaminated with a solvent, oil, grease, paint or other flammable substance shall be placed in covered metal containers before disposal and shall not be stored in work areas.
(6) Where a volatile or flammable substance, gas or vapour is present, or arises out of material or equipment or from a work process, existing or potential sources of ignition shall be controlled or eliminated.
(7) For the purpose of subsection (6), a source of ignition includes an open flame, spark-producing mechanical equipment, welding and cutting processes, smoking, static discharge, electrical equipment or an installation that is not approved for hazardous locations, as specified by the Canadian Electrical Code.
(8) Where work involves more than one employer, a principal contractor shall ensure that sources of ignition resulting from the work of one employer are eliminated or adequately controlled where a flammable gas or a flammable liquid is handled, used or stored by another employer.
Section 446 Combustible substances
446. (1) Where a work process releases finely-divided combustible dust within an enclosed area where workers are employed, effective dust control equipment shall be used.
(2) A collector of combustible dusts, other than that of the liquid spray type, shall be
(a) located outside or in isolated enclosures removed from or protected against sources of ignition; and
(b) provided with explosion relief vents.
(3) Electrical wiring and equipment in a combustible dust collector and associated rooms or enclosures shall be of the explosion-proof type.
(4) Where combustible dust collects in a building, structure, machinery or equipment, it shall be removed before the accumulation of the dust creates a fire or explosion hazard.
Part XXI WELDING, BURNING AND CUTTING OPERATIONS
Section 449 Gas welding and burning
449. (1) Welding, cutting, and similar processes shall be carried out according to the requirements of
(a) CSA Standard W117.2 in "Safety in Welding, Cutting and Allied Processes" or another standard acceptable to the minister ;
(b) the manufacturer's instructions and recommendations for the equipment being used; and
(c) the applicable requirements of these regulations.
(2) Cylinders, piping and fittings of compressed and liquefied-gas systems shall be located or protected in a manner that prevents physical damage to them.
(3) A worker shall prevent a spark or flame from coming into contact with a cylinder, regulator or hose of a compressed-gas system and charged gas cylinders shall be protected from a source of heat in excess of 54.44Celsius.
(4) Before gas-welding or burning equipment is put into use, a worker shall ensure that parts are free from defects, leaks or oil and grease and only standard fittings, designed and manufactured for the specific compressed gas service shall be used.
(5) A regulator or an automatic reducing valve of welding equipment shall only be used for the gas for which it was designed.
Section 450 Compressed gas cylinders
450. (1) A compressed gas cylinder
(a) shall be
(i) secured during storage, transportation or use, and
(ii) stored, transported and used only in accordance with the manufacturer's instructions, applicable CSA and NFPA standards and applicable legislation; and
(b) shall not be hoisted by slings, dropped or subjected to impact.
(2) A cylinder valve shall be closed and a hose drained when work is finished or when a cylinder is empty, and a valve protection cover shall be kept in position when a cylinder is not connected for use.
Section 451 Oxygen
451. A worker shall not
(a) permit oil or grease to contact an oxygen cylinder, valve, regulator or other fitting; or
(b) handle an oxygen cylinder or apparatus with oily or greasy hands or gloves.
Section 452 Radiation protection
452. (1) Arc welding shall not be carried out unless a worker who may be exposed to radiation from the arc flash is protected by an adequate screen, curtain or partition or wears suitable eye protection.
(2) A screen, curtain or partition near an arc welding operation shall be made of or treated with a flame-resistant material or coating, and have a nonreflective surface finish.
Section 453 Burning and welding
453. (1) Burning, welding or other hot work shall not be done in an area where there is a likelihood of the presence of flammable substances until
(a) tests have been done to ensure that work may be safely performed; and
(b) suitable procedures have been adopted to ensure that all existing or potential sources of ignition have been eliminated or effectively controlled.
(2) Where testing procedures are used, tests shall be conducted at intervals to ensure the continuing safety of workers.
(3) Burning, welding or cutting shall not be done where there is a danger of extreme heat coming into contact with a concrete surface unless that surface is protected from the source of heat.
(4) Suitable safety devices to prevent reverse gas flow and to arrest a flashback shall be installed according to the manufacturer's instructions on each hose in an oxygen system between the torch and the regulator.
Section 454 Ventilation
454. Effective local exhaust ventilation shall be used at a fixed work station to minimize worker exposure to harmful air contaminants produced by welding, burning or soldering.
Section 455 Coatings on metals
455. A coating on metal which could emit harmful contaminants, including lead, chromium, organic materials, or toxic combustion products shall be removed from the base metal, whenever practicable, before welding or cutting.
Section 456 Receptacles for stubs
456. Receptacles for electrode stubs shall be provided and used.
Section 457 Respiratory protection
457. Respiratory protective equipment shall be provided and worn where an effective means of natural, mechanical or local exhaust ventilation is not practicable.
Part XXVII CONFINED SPACE ENTRY
Section 511 Confined space entry
511. (1) An employer shall perform an assessment of the work area to determine whether it contains a confined space.
(2) For the purpose of this Part, "confined space" means an enclosed or partially enclosed space that
(a) is not designed or intended for human occupancy except for the purpose of performing work;
(b) has restricted means of access and egress; and
(c) may become hazardous to a person entering it as a result of
(i) its design, construction, location or atmosphere,
(ii) the materials or substances in it, or
(iii) any other conditions relating to it.
(3) A worker shall not work in a confined space after January 1, 2013 unless the worker has completed a confined space entry program prescribed by the commission.
(4) An employer shall inform a worker who may have to work in a confined space of a hazard by posting signs or other equally effective means of advising of the existence of and dangers posed by confined spaces.
[N.L.R. 43/22, s. 42]
Section 512 Corrective precautions
512. (1) Upon first entering a confined space, a worker shall assume the space is hazardous until the contrary is demonstrated.
(2) An employer shall ensure that a worker does not enter a confined space until
(a) an adequate assessment of the hazards related to the confined space has been carried out;
(b) a source containing a hazardous substance leading to the confined space is safely and completely blocked off or disconnected;
(c) a test required under subsection (11) has been completed;
(d) the worker is qualified to safely enter and perform duties within the confined space;
(e) a written work permit documenting the tests and safety precautions has been completed; and
(f) a set of written safe work procedures has been developed and a worker has been instructed in these procedures.
(3) The assessment referred to in paragraph (2)(a) shall be recorded in writing and shall consider, with respect to each confined space,
(a) the hazards that may exist due to the design, construction, location, use or contents of the confined space; and
(b) the hazards that may develop while work is done inside the confined space.
(4) The record of the assessment may be incorporated into an entry permit.
(5) Where 2 or more confined spaces are of similar construction and present the same hazards, their assessments may be recorded in a single document, but each confined space shall be clearly identified in the assessment.
(6) The employer shall appoint a person with adequate knowledge, training and experience to carry out the assessment and shall maintain a record containing details of the person's knowledge, training and experience.
(7) The assessment shall contain the name of the person who carries out the assessment.
(8) The person shall sign and date the assessment and provide it to the employer.
(9) On request, the employer shall provide copies of the assessment and of the record to
(a) the joint health and safety committee or the health and safety representative; or
(b) every worker who performs work to which the assessment relates, where the workplace has no joint health and safety committee or health and safety representative.
(10) The employer shall ensure that the assessment is reviewed as often as necessary to ensure that the assessment referred to in paragraph (2)(a) remains current.
(11) Appropriate tests for harmful vapours, gasses, fumes, mists, dusts or explosive substances and oxygen deficiency shall be made and recorded
(a) before entry into the confined space;
(b) after an interruption in the work procedures; and
(c) at appropriate intervals.
(12) Where a test made under subsection (11) indicates an unsafe condition, the confined space shall be ventilated or cleaned or both and periodically retested to ensure that:
(a) the oxygen content is between 20% and 22%;
(b) the concentration of flammable substances is maintained below 10% of the lower explosive limit (LEL) of that substance or substances; and
(c) a worker's exposure to harmful substances is maintained at acceptable levels in accordance the TLVs established by ACGIH.
(13) Where a test under subsection (11) indicates the presence of a harmful or explosive substance and it is not feasible to provide a safe respirable atmosphere, an employer shall ensure that
(a) a worker entering the confined space is provided with and wears respiratory and personal protective equipment appropriate to the hazards likely to be encountered; and
(b) where a flammable or explosive gas or liquid is present all sources of ignition are controlled or eliminated.
(14) Where control measures referred to in subsection (13) cannot be implemented, a worker shall leave the confined space.
(15) Tests made under in subsection (11) shall be performed by a person who has been adequately trained in the proper use of testing and monitoring equipment.
(16) Equipment used in testing and monitoring shall be calibrated and monitored according to the manufacturer's instructions.
(17) The completed permit referred to in paragraph (2)(e) shall be made available at the time of entry to all authorized personnel by posting it at the entry portal or by another effective means.
Section 513 Work procedures
513. (1) An employer shall ensure that a worker who is required or permitted to enter a confined space in which a harmful atmosphere exists or may develop or where the worker may become entrapped by material
(a) wears appropriate retrieval equipment which would keep the worker in a position to be rescued; and
(b) has a life-line attached to the retrieval equipment which is tended at all times by a person, stationed outside the entrance to the confined space who shall be equipped for and capable of effecting rescue
and the employer shall prevent entanglement of life-lines and other equipment where one or more workers enter the confined space.
(2) Notwithstanding subsection (1), the use of a lifeline is not required where an obstruction or other condition makes its use impractical or unsafe but, in that case, an employer shall implement procedures to ensure the safety of the worker.
(3) Where a worker is required to enter a confined space the employer shall ensure that an attendant
(a) is assigned to the worker;
(b) is stationed outside and near
(i) the entrance to the confined space, or
(ii) where there is more than one entrance to the confined space, the one that best allows the attendant to perform the attendant's duties under subsection (4);
(c) is in continuous communication with the worker using the means of communication described in the relevant safe work procedure; and
(d) is provided with a device for summoning an adequate rescue response.
(4) An attendant shall not enter a confined space and shall, in accordance with the required safe work procedure,
(a) monitor the safety of the worker in the confined space;
(b) provide assistance to the worker; and
(c) summon an adequate rescue response where one is required.
[N.L.R. 43/22, s. 43]
Section 514 Entry into confined space
514. A confined space shall be entered only where
(a) the opening for entry and exit is sufficient to allow safe passage of a person wearing personal protective equipment;
(b) mechanical equipment in the confined space is
(i) disconnected from its power source, and
(ii) locked out and tagged;
(c) pipes and other supply lines whose contents are likely to create a hazard are blanked off;
(d) measures have been taken to ensure that, where appropriate, the confined space is continuously ventilated;
(e) liquid in which a person may drown or a free-flowing solid in which a person may become entrapped has been removed from the confined space;
(f) adequate explosion-proof illumination is provided where appropriate; and
(g) adequate barriers are erected to prohibit unauthorized entry.
Section 515 Explosives or flammable atmosphere
515. An employer shall ensure that a worker does not enter or remain in a confined space that contains or is likely to contain an explosive or flammable gas or vapour, unless
(a) the worker is performing only inspection, work that does not produce a source of ignition and, in the case of an explosive or flammable gas or vapour, the atmospheric concentration is less than 25% of its lower explosive limit, as determined by a combustible gas measuring instrument;
(b) the worker is performing only cold work and, in the case of an explosive or flammable gas or vapour, the atmospheric concentration is less than 10% of its lower explosive limit as determined by combustible gas instruments; or
(c) the worker is performing hot work and all of the following conditions are satisfied:
(i) in the case of an explosive or flammable gas or vapour, the atmospheric concentration is less than 5% of its lower explosive limit, as determined by a combustible gas instrument,
(ii) the atmosphere in the confined space does not contain, and is not likely to contain while a worker is inside, an oxygen content greater than 23%,
(iii) the atmosphere in the confined space is monitored continuously,
(iv) the entry permit includes adequate provisions for hot work and corresponding control measures, and
(v) an adequate alarm system and exit procedures are provided to ensure that workers have adequate warning and are able to exit the confined space safely where either or both of the following occur, in the case of an explosive or flammable gas or vapour
(A) the atmospheric concentration exceeds 5% of its lower explosive limit, or
(B) the oxygen content of the atmosphere exceeds 23% by volume.
Section 516 Rescue from confined space
516. An employer shall ensure that emergency rescue procedures are established and followed where workers are trained in the event of an accident or other emergency in or near the confined space, including immediate evacuation of the confined space.
Workplace Hazardous Materials Information System (WHMIS)
Regulations, 2018
C.N.L.R. 34/18
Section 2 Definitions
2. In these regulations
(a) "bulk shipment" means a shipment of a hazardous product that is contained, without intermediate containment or intermediate packaging, in
(i) a vessel that has a water capacity equal to or greater than 450 litres,
(ii) a freight container, a road vehicle, a railway vehicle or a portable tank,
(iii) the hold of a ship, or
(iv) a pipeline;
(b) "CAS registry number" means the identification number assigned to a chemical by the Chemical Abstracts Service, a division of the American Chemical Society;
(c) "category" includes a subcategory;
(d) "container" includes a bag, barrel, bottle, box, can, cylinder, drum, storage tank or similar package or receptacle;
(e) "education" means the delivery of general information to workers including information applicable to more than one workplace or job;
(f) "fugitive emission" means a gas, liquid, solid, vapour, fume, mist, fog or dust that escapes from process equipment or from emission control equipment or from a product to which workers may be readily exposed;
(g) "hazard information" means information on the proper and safe use, storage and handling of a hazardous product and includes information relating to its health and physical hazards;
(h) "hazardous product" means a product, material, mixture or substance classified by the regulations made under subsection 15(1) of the Hazardous Products Act (Canada) in a category of a hazard class listed in Schedule 2 of that Act;
(i) " Hazardous Products Regulations " means the Hazardous Products Regulations under the Hazardous Products Act (Canada) ;
(j) "hazardous waste" means a hazardous product in the workplace that is acquired or generated for recycling or recovery or is intended for disposal;
(k) "health professional" means
(i) a physician who is registered and entitled under the laws of a province to practise medicine and who is practising medicine under those laws in that province, and
(ii) a nurse who is registered or licensed and entitled under the laws of a province to practise nursing and who is practising nursing under those laws in that province;
(l) "label" means written, printed or graphic information elements relating to a hazardous product which are designed to be affixed to, printed on or attached to the hazardous product or the container in which the hazardous product is packaged;
(m) "laboratory sample" means a sample of a hazardous product packaged in a container that contains less than 10 kilograms of the hazardous product and is intended solely to be tested in a laboratory but does not include a sample that is to be used
(i) by the laboratory for testing other products, materials, mixtures or substances, or
(ii) for education or demonstration purposes;
(n) "manufactured article" means an article that
(i) is formed to a specific shape or design during manufacture, the intended use of which when in that form is dependent in whole or in part on its shape or design, and
(ii) when being installed, if the intended use of the article requires it to be installed, and under normal conditions of use, will not release or otherwise cause a person to be exposed to a hazardous product;
(o) "proceedings" has the same meaning as in subsection 19(3) of the Hazardous Materials Information Review Act (Canada) ;
(p) "product identifier" means, in respect of a hazardous product, the brand name, chemical name, common name, generic name or trade name;
(q) "readily available" means
(i) present in an appropriate place that is known to the workers,
(ii) accessible to workers at all times, and
(iii) in the form of either a physical copy that can be handled or an electronic copy that is easily available in hard copy to workers likely to be exposed to a hazardous product;
(r) "research and development" means a systematic investigation or search carried out in a field of science or technology by means of experiment or analysis, other than the disclosure of source of toxicological data under section 25;
(s) "safety data sheet" means a document that contains the headings required under the regulations made under subsection 15(1) of the Hazardous Products Act (Canada) and information about a hazardous product, including information related to the hazards associated with the use, storage or handling of the hazardous product in the workplace;
(t) "significant new data" means new data regarding the hazard presented by a hazardous product that changes its classification in a category of a hazard class or results in its classification in another hazard class, or changes the ways to protect against the hazard presented by the hazardous product;
(u) "supplier label" means a label provided by a supplier that contains information elements as required by the Hazardous Products Act (Canada)
(v) "supplier safety data sheet" means a safety data sheet provided by a supplier that contains information elements as required by the Hazardous Products Act (Canada) ;
(w) "training" refers to the delivery of workplace and job specific information to workers; and
(x) "workplace label" means a label which discloses
(i) a product identifier which is identical to that found on the safety data sheet of the corresponding hazardous product,
(ii) information for the safe handling (ii) information for the safe handling of the hazardous product which is conveyed in a manner appropriate to the workplace, and
(iii) that a safety data sheet for the hazardous product, where one has been obtained from a supplier or prepared by the employer, is available.
Section 4 Prohibition
4. (1) An employer shall ensure that a hazardous product is not used, stored or handled in a workplace unless all of the applicable requirements of these regulations in respect of labels, identifiers, safety data sheets and worker education and training are complied with.
(2) Notwithstanding subsection (1), an employer may store a hazardous product in a workplace while actively seeking information required by these regulations.
Section 5 Worker education and training
5. (1) An employer shall ensure that a worker who works with a hazardous product or may be exposed to a hazardous product in the course of his or her work activities is informed about all hazard information received from a supplier concerning that hazardous product as well as any further hazard information of which the employer is aware or ought to be aware concerning the use, storage, handling and disposal of that hazardous product.
(2) Where a hazardous product is produced in a workplace, an employer shall ensure that a worker who works with that hazardous product or may be exposed to that hazardous product in the course of his or her work activities is informed about all hazard information of which the employer is aware or ought to be aware concerning that hazardous product and its use, storage, handling and disposal.
Section 6 Instructions to workers
6. (1) The employer shall ensure that a worker who may be exposed to a hazardous product in the course of his or her work activities is
(a) educated in the content required on a supplier label and workplace label, and the purpose and significance of the information disclosed on it;
(b) educated in the content required on a safety data sheet, and the purpose and significance of the information contained on the safety data sheet;
(c) trained in procedures for the safe use, storage, handling and disposal of a hazardous product;
(d) trained in procedures for the safe use, storage, handling and disposal of a hazardous product contained or transferred in
(i) a pipe,
(ii) a piping system including valves,
(iii) a process vessel,
(iv) a reaction vessel, or
(v) a tank car, tank truck, ore car, conveyor belt or similar conveyance;
(e) trained in procedures to be followed where a fugitive emission is present; and
(f) trained in procedures to be followed in case of an emergency involving a hazardous product.
(2) An employer shall ensure that the program of worker education and training required by subsection (1) is developed and implemented
(a) for that employer's workplace and related to the workplace's hazard prevention and control program; and
(b) in consultation with the occupational health and safety committee or the worker health and safety representative.
(3) An employer shall ensure, so far as is reasonably practicable, that
(a) the program of worker education and training required by subsection (1) results in a worker being able to apply the information as needed to protect the worker's health and safety; and
(b) the knowledge of workers is periodically evaluated using written tests, practical demonstrations or other suitable means.
(4) The employer shall review at least annually, or more frequently where required by a change in work conditions or available hazard information, and in consultation with the occupational health and safety committee or the worker health and safety representative, the education and training programs that have been developed and implemented to provide to workers the knowledge required to safely use, store, handle and dispose of hazardous products.
Section 7 Supplier label
7. (1) An employer shall ensure that a hazardous product or the container in which a hazardous product is packaged that is received at a workplace has a label affixed to it, printed on it or attached to it in accordance with the Hazardous Products Regulations .
(2) Where a hazardous product is in the workplace in the container in which it was received from the supplier, an employer shall not remove, deface, modify or alter the supplier label.
(3) The exemptions from the labelling requirements under the Hazardous Products Regulations and section 18, where applicable, shall prevail over subsections (1) and (2).
(4) The employer shall update the labels or the information on the container in which a hazardous product is packaged as soon as significant new data is provided to the employer from the supplier.
(5) Where a label affixed to, printed on or attached to a hazardous product or a container of a hazardous product becomes illegible or is accidentally removed from the hazardous product or the container, the employer shall replace the label with either a supplier label or a workplace label.
(6) Notwithstanding subsection (2), an employer may remove a supplier label under normal conditions of use of the hazardous product where it is in a container that has a capacity of 3 millilitres or less and the label interferes with the normal use of the product.
(7) Where a hazardous product is imported or received under the Hazardous Products Regulations at a workplace and that hazardous product does not have a supplier label, the employer shall affix to, print on or attach to it a workplace label that complies with the requirements of the Hazardous Products Regulations .
(8) An employer who has received an unpackaged hazardous product or a hazardous product transported as a bulk shipment to or on which, under the exemption in subsection 5.5(2) of the Hazardous Products Regulations , a supplier label has not been affixed, printed or attached, shall affix, print or attach a label having the information required of a supplier label to or on the container of the hazardous product or to or on the hazardous product in the workplace.
Section 8 Employer-produced products
8. (1) Where an employer produces a hazardous product in a workplace, the employer shall ensure that the hazardous product or the container of the hazardous product has applied to it a workplace label.
(2) The employer shall update the workplace labels as soon as significant new data is available to the employer.
(3) Subsection (1) does not apply when the hazardous product is in a container that is intended to contain the hazardous product for sale or disposition and the container is or is about to be appropriately labelled.
(4) For the purpose of subsection (1), the word "produces" does not include the production of a fugitive emission.
Section 9 Decanted products
9. (1) Where a hazardous product in a workplace is in a container other than the container in which it was received from a supplier, the employer shall ensure that the container has applied to it a workplace label.
(2) Subsection (1) does not apply to a portable container that is filled directly from a container that has applied to it a supplier label or workplace label where
(a) the hazardous product
(i) is under the control of and is used exclusively by the worker who filled the portable container,
(ii) is used only during the shift in which the portable container was filled, and
(iii) the content of the container is clearly identified; or
(b) all of the hazardous product is required for immediate use.
Section 10 Hazardous product in piping systems and vessels
10. Where a hazardous product in a workplace is contained or transferred in
(a) a pipe;
(b) a piping system including valves;
(c) a process vessel;
(d) a reaction vessel; or
(e) a tank car, tank truck, ore car, conveyor belt or similar conveyance,
the employer shall ensure the safe use, storage, handling and disposal of the hazardous product through worker training and the use of colour coding, labels, placards or a mode of identification.
Section 12 Laboratory labels
12. (1) Where subsection 5(5) or (6) of the Hazardous Products Regulations applies to a laboratory sample of a hazardous product, a label provided by the supplier and affixed to, printed on or attached to the container of the product received at the workplace that discloses the following information in place of the information required under paragraph 3(1)(c) or 3(1)(d) of the Hazardous Products Regulations complies with the requirements of section 7 of these regulations:
(a) the chemical name or generic chemical name of a material or substance in the hazardous product that, individually, is classified, under the Hazardous Products Act (Canada) and the Hazardous Products Regulations , in any category of a health hazard class and is present above the relevant concentration limit, or is present at a concentration that results in the mixture being classified in a category of a health hazard class, where known by the supplier; and
(b) the statement "Hazardous Laboratory Sample. For hazard information or in an emergency call / Èchantillon pour laboratoire de produit dangereux. Pour obtenir des renseignements sur les dangers ou en cas d'urgence, composez" followed by an emergency telephone number which will allow a person to obtain the information that is required to be disclosed on the safety data sheet of the hazardous product.
(2) Where a hazardous product is in a container other than the container in which it was received from a supplier or is produced in the workplace or in a laboratory, the employer is exempt from the requirement of sections 8 and 9 if
(a) the hazardous product is
(i) a laboratory sample,
(ii) intended by the employer solely for use, analysis, testing, research and development, or evaluation in a laboratory,
(iii) not removed from the laboratory, and
(iv) clearly identified by a mode of identification visible to workers at the workplace; and
(b) workers are educated and trained in respect of the safe use, storage, handling and disposal of the hazardous product and the mode of identification.
(3) The employer shall ensure that the mode of identification and worker education and training used under subparagraph (2)(a)(iv) and paragraph (2)(b) enable the workers to readily identify and obtain one or more of the following:
(a) the information required on a safety data sheet;
(b) a label or document disclosing the information referred to in paragraphs (1)(a) and (b) with respect to the hazardous product or laboratory sample; or
(c) other information necessary to ensure the safe use, storage, handling and disposal of the hazardous product or laboratory sample.
Section 13 Supplier safety data sheets
13. (1) An employer who acquires a hazardous product for use, storage or handling at a workplace shall obtain a supplier safety data sheet in respect of that hazardous product that complies with the requirements of the Hazardous Products Regulations .
(2) Where a supplier safety data sheet obtained for a hazardous product in the workplace under subsection (1) is 3 or more years old, the employer shall, where possible, obtain from the supplier an up-to-date supplier safety data sheet in respect of that hazardous product.
(3) Subsection (2) shall not apply where
(a) the supplier advises the employer that the new safety data sheet no longer applies to the original product; or
(b) the employer has obtained written confirmation from the supplier that the safety data sheet has not changed.
(4) Where the employer is unable to obtain a safety data sheet as required under subsection (2), the employer shall add significant new data applicable to that hazardous product that he or she is aware of or ought to be aware of to the existing supplier safety data sheet.
(5) Notwithstanding subsection (1), the employer may provide at a workplace a safety data sheet in a format different from the supplier safety data sheet where the safety data sheet
(a) complies with section 18 or discloses less information than is required on the supplier safety data sheet where it is approved by the occupational health and safety committee or the worker health and safety representative; and
(b) the supplier safety data sheet is available at the workplace and the safety data sheet provided indicates that it is available.
(6) Where a supplier is exempted under the Hazardous Products Regulations from the requirement to provide a safety data sheet for a hazardous product, the employer is exempt from the requirement to obtain and provide a safety data sheet for that hazardous product.
(7) Where a hazardous product is received at a laboratory and the supplier has provided a safety data sheet, the employer shall ensure that a copy of the safety data sheet is readily available to the workers in that laboratory.
(8) Where a hazardous product is received or produced at a laboratory and the employer has prepared a safety data sheet, the employer shall ensure that the safety data sheet is readily available to workers in the laboratory.
Section 14 Employer safety data sheets
14. (1) Where the employer produces a hazardous product in the workplace, the employer shall prepare a safety data sheet in respect of that product which discloses, subject to section 18 of these regulations and Part 5 of the Hazardous Products Regulations , the information required under the Hazardous Products Regulations .
(2) An employer shall update the safety data sheet referred to in subsection (1) as soon as practical but not later than 90 days after significant new data becomes available to the employer.
(3) For the purpose of subsection (1), "produces" does not include the production of a fugitive emission or intermediate products undergoing reaction within a reaction or process vessel.
Section 15 Availability of safety data sheets
15. An employer shall ensure that
(a) a copy of a safety data sheet required by section 13 or 14 is made readily available at a workplace to workers who may be exposed to the hazardous product;
(b) a copy of a safety data sheet required by section 13 or 14 is made readily available to the occupational health and safety committee or to the worker health and safety representative; and
(c) the occupational health and safety committee or the worker health and safety representative is consulted on how to best achieve accessibility of safety data sheets in the workplace.
Section 16 Notice of significant new data
16. The employer shall notify the workers and the occupational health and safety committee or the worker health and safety representative of significant new data regarding a hazardous product as soon as possible after the supplier advises the employer or the employer becomes aware of the significant new data.
Section 17 Deletions from a safety data sheet
17. Where an employer claims an exemption from a requirement to disclose information under section 18, the employer may delete from the safety data sheet prepared in accordance with sections 13 and 14, for the time period prescribed by subsection 18(4), the information that is the subject of the claim but shall not delete hazard information.
Section 18 Confidential business information
18. (1) An employer who is required under these regulations to disclose any of the following information on a label or a safety data sheet may, where the employer considers it to be confidential business information, claim an exemption from the requirement to disclose that information:
(a) in the case of a material or substance that is a hazardous product,
(i) the chemical name of the material or substance,
(ii) the CAS registry number, or any other unique identifier, of the material or substance, and
(iii) the chemical name of an impurity, stabilizing solvent or stabilizing additive that is present in the material or substance that is classified in a category of a health hazard class under the Hazardous Products Act (Canada) and that contributes to the classification of the material or substance in the health hazard class under that Act;
(b) in the case of an ingredient that is in a mixture that is a hazardous product,
(i) the chemical name of the ingredient,
(ii) the CAS registry number, or any other unique identifier, of the ingredient, and
(iii) the concentration or concentration range of the ingredient;
(c) in the case of a material, substance or mixture that is a hazardous product, the name of any toxicological study that identifies the material or substance or any ingredient in the mixture;
(d) the product identifier of a hazardous product;
(e) information about a hazardous product, other than the product identifier, that constitutes a means of identification; and
(f) information that could be used to identify a supplier of a hazardous product.
(2) A claim under subsection (1) shall be made under the Hazardous Materials Information Review Act (Canada) and shall be filed in accordance with the procedure established under that Act and the regulations made under it.
(3) Under section 47 of the Hazardous Materials Information Review Act (Canada) , the federal Minister of Health shall exercise the powers and perform the functions specified in that Act and the procedures prescribed by regulations under that Act in respect of the claim made under subsection (1).
(4) Information that an employer considers to be confidential business information is exempt from disclosure from the time a claim is filed under subsection (1) until the final disposition of the proceedings in relation to the claim and for a period of 3 years after that if the claim is found to be valid.
(5) An employer who makes a claim under subsection (1) shall abide by decisions and orders issued under the Hazardous Materials Information Review Act (Canada) .
(6) Appeals of decisions and orders made under the Hazardous Materials Information Review Act (Canada) lie exclusively with the procedures established under that Act.
Section 19 Hazardous Materials Information Review Act (Canada)
19. (1) An employer who, under section 18, files a claim for exemption from a requirement to disclose information in respect of a hazardous product on a safety data sheet or on a label shall disclose on the safety data sheet and, where applicable, on the label of the hazardous product or container in which the hazardous product is packaged
(a) a statement that a claim for an exemption from that requirement has been filed;
(b) the date that the claim for exemption was filed; and
(c) the registry number assigned to the claim under the Hazardous Materials Information Review Act (Canada) .
(2) The requirements under subsection (1) apply,
(a) in the case that an order was issued by a screening officer under subsection 16(1) or 17(1) of the Hazardous Materials Information Review Act (Canada) , until the end of the period that begins on the final disposition of the proceedings in relation to the claim for exemption and does not exceed the period specified in the order; or
(b) in any other case, until the end of the period not exceeding 30 days after the final disposition of the proceedings in relation to the claim for exemption.
Section 20 Notice of exemption
20. An employer who receives notice of a decision made under the Hazardous Materials Information Review Act (Canada) that all or part of his or her claim for exemption from a requirement to disclose information in respect of a hazardous product on a safety data sheet or a label is valid shall, during the period beginning no later than the end of the applicable period specified in subsection 19(2) and on compliance with any order issued under subsection 16(1) or 17(1) of the Hazardous Materials Information Review Act (Canada) , where applicable, and ending on the last day of the exemption period, in respect of the sale or importation of the hazardous product or container in which the hazardous product is packaged, disclose the following information:
(a) a statement that an exemption has been granted;
(b) the date of the decision granting the exemption; and
(c) the registry number assigned to the claim under the Hazardous Materials Information Review Act (Canada) .
Section 21 Compliance where claim filed
21. (1) Where an employer produces a hazardous product in the workplace and files a claim for exemption under paragraph 11(2)(a) or subparagraphs 11(2)(b)(i) or (ii) of the Hazardous Materials Information Review Act (Canada) and the employer prepares a safety data sheet in respect of that hazardous product that discloses the following in place of the information elements listed in paragraphs 3(1)(a), (b), (c) and (d) or 3(2)(a), (b) and (c) of Schedule 1 to the Hazardous Products Regulations , the employer is compliant with subsection 14(1) of these regulations:
(a) in the case of a hazardous product that is a material or substance, the generic chemical name of the material or substance; or
(b) in the case of a hazardous product that is a mixture, the generic chemical name of each material or substance in the mixture that, individually, is classified in any category of a health hazard class under the Hazardous Products Act (Canada) and is present above the relevant concentration limit or is present at a concentration that results in the mixture being classified in a category of any health hazard class under that Act.
(2) Where an employer produces a hazardous product in the workplace and files a claim for exemption under subparagraph 11(2)(b)(iii) of the Hazardous Materials Information Review Act (Canada) and the employer prepares a safety data sheet in respect of that hazardous product that does not disclose the information element listed in paragraph 3(2)(d) of Schedule 1 to the Hazardous Products Regulations , the employer is compliant with subsection 14(1) of these regulations.
(3) Where an employer produces a hazardous product in the workplace and files a claim for exemption under paragraph 11(2)(d) of the Hazardous Materials Information Review Act (Canada) and the employer prepares a safety data sheet in respect of that hazardous product that discloses, in place of the product identifier, a code name or code number for the product, the employer is compliant with subsection 14(1) of these regulations.
Section 22 Confidentiality of information
22. (1) Where an official of the government of the province obtains information under paragraph 46(2)(e) of the Hazardous Materials Information Review Act (Canada) , the official to whom the information is communicated shall keep the information confidential and shall not disclose the information to a person except for the purposes of the administration or enforcement of the Occupational Health and Safety Act and regulations made under it.
(2) A person to whom information is disclosed under subsection (1) shall keep the information confidential.
Section 23 Disclosure of information in medical emergencies
23. (1) An employer shall, in respect of a hazardous product present or which was present in the workplace, provide information respecting the hazardous product, including confidential business information, in the possession of the employer to a health professional who requests information on the hazardous product for rendering medical treatment to a person in an emergency.
(2) Any information that, by virtue of an exemption under the Hazardous Materials Information Review Act (Canada) or these regulations, is not required to be disclosed on the safety data sheet but has nevertheless been provided by an employer to any health professional who requests that information for the purpose of making a medical diagnosis of, or rendering medical treatment to, a person in a medical emergency shall be kept confidential, except for the purpose for which it was provided, if the health professional has been informed by the employer that the information is to be kept confidential.
Section 24 Other disclosure prohibited
24. A person shall not use, disclose or release information protected as confidential business information under these regulations except as provided by sections 22 and 23.
Section 25 Disclosure of source of toxicological data
25. Subject to the Hazardous Materials Information Review Act (Canada) , an employer who manufactures a hazardous product in a workplace shall, at the request of
(a) an officer;
(b) a worker at the site;
(c) the occupational health and safety committee;
(d) a worker health and safety representative; or
(e) in the absence of an occupational health and safety committee or a worker health and safety representative, at the request of the representative of the workers at the site,
disclose as quickly as possible under the circumstances the source of toxicological data used in preparing the safety data sheet in the application of subsection 14(1).
Sections 26 - 28 omitted.
- Don’t Be Next (cancer)
- Don’t Be Next (soot)
- Don’t Be Next (statistics)
- Industrial Hygiene Service Providers Directory of Newfoundland and Labrador
- Occupational Disease
- Registry of the Former Workers of the Baie Verte Asbestos Mine: Final Report
- Safety Share - What is WHMIS 2015?
- Safety Share – Mercury Vapour and Lighting
- Safety Share – Silica
- Sharps
CCOHS


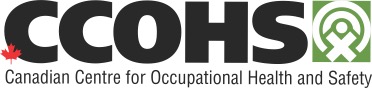