Confined Space Entry
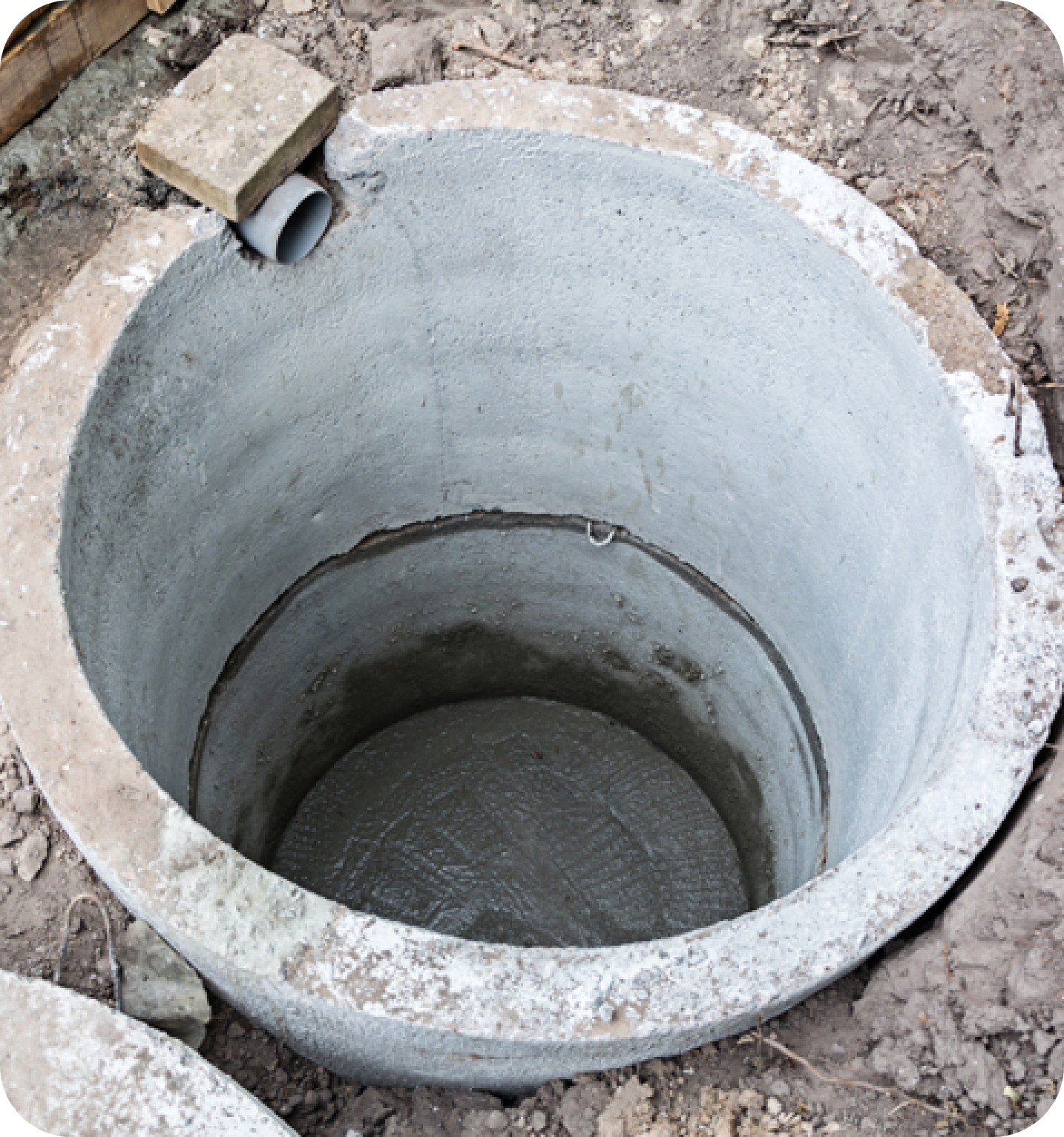
Highlighted words reveal definitions when selected.
Confined space incidents can happen suddenly, often without any warning that something is wrong. Employers must make sure workers remain safe when working in or around confined spaces. The necessary steps include identifying confined spaces, and assessment and control of hazards.
The effective use of atmospheric testing is very important. Statistics show that more than 50 per cent of confined space deaths are due to oxygen deficiency and in most of these cases no atmospheric testing was done. Lack of oxygen can impair judgement and cause workers to lose consciousness. These symptoms not only affect a worker’s ability to get out of the space, but also put rescuers at risk. According to the National Institute for Occupational Safety and Health (NIOSH), approximately 60 per cent of confined space fatalities are rescuers.
Although a confined space can have many hazards, the four main dangers are:
- Lack of oxygen;
- Fire and explosion;
- Exposure to toxins; and
- Drowning in liquids and entrapment in free-flowing solids.
Employer Responsibilities
Employers must:
- Assume a confined space is hazardous, until it is proven not to be. [OHS Regs., s. 512 (1)]
- Perform an assessment of the workplace to determine if a confined space is present. [OHS Regs., s. 511 (1)] Where a confined space is identified, inform workers by posting signs or another means that states the existence and dangers of the confined space. [OHS Regs., s. 511 (4)]
- Make sure that workers do not enter a confined space until: [OHS Regs., s. 512 (2)]
- An adequate risk assessment has been done which records (in writing) the hazards that may exist or develop while the work is being done;
- The source(s) of a hazardous substance has been safely and completely blocked off or disconnected;
- Appropriate atmospheric tests have been done;
- The written work permit is done that documents the tests and precautions;
- Written safe work procedures are developed;
- Workers have been instructed about the safe work procedures.
- Appoint a qualified person to carry out the assessment, and maintain records about this person’s knowledge, training and experience. [OHS Regs., s. 512 (6)]
- Make sure the assessment is reviewed as often as necessary to remain up to date. [OHS Regs., s. 512 (10)]
- Make sure workers do not enter a confined space unless they hold a current certification in confined space entry obtained from an approved training provider. [OHS Regs., s. 511 (3)] Confined space entry training expires after three years.
Assessment
The assessment of a confined space must:
- Be carried out by a person with adequate knowledge, training and experience. [OHS Regs., s. 512 (6)]
- Be signed and contain the name of the person who did the assessment. [OHS Regs., s. 512 (7) and (8)]
- Clearly identify the confined space; however, two or more confined spaces of similar construction and hazards may be recorded on a single document. [OHS Regs., s. 512 (5)]
- Be given to the employer when complete. [OHS Regs., s. 512 (8)]
- Be given to the OHS Committee, WHS Representative, or when there is no Committee or Representative, every worker who performs confined space work, upon request. [OHS Regs., s. 512 (9)]
- Make sure the completed permit is made available to all authorized personnel by posting it at the entry to the confined space, or by another effective method. [OHS Regs., s. 512 (17)]
Atmospheric tests
Appropriate tests (based on the hazard assessment) must be made and recorded (in writing) for toxic dusts, vapours and gases; flammable or explosive substances; and too little or too much oxygen: [OHS Regs., s. 512 (11)]
- Before entry into the confined space;
- After an interruption in the work; and
- At appropriate intervals.
Tests must be done by a qualified person who has been adequately trained. [OHS Regs., s. 512 (15)] The equipment used for testing must be calibrated and maintained according to the manufacturer’s instructions. [OHS Regs., s. 512 (16)]
When an unsafe atmosphere is identified, the confined space must be ventilated, cleaned, or both; and periodically retested to make sure that: [OHS Regs., s. 512 (12)]
- Oxygen content is between 20 and 22 per cent.
- The concentration of flammable or explosive substances is below the appropriate lower explosive limit (LEL) for the type of work being conducted:
- 25 per cent LEL for inspection;
- 10 per cent LEL for cold work; or
- 5 per cent LEL for hot work.
- Exposure to toxic substances is maintained below the occupational exposure limits set by the ACGIH (American Conference of Governmental Industrial Hygienists).
When a toxic, explosive, or flammable substance or atmosphere is present, and it is not possible to remove it through ventilation and cleaning, the employer must make sure that:
- Workers entering the space are provided with and wear respiratory and personal protective equipment that is appropriate for the hazards present. [OHS Regs., s. 512 (13)]
- The atmosphere is monitored continuously.[OHS Regs., s. 512 (13)]
- All sources of ignition are eliminated or controlled. [OHS Regs., s. 512 (14)]
Hot work must only be performed in a confined space when the following additional conditions are met: [OHS Regs., s. 512 (13)]
- The oxygen concentration does not exceed 23 per cent;
- Procedures for safely performing the hot work are included in the permit; and
- An adequate alarm system and exit procedures are in place to notify the worker of atmospheric concentration that exceeds 5 per cent LEL and 23 per cent oxygen.
Confined space entry
A confined space must only be entered when: [OHS Regs., s. 514]
- The opening allows a person wearing personal protective equipment (PPE) to enter and exit safely;
- All mechanical equipment is disconnected from its power source, and is locked out;
- Pipes and other supply lines are blanked off;
- The space is continuously ventilated, as appropriate;
- Any liquid or free-flowing solid in which a person may drown or become trapped has been removed;
- Adequate explosion-proof lighting is provided, as appropriate;
- Adequate barriers are set up to stop unauthorized entry;
- An attendant is stationed outside and near the entrance to the confined space, or the entrance that best allows them to perform their duties; and [OHS Regs., s. 513 (3)]
- The attendant is in continuous communication with the worker and is provided with a communication device capable of summoning adequate rescue. [OHS Regs., s. 513 (3)]
Work procedures
The employer must make sure the required safe work procedures are in place before entry into a confined space.
The entrant must have procedures before they enter a confined space where there is a harmful atmosphere or if they may become entrapped by material. [OHS Regs., s. 513 (1)] These procedures include:
- Appropriate retrieval equipment that will keep the entrant in a position to be rescued.
- A method for ensuring that a lifeline attached to the retrieval equipment does not get tangled with other lifelines or equipment, as well as, a person to attend the lifeline at all times who is capable of performing a rescue; or where a lifeline is impractical, some other suitable means of ensuring the safety of the worker.
The attendant must have procedures that allow them to monitor the safety of the worker, provide assistance, and summon adequate rescue, without entering the confined space themselves. [OHS Regs., s. 513 (4)]
Where a worker is attending a lifeline, they must only use retrieval equipment to which the lifeline is attached to effect the rescue of an entrant. This method is the only rescue they are permitted to perform. They must not enter the confined space to effect rescue.
In addition, an emergency rescue plan must be created, and workers must be trained in their role in the plan, including under which conditions they must immediately evacuate the confined space. [OHS Regs., s. 516]
Workers Responsibilities
Workers must:
- Take reasonable care to protect his or her health and safety and that of workers and persons at or near the workplace. [OHS Act, s. 6)]
- Properly wear or use personal protective equipment (PPE), safeguards and safety and devices provided for their protection in accordance with the manufacturer’s instructions and training provided by the employer. [OHS Act, s. 7(a)(a.1)] [OHS Regs., s. 17]
- Follow safe work practices and procedures.
- Immediately report concerns and hazards to the supervisor or employer. [OHS Regs., s. 17(3)]
- Not enter a confined space unless you hold a current certification in confined space entry, obtained from an approved training provider. [OHS Regs., s. 511 (3)] Confined space entry training expires after three years.
Related Topics
Confined space
An enclosed or partially enclosed space that:- Is not designed or intended for human occupancy except for the purpose of performing work;
- Has restricted means of access and egress; and
- May become hazardous to a person entering it as a result of:
- It's design, construction, location or atmosphere,
- The materials or substances in it, or
- Any other conditions relating to it. [OHS Regs., s. 511(2)]
Atmospheric testing
The measurement of oxygen and toxic substances in the air.The purpose is to determine if the air is safe for human occupancy, and if it is found to be unsafe, to determine the type of respiratory protection required.
Oxygen deficiency
An employer shall ensure that the respirable air in all underground workings is free from hazardous amounts of dusts, vapours and gases, and does not contain less than 20% oxygen.[OHS Regs., s. 413]And
where a test made under subsection (11) indicates an unsafe condition, the confined space shall be ventilated or cleaned or both and periodically retested to ensure that the oxygen content is between 20% and 22%. [OHS Regs., s. 512(12)]
National Institute for Occupational Safety and Health (NIOSH)
The National Institute for Occupational Safety and Health (NIOSH) is a research agency that is focused on the study of worker safety and health.Risk assessment
A risk assessment is a thorough check of the work environment and task before work begins.The purpose is to identify potential hazards and appropriate safety measures to be used to eliminate or reduce the hazards.
Permit
A permit or a permit to work is a formal written authority given to a worker or workers to carry out a planned work procedure. The purpose is to protect workers who are working in hazardous situations. For instance, a permit to work is required for entry into a confined space.Qualified person
A person who is knowledgeable of the work, the hazards involved and the means to control the hazards, by reason of education, training, experience or a combination of them. [OHS Regs., s.2(h) and (w)]Approved training provider
Some types of training, such as confined space entry, fall protection and power line hazards, must be delivered by WorkplaceNL approved training provider. A list of approved trainers and available courses can be found in the Certification Training Registry (CTR) https://ctr.bluedrop.io/#/Occupational Health and Safety Committee
Where 10 or more workers are employed at a workplace, the employer shall establish an occupational health and safety committee to monitor the health, safety and welfare of the workers employed at the workplace. [OHS Act, s. 37]A committee shall consist of 2 to 12 persons. Where the employer and workers cannot agree on the size of the committee, the minister may establish its size. [OHS Act, s. 38]
At least half of the members are to be persons representing the workers who are not connected with the management. The persons representing the workers are to be elected by other workers or appointed in accordance with the constitution of the union of which the workers are members.
The employer shall appoint sufficient employer representatives to ensure that the committee may function.
The employer and worker members of a committee shall elect a co-chairperson from their respective groups.
The employer shall post the names of the committee members in a prominent place at the workplace.
A committee:
- Shall seek to identify aspects of the workplace that may be unhealthy or unsafe;
- Shall participate in a workplace inspection that an employer is required by the regulations to conduct;
- May make recommendations to principal contractors, employers, workers, self-employed persons and the Assistant Deputy Minister or an Officer for the enforcement of standards to protect the health, safety and welfare of workers at the workplace;
- Shall receive complaints from workers as to their concerns about the health and safety of the workplace and their welfare;
- Shall establish and promote health and safety educational programs for workers;
- Shall maintain records as to the receipt and disposition of complaints received from workers;
- Shall co-operate with the Assistant Deputy Minister or an Officer who is exercising his or her duties under the act; and
- Shall perform those other duties and follow those procedures that may be prescribed by the regulations. [OHS Act, s. 39]
Worker Health and Safety Representative
Where less than 10 workers are employed at a workplace, the employer shall ensure that a worker not connected with the management of the workplace is designated as the worker health and safety representative to monitor the health, safety and welfare of workers employed at the workplace.[OHS Act, s. 41]
The worker health and safety representative is to be elected by other workers at the workplace or appointed in accordance with the constitution of the labour union of which the workers are members. [OHS Act, s. 42]
The employer shall post the name of the worker health and safety representative in a prominent place at the workplace. [OHS Act, s. 43]
A worker health and safety representative has the same duties as those imposed upon a committee where that is reasonably practicable. [OHS Act, s. 44]
A worker health and safety representative shall consult with his or her employer while performing his or her duties. [OHS Act, s. 44]
Ventilated
Ventilation is the movement of air in a closed space or system. It often involves the replacement of old or toxic air with fresh air taken from outside.Lower explosive limit (LEL)
Explosive gases and vapours only pose a risk to workers when the fuel to oxygen ratio is in the correct range. This is known as the explosive range.The upper and lower limits of this range are known as the upper explosive limit (UEL) and lower explosive limit (LEL), respectively.
When the fuel to oxygen ratio is below the LEL, there is not enough fuel to ignite the mixture. Likewise, when the fuel to oxygen ratio is above the UEL, there is not enough oxygen to ignite the mixture.
%LEL refers to the amount of fuel relative to the LEL.
Inspection
In the context of confined space entry, inspection means to visually examine the confined space without performing any tasks that have the potential to produce a source of ignition.Cold work
In the context of confined space entry, cold work means performing tasks that do not have the potential to produce a source of ignition.Hot work
means work which involves burning, welding, cutting, grinding, using fire or spark producing tools or other work that produces a source of ignition. [OHS Regs., s.2(m]ACGIH (American Conference of Governmental Industrial Hygienists)
The American Conference of Governmental Industrial Hygienists (ACGIH) is a scientific organization that develops occupational exposure limits for chemical and physical hazards. These limits can be found in their TLVs® and BEIs® book.In Newfoundland and Labrador, acceptable occupational exposure limits are established by the ACGIH.
Personal protective equipment
Any equipment or device which protects a worker's body from injury, illness or death. PPE acts as a barrier to protect the worker from the hazard.PPE should only be used:
- Where other controls are not available or adequate.
- As a short-term measure before controls are implemented.
- During activities such as maintenance, clean up, and repair where other controls are not feasible or effective.
- During emergency situations.
Lockout
"lockout" means the use of a lock to render machinery or equipment inoperable or to isolate an energy source in accordance with written procedure. [OHS Regs., s.127(e)]Retrieval equipment
Equipment that can be used to facilitate non-entry rescue of a worker. For example, in a confined space this may include full body harness, lifeline tripod, and winch.Emergency rescue plan
A set of written procedures to follow in case of an emergency.The procedures must include actions to be taken by the employer to reduce the impact of an emergency on people, equipment and the environment.
OCCUPATIONAL HEALTH AND SAFETY ACT
R.S.N.L. 1990, c. O-3
Section 6 Workers' general duty
6. A worker, while at work, shall take reasonable care to protect his or her own health and safety and that of workers and other persons at or near the workplace.
Section 7 Specific duties of workers
7. A worker
(a) shall co-operate with his or her employer and with other workers in the workplace to protect
(i) his or her own health and safety,
(ii) the health and safety of other workers engaged in the work of the employer,
(iii) the health and safety of other workers or persons not engaged in the work of the employer but present at or near the workplace;
(a.1) shall use devices and equipment provided for his or her protection in accordance with the instructions for use and training provided with respect to the devices and equipment;
(b) shall consult and co-operate with the occupational health and safety committee, the worker health and safety representative or the workplace health and safety designate at the workplace; and
(c) shall co-operate with a person exercising a duty imposed by this Act or regulations.
[S.N.L. 1999, c. 28, s. 3; 2001, c. 10, s. 26; 2004, c. 52, s. 2]
Section 37 Committees
37. Where 10 or more workers are employed at a workplace, the employer shall establish an occupational health and safety committee to monitor the health, safety and welfare of the workers employed at the workplace.
[S.N.L. 1999, c. 28, s. 9]
Section 38 Membership of committees
38. (1) A committee shall consist of the number of persons that may be agreed to by the employer and the workers but shall not be less than 2 nor more than 12 persons.
(2) At least half of the members of a committee are to be persons representing the workers at the workplace who are not connected with the management of the workplace.
(3) The persons representing the workers on the committee are to be elected by other workers at the workplace or appointed in accordance with the constitution of the union of which the workers are members.
(4) Where the employer and workers cannot agree on the size of the committee, the minister may establish its size.
(5) The employer shall appoint sufficient employer representatives to ensure that the committee may function.
(6) The employer and worker members of a committee shall elect a co- chairperson from their respective groups.
(7) The employer shall post the names of the committee members in a prominent place at the workplace.
Section 39 Duties of committees
39. A committee established under section 37
(a) shall seek to identify aspects of the workplace that may be unhealthy or unsafe;
(a.1) shall participate in a workplace inspection that an employer is required by the regulations to conduct;
(b) may make recommendations to principal contractors, employers, workers, self-employed persons and the assistant deputy minister or an officer for the enforcement of standards to protect the health, safety and welfare of workers at the workplace;
(c) shall receive complaints from workers as to their concerns about the health and safety of the workplace and their welfare;
(d) shall establish and promote health and safety educational programs for workers;
(e) shall maintain records as to the receipt and disposition of complaints received from workers under paragraph (c);
(f) shall co-operate with the assistant deputy minister or an officer who is exercising his or her duties under the Act; and
(g) shall perform those other duties and follow those procedures that may be prescribed by the regulations.
[S.N.L. 2001, c. 10, s. 29]
Section 40 Meetings of committee
40. Meetings of a committee shall take place during regular working hours at least once every 3 months and a worker is not to suffer loss of pay or other benefits while engaged in a meeting of a committee.
Section 41 Worker representative
41. (1) Where less than 10 workers are employed at a workplace, the employer shall ensure that a worker not connected with the management of the workplace is designated as the worker health and safety representative to monitor the health, safety and welfare of workers employed at the workplace.
(2) The employer shall provide and pay for training for the worker health and safety representative.
(3) The training provided under subsection (2) shall meet the requirements the Workplace Health Safety and Compensation Commission may set.
(4) The worker health and safety representative shall participate in the training provided under this section.
(5) An employer shall compensate a worker for participating in training under this section as if the training were regular work.
[S.N.L. 2001, c. 10, s. 30; 2004, c. 47, s. 27]
Section 42 Election of representative
42. The worker health and safety representative is to be elected by other workers at the workplace or appointed in accordance with the constitution of the labour union of which the workers are members.
Section 43 Posting name
43. The employer shall post the name of the worker health and safety representative or the workplace health and safety designate in a prominent place at the workplace.
[S.N.L. 2004, c. 52, s. 9]
Section 44 Duties of representative
44. (1) A worker health and safety representative or the workplace health and safety designate has the same duties as those imposed upon a committee under section 39, where that is reasonably practicable.
(2) A worker health and safety representative or the workplace health and safety designate, where the workplace health and safety designate is not the employer, shall consult with his or her employer while performing his or her duties under subsection (1).
(3) Where the workplace health and safety designate is the employer, he or she shall consult with the workers while performing his or her duties under subsection (1).
[S.N.L. 2004, c. 52, s. 10]
Occupational Health and Safety Regulations, 2012
N.L.R. 5/12
Part I GENERAL
Section 2 Interpretation
2. (1) In these regulations
(a) "accident" includes
(i) an event occasioned by a physical or natural cause, or
(ii) disablement arising out of and in the course of employment;
(b) "ACGIH" means the American Conference of Governmental Industrial Hygienists;
(c) "Act" means the Occupational Health and Safety Act ;
(d) "administrative controls" means the provision, use and scheduling of work activities and resources in the workplace, including planning, organizing, staffing and coordinating, for the purpose of controlling risk;
(e) "ASHRAE" means the American Society of Heating, Refrigeration and Air Conditioning Engineers;
(f) "authorized" means, in reference to a person, a qualified person designated by an employer to carry out specific functions;
(g) "commission" means the Workplace Health, Safety and Compensation Commission continued under the Workplace Health, Safety and Compensation Act, 2022 ;
(h) "competent" means a person who is
(i) qualified because of that person's knowledge, training and experience to do the assigned work in a manner that ensures the health and safety of every person in the workplace, and
(ii) knowledgeable about the provisions of the Act and these regulations that apply to the assigned work, and about potential or actual danger to health or safety associated with the assigned work;
(i) "construction" means building, erection, excavation, alteration, repair, renovation, dismantling, demolition, structural maintenance, painting, moving, land clearing, earth moving, grading, street and highway building, concreting, equipment installation and alteration and the structural installation of construction components and materials in any form or for any purpose, and work in connection with it;
(j) "CSA" means the Canadian Standards Association;
(k) "engineering controls" means the physical arrangement, design or alteration of workstations, equipment, materials, production facilities or other aspects of the physical work environment, for the purpose of controlling risk;
(l) "hazardous health occupation" means an occupation from which an occupational disease may arise;
(m) "hot work" means work which involves burning, welding, cutting, grinding, using fire or spark producing tools or other work that produces a source of ignition;
(n) "injury" means
(i) an injury as a result of a chance event occasioned by a physical or natural cause, (ii) an injury as a result of wilful and intentional act, not being the act of the worker, (iii) disablement, (iv) occupational disease, or (v) death as a result of an injury arising out of and in the course of employment and includes a recurrence of an injury and an aggravation of a pre-existing condition but does not include stress other than stress that is an acute reaction to a sudden and unexpected traumatic event;
(o) "ISO" means the International Organization for Standardization;
(p) "mine" means mine as defined in the Mining Act ;
(q) "occupation" means an employment, business, calling or pursuit but does not include an endeavour that is not included in one of the classes of occupations in the current National Occupational Classification List developed by the Department of Human Resources and Social Development Canada in collaboration with Statistics Canada;
(r) "occupational disease" means a disease prescribed by regulations under the Workplace Health, Safety and Compensation Act and another disease peculiar to or characteristic of a particular industrial process, trade or occupation;
(s) "occupational health service" means a service established in or near a workplace to maintain and promote the physical and mental well-being of workers and may include personnel, equipment, transportation, supplies and facilities;
(t) "plant" means buildings, equipment and facilities where a worker or self-employed person is engaged in an occupation;
(u) "professional engineer" means a person who holds a certificate of registration to engage in the practice of engineering under the Engineers and Geoscientists Act;
(v) "proof test" means a test applied to a product to determine material or manufacturing defects;
(w) "qualified" means being knowledgeable of the work, the hazards involved and the means to control the hazards, by reason of education, training, experience or a combination of them;
(x) "TLV" means the documentation of threshold limit values for chemical substances and physical agents in the work environment published annually or more frequently by the ACGIH; and
(y) "work platform" means an elevated or suspended temporary work base for workers.
(2) In these regulations, a reference to a code or guideline, unless otherwise stated, includes amendments to that code or guideline and a reference shall be presumed to be a reference to the most current code or guideline.
(3) Where there is a conflict between a standard established by these regulations or a code or standard adopted by these regulations, the more stringent standard applies.
[S.N.L. 2022, c. W-11.1, s. 168]
Part III GENERAL DUTIES
Section 17 General duties of workers
17. (1) A worker shall make proper use of all necessary safeguards, protective clothing, safety devices, lifting devices or aids, and appliances
(a) designated and provided for the worker’s protection by the employer; or
(b) required under these regulations to be used or worn by a worker.
(2) A worker shall follow the safe work procedure in which the worker has been instructed.
(3) A worker shall immediately report a hazardous work condition that may come to the worker’s attention to the employer or supervisor.
[N.L.R. 43/22, s. 4]
Part IX DE-ENERGIZATION AND LOCKOUT
Section 127 Definitions
127. In this Part
(a) "control system isolating device" means a device that physically prevents activation of a system used for controlling the operation of machinery or equipment;
(b) "energy isolating device" means a device that physically prevents the transmission or release of an energy source to machinery or equipment;
(c) "energy source" means an electrical, mechanical, hydraulic, pneumatic, chemical, thermal or other source of energy of potential harm to workers;
(d) "key securing system" means a system which physically prevents access to keys when locks or positive sealing devices are applied in a group lockout procedure;
(e) "lockout" means the use of a lock to render machinery or equipment inoperable or to isolate an energy source in accordance with written procedure;
(f) "maintenance" means work performed to keep machinery or equipment in a safe operating condition, including installation, repair, cleaning, lubrication and the clearing of obstructions;
(g) "normal production" means work that is routine, repetitive, and integral to the normal use of machinery or equipment for production; and
(h) "personal lock" means a lock provided by the employer for use by a worker to ensure personal lockout protection such that each lock, when applied, is operable only by a key in the worker's possession, and by a key under the control of the supervisor or manager in charge.
Part XVIII EXCAVATION, UNDERGROUND WORK AND ROCK CRUSHING
Section 413 Air quality
413. (1) An employer shall ensure that
(a) the respirable air in all underground workings is free from hazardous amounts of dusts, vapours and gases, and does not contain less than 20% oxygen; and
(b) appropriate tests for harmful vapour, gases, fumes, mists, dusts or explosive substances and oxygen deficiency are made and recorded
(i) before entry,
(ii) after an interruption in the work procedures, and
(iii) at appropriate intervals.
(2) An employer who employs workers at a mine or quarry where silica is mined or quarried, or where it is present, shall comply with the Silica Code of Practice.
(3) The tests required under paragraph (1)(b) shall be performed by a person who has appropriate training in the proper use of testing and monitoring equipment.
(4) A worker employed in surface rock-excavating workings shall be protected from harmful dust concentrations by
(a) the use of suppression;
(b) dust removal by mechanical means; or
(c) another acceptable engineering control.
(5) Where a worker is exposed to dusting resulting from loading, transporting or conveying rock at surface operations, the dust shall be reduced to non-harmful concentrations by the application of water or by other effective methods.
(6) An employer shall ensure that dust caused by drilling or handling rock at underground rock-excavating workings is effectively suppressed by a means acceptable to the division.
(7) A rock drill, that is, a machine or device for drilling a hole in rock for the purpose of blasting, usually powered by compressed air but in which electricity or steam may be used, shall be equipped with a water jet, spray or other device acceptable to the minister to effectively suppress drilling dust.
(8) Subsection (7) does not apply to hand-drilling procedures.
(9) A water spray shall be used in every development heading unless written permission has been received from the assistant deputy minister to work the heading without a water spray.
(10) Effective dust-control measures shall be employed during the handling and loading of broken rock.
(11) Mechanical ventilation shall be provided to produce a minimum air volume of 15.24 cubic metres a minute a square metre of working face in the work area.
Part XXVII CONFINED SPACE ENTRY
Section 511 Confined space entry
511. (1) An employer shall perform an assessment of the work area to determine whether it contains a confined space.
(2) For the purpose of this Part, "confined space" means an enclosed or partially enclosed space that
(a) is not designed or intended for human occupancy except for the purpose of performing work;
(b) has restricted means of access and egress; and
(c) may become hazardous to a person entering it as a result of
(i) its design, construction, location or atmosphere,
(ii) the materials or substances in it, or
(iii) any other conditions relating to it.
(3) A worker shall not work in a confined space after January 1, 2013 unless the worker has completed a confined space entry program prescribed by the commission.
(4) An employer shall inform a worker who may have to work in a confined space of a hazard by posting signs or other equally effective means of advising of the existence of and dangers posed by confined spaces.
[N.L.R. 43/22, s. 42]
Section 512 Corrective precautions
512. (1) Upon first entering a confined space, a worker shall assume the space is hazardous until the contrary is demonstrated.
(2) An employer shall ensure that a worker does not enter a confined space until
(a) an adequate assessment of the hazards related to the confined space has been carried out;
(b) a source containing a hazardous substance leading to the confined space is safely and completely blocked off or disconnected;
(c) a test required under subsection (11) has been completed;
(d) the worker is qualified to safely enter and perform duties within the confined space;
(e) a written work permit documenting the tests and safety precautions has been completed; and
(f) a set of written safe work procedures has been developed and a worker has been instructed in these procedures.
(3) The assessment referred to in paragraph (2)(a) shall be recorded in writing and shall consider, with respect to each confined space,
(a) the hazards that may exist due to the design, construction, location, use or contents of the confined space; and
(b) the hazards that may develop while work is done inside the confined space.
(4) The record of the assessment may be incorporated into an entry permit.
(5) Where 2 or more confined spaces are of similar construction and present the same hazards, their assessments may be recorded in a single document, but each confined space shall be clearly identified in the assessment.
(6) The employer shall appoint a person with adequate knowledge, training and experience to carry out the assessment and shall maintain a record containing details of the person's knowledge, training and experience.
(7) The assessment shall contain the name of the person who carries out the assessment.
(8) The person shall sign and date the assessment and provide it to the employer.
(9) On request, the employer shall provide copies of the assessment and of the record to
(a) the joint health and safety committee or the health and safety representative; or
(b) every worker who performs work to which the assessment relates, where the workplace has no joint health and safety committee or health and safety representative.
(10) The employer shall ensure that the assessment is reviewed as often as necessary to ensure that the assessment referred to in paragraph (2)(a) remains current.
(11) Appropriate tests for harmful vapours, gasses, fumes, mists, dusts or explosive substances and oxygen deficiency shall be made and recorded
(a) before entry into the confined space;
(b) after an interruption in the work procedures; and
(c) at appropriate intervals.
(12) Where a test made under subsection (11) indicates an unsafe condition, the confined space shall be ventilated or cleaned or both and periodically retested to ensure that:
(a) the oxygen content is between 20% and 22%;
(b) the concentration of flammable substances is maintained below 10% of the lower explosive limit (LEL) of that substance or substances; and
(c) a worker's exposure to harmful substances is maintained at acceptable levels in accordance the TLVs established by ACGIH.
(13) Where a test under subsection (11) indicates the presence of a harmful or explosive substance and it is not feasible to provide a safe respirable atmosphere, an employer shall ensure that
(a) a worker entering the confined space is provided with and wears respiratory and personal protective equipment appropriate to the hazards likely to be encountered; and
(b) where a flammable or explosive gas or liquid is present all sources of ignition are controlled or eliminated.
(14) Where control measures referred to in subsection (13) cannot be implemented, a worker shall leave the confined space.
(15) Tests made under in subsection (11) shall be performed by a person who has been adequately trained in the proper use of testing and monitoring equipment.
(16) Equipment used in testing and monitoring shall be calibrated and monitored according to the manufacturer's instructions.
(17) The completed permit referred to in paragraph (2)(e) shall be made available at the time of entry to all authorized personnel by posting it at the entry portal or by another effective means.
Section 513 Work procedures
513. (1) An employer shall ensure that a worker who is required or permitted to enter a confined space in which a harmful atmosphere exists or may develop or where the worker may become entrapped by material
(a) wears appropriate retrieval equipment which would keep the worker in a position to be rescued; and
(b) has a life-line attached to the retrieval equipment which is tended at all times by a person, stationed outside the entrance to the confined space who shall be equipped for and capable of effecting rescue
and the employer shall prevent entanglement of life-lines and other equipment where one or more workers enter the confined space.
(2) Notwithstanding subsection (1), the use of a lifeline is not required where an obstruction or other condition makes its use impractical or unsafe but, in that case, an employer shall implement procedures to ensure the safety of the worker.
(3) Where a worker is required to enter a confined space the employer shall ensure that an attendant
(a) is assigned to the worker;
(b) is stationed outside and near
(i) the entrance to the confined space, or
(ii) where there is more than one entrance to the confined space, the one that best allows the attendant to perform the attendant's duties under subsection (4);
(c) is in continuous communication with the worker using the means of communication described in the relevant safe work procedure; and
(d) is provided with a device for summoning an adequate rescue response.
(4) An attendant shall not enter a confined space and shall, in accordance with the required safe work procedure,
(a) monitor the safety of the worker in the confined space;
(b) provide assistance to the worker; and
(c) summon an adequate rescue response where one is required.
[N.L.R. 43/22, s. 43]
Section 514 Entry into confined space
514. A confined space shall be entered only where
(a) the opening for entry and exit is sufficient to allow safe passage of a person wearing personal protective equipment;
(b) mechanical equipment in the confined space is
(i) disconnected from its power source, and
(ii) locked out and tagged;
(c) pipes and other supply lines whose contents are likely to create a hazard are blanked off;
(d) measures have been taken to ensure that, where appropriate, the confined space is continuously ventilated;
(e) liquid in which a person may drown or a free-flowing solid in which a person may become entrapped has been removed from the confined space;
(f) adequate explosion-proof illumination is provided where appropriate; and
(g) adequate barriers are erected to prohibit unauthorized entry.
Section 516 Rescue from confined space
516. An employer shall ensure that emergency rescue procedures are established and followed where workers are trained in the event of an accident or other emergency in or near the confined space, including immediate evacuation of the confined space.
CCOHS


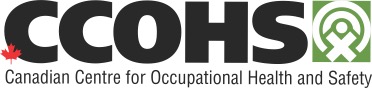