Emergency Response
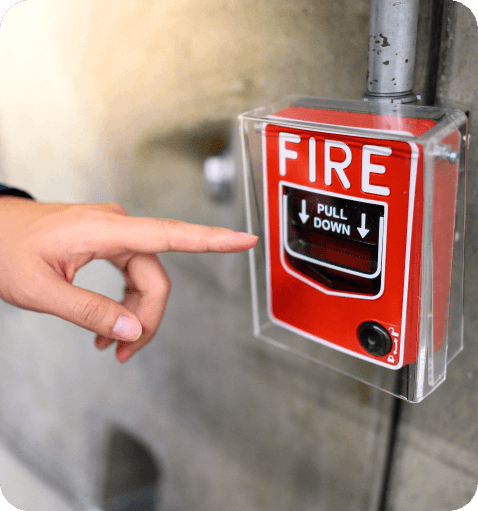
Highlighted words reveal definitions when selected.
When sudden or unexpected events occur, workplaces must be prepared to respond so that they can protect workers and the community, reduce financial losses, and resume business. An emergency response plan is an important part of an occupational health and safety program. It identifies potential emergency situations, sets procedures to follow, makes resources available, and defines the roles and responsibilities that individuals will follow.
Employer Responsibilities
Employers must:
- Conduct a risk assessment to determine when there may be a need to rescue or evacuate workers. [OHS Regs., s. 38(1)]
- Create written procedures for anticipated emergencies, and assign workers to coordinate them. [OHS Regs., s. 38(2)] Emergency procedures must be reviewed regularly and when there is a change that could affect the health and safety of workers.
- Create written rescue and evacuation procedures for hazardous work, including: [OHS Regs., s. 38(3)]
- Working at height;
- Work in a confined space or where there is a risk of entrapment;
- Work with hazardous substances;
- Underground work;
- Work in proximity to power lines;
- Work on or over water; and
- Workplaces where there are persons who require physical assistance to evacuate.
- Post information about escape routes and conduct emergency drills in workplaces the employer considers to be low risk. [OHS Regs., s. 38(4)]
- Instruct workers in the emergency response procedures applicable to their work, such as fire prevention and evacuation procedures. [OHS Regs., s. 41(1)]
- Make sure workers assigned to firefighting duties are given adequate training by a qualified instructor following National Fire Protection Association (NFPA) standards, at least once a year. [OHS Regs., s. 41 (2)(3)]
Where an employer is required to have an occupational health and safety program, it must include plans for emergency response. [OHS Regs., s. 12(1)(e) and (j)] Emergency response plans must be reviewed at least every three years, and when there are changes that could affect the health and safety of workers.
Where an employer requires a worker to work alone or in isolation, the employer must develop and follow written procedures for checking the well-being of the lone worker. Include check-in times and steps to take if the worker cannot be contacted. [OHS Regs., s. 15(4) and (5)]
Emergency exit routes [OHS Regs., s. 39(1) and (2]:
- Must allow for a quick, unobstructed exit.
- Must be created when the regular means of exit could become dangerous or unusable.
Emergency lighting [OHS Regs., s. 40]:
- Must be available where failure of the lighting system could be hazardous to a worker.
- Must be reliable during emergency shutdown procedures and evacuation.
Emergency shower and eyewash facilities:
- Must be available where a worker’s skin or eyes may be exposed to hazardous substances [OHS Regs., s. 42(11)] and [OHS Regs. s. 63(a)] be installed and maintained in accordance with ANSI Z358.1.
- Selection of an emergency shower or eyewash facility must be based upon a risk assessment and comply with the manufacturer's safety data sheet (SDS) or consumer product safety information. [OHS Regs., s. 42(5) and 63(d)]
- Where a plumbed system is used, it must be supplied with potable water. [OHS Regs., s. 63(b)]
- Where a self-contained system is used, it must be supplied with either potable water or isotonic saline flushing solution. [OHS Regs., s. 63(b)]
- Access to an emergency shower or eyewash facility must not be obstructed by material or equipment. [OHS Regs., s. 63(c)]
- Emergency shower and eyewash facilities must be supplied with water, or flushing solution, that is maintained at a temperature that comply with the ANSI standard or, if special circumstances exist, in accordance with SDS.
Fire prevention and control [OHS Regs., s. 443]
- The design and occupancy of structures including fire alarms, fire detection and fire protection equipment must comply with the Fire Protection Services Act and the National Fire Code of Canada.
- Fire alarms and fire detection equipment must be maintained according to the manufacturer’s instructions and applicable codes and standards under the Fire Protection Services Act.
- Where hazardous products could be a danger to firefighters, the local fire department must be notified of the location and safe handling procedures. This requirement does not apply if:
- Materials are kept on site for less than five days;
- The employer has another means of notifying firefighters (e.g. signage); or
- The workplace is not within the service area of a fire department.
Emergency drills [OHS Regs., s. 39]:
- Required at least annually to ensure the effectiveness of emergency exit routes and procedures. Emergency drills can be coordinated with local first responders in order to determine the effectiveness of their response capability.
- Must be recorded (in writing) and the record must be kept for five years.
Worker Responsibilities
Workers must:
- Take reasonable care to protect his or her health and safety and that of workers and persons at or near the workplace. [OHS Act, s. 6)]
- Properly wear or use personal protective equipment (PPE), safeguards and safety devices provided for their protection in accordance with the manufacturer’s instructions and training provided by the employer. [OHS Act, s. 7(a)(a.1)] [OHS Regs., s. 17]
- Follow emergency evacuation procedures.
- Participate in training, hazard assessments, and drills, if provided.
- Be properly trained for work, including emergency evacuation procedures and firefighting duties, as needed.
- Immediately report concerns and hazards to the supervisor or employer. [OHS Regs., s. 17(3)]
Related Topics
Emergency response plan
A set of written procedures to follow in case of an emergency.The procedures must include actions to be taken by the employer to reduce the impact of an emergency on people, equipment and the environment.
Occupational Health and Safety Program
Where 10 or more workers are employed at a workplace, the employer shall establish and maintain an occupational health and safety program in accordance with the regulations. [OHS Act, s. 36.1(1)] and [OHS Regs. s. 12]Risk assessment
A risk assessment is a thorough check of the work environment and task before work begins to identify hazards and includes evaluating and quantifying the risk associated with the hazards that have been identified.The purpose is to identify potential hazards and appropriate safety measures to be used to eliminate or reduce the hazards and to prioritize safety measures based on the rankings assigned to the hazards that have been identified.
Working at height
Fall protection is required for work where there is a hazard of falling: [OHS Regs., s. 141]- Three metres or more, above a safe surface or water;
- Above a surface or thing that could cause an injury if a worker did fall; or
- Above an open tank, pit or vat that contains hazardous material.
Confined space
An enclosed or partially enclosed space that:- Is not designed or intended for human occupancy except for the purpose of performing work;
- Has restricted means of access and egress; and
- May become hazardous to a person entering it as a result of:
- It's design, construction, location or atmosphere,
- The materials or substances in it, or
- Any other conditions relating to it. [OHS Regs., s. 511(2)]
Entrapment
A state of being caught or trapped by material or water.For example, the cave-in or collapse of the trench walls could cause workers inside the trench to become entrapped in soil.
Hazardous products
Means a product, material, mixture or substance classified under one or more of the hazard classes defined under the Canadian Hazardous Product Act.Escape routes
A predefined path of travel that has been designed to provide employees with a safe means of evacuating their workplace in the event of an emergency; or, if an exit is not possible or is unsafe, to a refuge shelter.The route itself must be clearly marked so that employees will not get lost, even in low-light conditions.
The route must be explained to employees in advance of an actual emergency, so they are familiar with the path they should take if an emergency occurs.
After an evacuation workers should gather in a designated area to be accounted for. This is often called a muster area.
Emergency drills
To minimize the impact of an emergency, it is important that every person knows exactly what to do.An emergency drill is a pre-arranged event whereby workers can practice emergency procedures, such as evacuation.
Emergency drills must be completed regularly, to ensure workers are aware of their duties and to account for changes to codes and standards.
Training
Firefighting training must include:- Fire suppression methods
- Fire prevention
- Emergency procedures
- Organization and chain of command
- Firefighting crew safety; and
- Communications according to National Fire Protection Association standards. [OHS Regs., s. 41]
National Fire Protection Association (NFPA)
The National Fire Protection Association (NFPA) is a USA organization that sets codes and standards.https://www.nfpa.org/
Working alone or in isolation
Working alone or in isolation means that assistance is not readily available in an emergency, or if you become injured or ill. [OHS Regs., s. 15(1)]Emergency shower and emergency eyewash facilities
An emergency shower is a plumbed, faucet-mounted, or self-contained device designed to rinse the worker's head and body.The facility must be installed and maintained in accordance with ANSI Z358.1
An eyewash facility is a plumbed, faucet-mounted, or self-contained device designed to rinse both eyes and the surrounding facial area.
The facility must be installed and maintained in accordance with ANSI Z358.1
ANSI
ANSI is the American National Standards Institute.Standards may be purchased from the ANSI store: https://webstore.ansi.org/
Safety data sheet (SDS)
A safety data sheet (SDS) is a document that contains information on the potential hazards of a hazardous substance, instructions on how to work safely with it, and actions to take in an emergency. A SDS should not be confused with the label; as it contains much more detailed information.Before using a hazardous product, it’s essential to conduct a risk assessment by reading and fully understanding the SDS.
Potable water
Potable is water that is safe to drink or to use for food preparation.Isotonic saline flushing solution
A mixture of sodium chloride and water.Fire Protection Services Act
The Fire Protection Act is available fromhttps://www.assembly.nl.ca/Legislation/sr/statutes/f11-01.htm
National Fire Code of Canada
The National Fire Code of Canada is available from the National Research Council athttps://nrc.canada.ca/en/certifications-evaluations-standards/codes-canada/codes-canada-publications/national-fire-code-canada-2015
Personal protective equipment
Any equipment or device which protects a worker's body from injury, illness or death. PPE acts as a barrier to protect the worker from the hazard.PPE should only be used:
- Where other controls are not available or adequate.
- As a short-term measure before controls are implemented.
- During activities such as maintenance, clean up, and repair where other controls are not feasible or effective.
- During emergency situations.
OCCUPATIONAL HEALTH AND SAFETY ACT
R.S.N.L. 1990, c. O-3
Section 6 Workers' general duty
6. A worker, while at work, shall take reasonable care to protect his or her own health and safety and that of workers and other persons at or near the workplace.
Section 7 Specific duties of workers
7. A worker
(a) shall co-operate with his or her employer and with other workers in the workplace to protect
(i) his or her own health and safety,
(ii) the health and safety of other workers engaged in the work of the employer,
(iii) the health and safety of other workers or persons not engaged in the work of the employer but present at or near the workplace;
(a.1) shall use devices and equipment provided for his or her protection in accordance with the instructions for use and training provided with respect to the devices and equipment;
(b) shall consult and co-operate with the occupational health and safety committee, the worker health and safety representative or the workplace health and safety designate at the workplace; and
(c) shall co-operate with a person exercising a duty imposed by this Act or regulations.
[S.N.L. 1999, c. 28, s. 3; 2001, c. 10, s. 26; 2004, c. 52, s. 2]
Section 36.1 Health and safety program
36.1 (1) Where 10 or more workers are employed at a workplace, the employer shall establish and maintain an occupational health and safety program in accordance with the regulations.
(2) An occupational health and safety program shall be established in consultation with the occupational health and safety committee at the workplace.
(3) An occupational health and safety program shall include those documents that may be prescribed in the regulations.
(4) An occupational health and safety program shall be in writing and shall, when requested, be provided to the occupational health and safety committee, a worker at the workplace and an officer.
[S.N.L. 2001, c. 10, s. 27; 2004, c. 47, s. 27]
Occupational Health and Safety Regulations, 2012
N.L.R. 5/12
Part III GENERAL DUTIES
Section 12 Occupational health and safety program
12. (1) An occupational health and safety program required under section 36.1 of the Act shall be signed and dated by the employer and by the person or persons responsible for the management of the employer's operations in the province and shall include:
(a) a statement of the employer's commitment to cooperate with the occupational health and safety committee and workers in the workplace in carrying out their collective responsibility for occupational health and safety;
(b) a statement of the respective responsibilities of the employer, supervisors, the occupational health and safety committee and workers in carrying out their collective responsibility for occupational health and safety;
(c) procedures to identify the need for, and for the preparation of written safe work procedures to implement health and safety practices, including practices required by the Act and the regulations, or as required by an officer;
(d) written work procedures appropriate to the hazards and work activity in the workplace;
(e) a plan for orienting and training workers and supervisors in workplace and job-specific safe work practices, plans, policies and procedures, including emergency response, that are necessary to eliminate, reduce or control hazards;
(f) provisions for establishing and operating an occupational health and safety committee, including provisions respecting
(i) maintenance of membership records,
(ii) procedural rules,
(iii) access by the committee to management staff with the authority to resolve health and safety issues and to information about the employer's operations required under the Act and the regulations, and
(iv) a plan for training committee members as required under the Act;
(g) a system for the recognition, evaluation and control of hazards that includes:
(i) evaluation and monitoring of the workplace to identify potential hazards and the associated risks,
(ii) procedures and schedules for regular inspections by management and committee members,
(iii) procedures for the identification, reporting and control or correction of hazards,
(iv) procedures for the prompt investigation of hazardous occurrences to determine the cause of the occurrence and the actions necessary to prevent a recurrence,
(v) identification of the circumstances where the employer is required to report hazards to the committee and the procedures for doing so, and
(vi) measures for the accountability of persons responsible for the reporting and correction of hazards;
(h) a plan for the control of biological and chemical substances handled, used, stored, produced or disposed of at the workplace and where appropriate, the monitoring of the work environment to ensure the health and safety of workers and other persons at or near the workplace;
(i) a system to ensure that persons contracted by the employer or for the employer's benefit comply with the program developed under this section and the Act and regulations;
(j) an emergency response plan;
(k) maintenance of records and statistics, including occupational health and safety committee minutes, reports of occupational health and safety inspections and investigations, with procedures to allow access to them by persons entitled to receive them under the Act; and
(l) provision for monitoring the implementation and effectiveness of the program.
(2) An employer that is required to establish and maintain an occupational health and safety program under section 36.1 of the Act shall
(a) implement the occupational health and safety program; and
(b) review and, where necessary, revise the occupational health and safety program as follows:
(i) at least every 3 years,
(ii) where there is a change of circumstances that may affect the health and safety of workers, and
(iii) where an officer requests a review.
Section 15 Working alone
15. (1) In this section, "to work alone or in isolation" means to work in circumstances where assistance would not be readily available to the worker
(a) in case of an emergency; or
(b) in case the worker is injured or in ill health.
(2) An employer shall conduct a risk assessment where a worker is assigned to work alone or in isolation;
(3) Where a risk assessment required under subsection (2) identifies a hazard, appropriate controls shall be implemented to eliminate, or where elimination is not practicable, minimize the risk associated with the hazard;
(4) An employer shall develop and implement a written procedure for checking the well-being of a worker assigned to work alone or in isolation;
(5) A procedure referred to in subsection (4) shall include the time interval between checks and the procedure to follow in case the worker cannot be contacted, including provisions for emergency response;
(6) A person shall be designated to establish contact with the worker at predetermined intervals and the results shall be recorded by the person;
(7) A procedure referred to in subsection (4) shall be developed in consultation with the worker assigned to work alone or in isolation, the occupational health and safety committee, the worker health and safety representative or designate, whichever applies;
(8) A procedure referred to in subsection (4) shall be reviewed at least annually, or more frequently if there is
(a) a change in work arrangements that may adversely affect a worker's well-being or safety; or
(b) a report that procedures are not working effectively.
Section 17 General duties of workers
17. (1) A worker shall make proper use of all necessary safeguards, protective clothing, safety devices, lifting devices or aids, and appliances
(a) designated and provided for the worker’s protection by the employer; or
(b) required under these regulations to be used or worn by a worker.
(2) A worker shall follow the safe work procedure in which the worker has been instructed.
(3) A worker shall immediately report a hazardous work condition that may come to the worker’s attention to the employer or supervisor.
[N.L.R. 43/22, s. 4]
Part V GENERAL HEALTH AND SAFETY REQUIREMENTS
Section 38 Emergency plan risk assessment
38. (1) An employer shall conduct a risk assessment in a workplace in which a need to rescue or evacuate workers may arise.
(2) Where the risk assessment required by subsection (1) shows a need for evacuation or rescue, appropriate written procedures shall be developed and implemented and a worker assigned to coordinate their implementation.
(3) Written rescue and evacuation procedures are required for but not limited to
(a) work at high angles;
(b) work in confined spaces or where there is a risk of entrapment;
(c) work with hazardous substances;
(d) underground work;
(e) work in close proximity to power lines;
(f) work on or over water; and
(g) workplaces where there are persons who require physical assistance to be moved.
(4) Where a workplace is a low risk workplace in the opinion of an employer, the employer shall post information about escape routes and conduct emergency drills the employer considers appropriate.
[N.L.R. 43/22, s. 10]
Section 39 Emergency procedures
39. (1) An emergency exit route shall be provided from a work area in which the malfunctioning of equipment or a work process could create an immediate danger to a worker and the regular means of exit could become dangerous or unusable.
(2) An emergency exit route shall be designed and marked to provide quick and unimpeded exit.
(3) At least once a year an emergency drill shall be held to ensure awareness and effectiveness of the emergency exit routes and procedure, and a record of the drill shall be kept for a period of 5 years.
Section 40 Emergency lighting
40. (1) Where a failure of a lighting system would create conditions dangerous to the health and safety of workers, an emergency lighting system shall be provided for the workplace and the exit routes.
(2) An emergency lighting system shall provide dependable illumination while the primary lighting system is off to enable all emergency measures to be carried out, including
(a) emergency shutdown procedures, and
(b) evacuation of workers from the premises.
Section 41 Emergency training
41. (1) A worker shall be given adequate instruction in the fire prevention and emergency evacuation procedures applicable to the workplace.
(2) A worker assigned to firefighting duties in a workplace shall be given adequate training by a qualified instructor in fire suppression methods, fire prevention, emergency procedures, organization and chain of command, firefighting crew safety and communications applicable to the workplace in accordance with National Fire Protection Association standards.
(3) Retraining for firefighting duties shall be provided periodically, but not less than once a year.
[N.L.R. 43/22, s. 11]
Part VI OCCUPATIONAL HEALTH REQUIREMENTS
Section 42 Hazardous substances
42. (1) An employer shall monitor the use or presence of substances at the workplace that may be hazardous to the health and safety of workers.
(2) In accordance with subsection (1), an employer shall implement a chemical and biological control program commensurate with the associated risks.
(3) In accordance with subsection (1), an employer shall eliminate hazardous substances from the workplace and where this is not practicable substitute a less hazardous substance.
(4) Where hazardous substances exist, an employer shall employ engineering and administrative controls to ensure their safe use.
(5) An employer shall ensure that a substance produced, used or handled at a workplace which by reason of toxicity, flammability or reactivity creates a risk to the health or safety of workers is controlled in accordance with the Safety Data Sheet or manufacturer's specifications.
(6) Where the minister determines that the use or presence of a hazardous substance at a place of employment may be injurious to the health of workers, the minister may inquire into the substance and may prohibit, restrict or modify the use of the substance until a time that an employer establishes to the minister that its use or presence is not injurious to the health of workers.
(7) An employer shall ensure that
(a) atmospheric contamination of the workplace by hazardous substances is kept as low as is reasonably practicable;
(b) a worker is informed of the nature and degree of health effects of the hazardous substances to which the worker is exposed;
(c) exposure of a worker to hazardous substances is as minimal as is reasonably practicable, and where a threshold limit value has been established by the ACGIH, exposure shall not exceed the threshold limit value;
(d) except as otherwise determined by the division, a worker is not exposed to a substance that exceeds the ceiling limit, short-term exposure limit or 8-hour TWA (time weighted average) limit prescribed by ACGIH; and
(e) where a substance referred to in paragraph (d) has an 8-hour TWA limit, a worker's exposure to the substance does not exceed
(i) 3 times the 8-hour TWA limit for more than a total of 30 minutes during the work period, and
(ii) 5 times the 8-hour TWA limit.
(8) Where extended work periods exist where the work period is more than 8 hours in a 24 hour day, the 8 hour exposure shall be adjusted accordingly as outlined in the ACGIH "Threshold Limit Values (TLVs)" Manual.
(9) Adjustment of TLVs, as required, shall be done in consultation with the occupational health and safety committee, the worker health and safety representative or the workplace health and safety designate, as appropriate.
(10) Where a worker is exposed to a substance which is designated as a reproductive toxin or a sensitizer, an employer shall develop policy and procedures appropriate to the risk, which may include protective reassignment.
(11) Where workers may be exposed to contact with chemicals harmful to the skin, facilities shall be available for the worker to effectively cleanse the contaminated body areas, including, where corrosive chemicals are involved, emergency water baths, showers, jump tanks, eyewash facilities or other effective means of treatment.
(12) The policy and procedures required by subsection (10) shall include
(a) informing workers about the reproductive toxin and identifying ways to minimize exposure to the toxin for a worker who has advised the employer of pregnancy or intent to conceive a child; and
(b) identifying ways to eliminate exposure to a sensitizer for a worker who is or may become sensitized to that substance.
(13) Solvents, oils, greases, paints or other flammable substances shall be cleaned up by using an approved non-combustible grease and oil absorbent which shall be placed in covered metal containers before disposal.
(14) Containers referred to in subsection (13) shall not be stored in work areas.
[S.N.L. 2019, c. 8, s. 20]
Section 63 Emergency washing facilities
63. An employer shall ensure that
(a) appropriate emergency washing facilities are provided in a work area where a worker's eyes or skin may be exposed to harmful or corrosive materials or other materials which may burn or irritate;
(b) only a potable water supply is used in a plumbed emergency eyewash facility and that only potable water or an isotonic saline flushing solution is used in a portable (non-plumbed) eyewash unit;
(c) access to emergency eyewash and shower facilities is not blocked by material or equipment; and
(d) selection of emergency washing facilities is based upon an assessment of the risks present in the workplace.
Part X FALL PROTECTION
Section 141 General requirements
141. Where a worker is exposed to the hazard of falling from a work area that is
(a) 3 metres or more above the nearest safe surface or water;
(b) above a surface or thing that could cause injury to the worker if the worker were to fall on the surface or thing; or
(c) above an open tank, pit or vat containing hazardous material,
the employer shall ensure that
(d) the worker is provided with a fall arrest system that meets the requirements of section 142;
(e) a guardrail that meets the requirements of section 28 is constructed or installed at the work area;
(f) a personnel safety net that meets the requirements of section 143 is installed at the work area;
(g) temporary flooring that meets the requirements of section 146 is constructed or installed at the work area; or
(h) the worker is provided with another means of fall protection that provides a level of safety equal to or greater than a fall arrest system that meets the requirements of section 142.
Part XX FIRE PREVENTION AND CONTROL
Section 443 Fire protection
443. (1) The design and occupancy of structures and the provision of fire alarm and detection equipment and fire protection equipment, in places of employment, shall comply with the Fire Prevention Act, 1991 and an employer shall ensure that work is carried out according to the applicable provisions of that Act and the National Fire Code.
(2) Fire alarm and detection equipment and fire protection equipment shall be maintained according to the manufacturer's instructions and any other requirements of provincial legislation.
(3) An employer that has
(a) controlled products as defined in the Workplace Hazardous Materials Information System (WHMIS) Regulations, 2018 ;
(b) explosives;
(c) pesticides;
(d) radioactive material;
(e) consumer products; or
(f) hazardous waste
in quantities which may endanger fire-fighters at a workplace shall ensure that the local fire department is notified of the nature and location of the hazardous materials or substances and methods to be used in their safe handling.
(4) Subsection (3) does not apply to a workplace:
(a) where materials are kept on site for less than 5 days, where the employer ensures that an alternate and effective means of notification of the fire department, appropriate to the hazard, is in place in the event of a fire or other emergency; or
(b) which is not within the service area of a fire department.
[S.N.L. 2019, c. 8, s. 20]
Part XXVII CONFINED SPACE ENTRY
Section 511 Confined space entry
511. (1) An employer shall perform an assessment of the work area to determine whether it contains a confined space.
(2) For the purpose of this Part, "confined space" means an enclosed or partially enclosed space that
(a) is not designed or intended for human occupancy except for the purpose of performing work;
(b) has restricted means of access and egress; and
(c) may become hazardous to a person entering it as a result of
(i) its design, construction, location or atmosphere,
(ii) the materials or substances in it, or
(iii) any other conditions relating to it.
(3) A worker shall not work in a confined space after January 1, 2013 unless the worker has completed a confined space entry program prescribed by the commission.
(4) An employer shall inform a worker who may have to work in a confined space of a hazard by posting signs or other equally effective means of advising of the existence of and dangers posed by confined spaces.
[N.L.R. 43/22, s. 42]
CCOHS


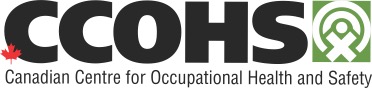