Marine Operations and Diving
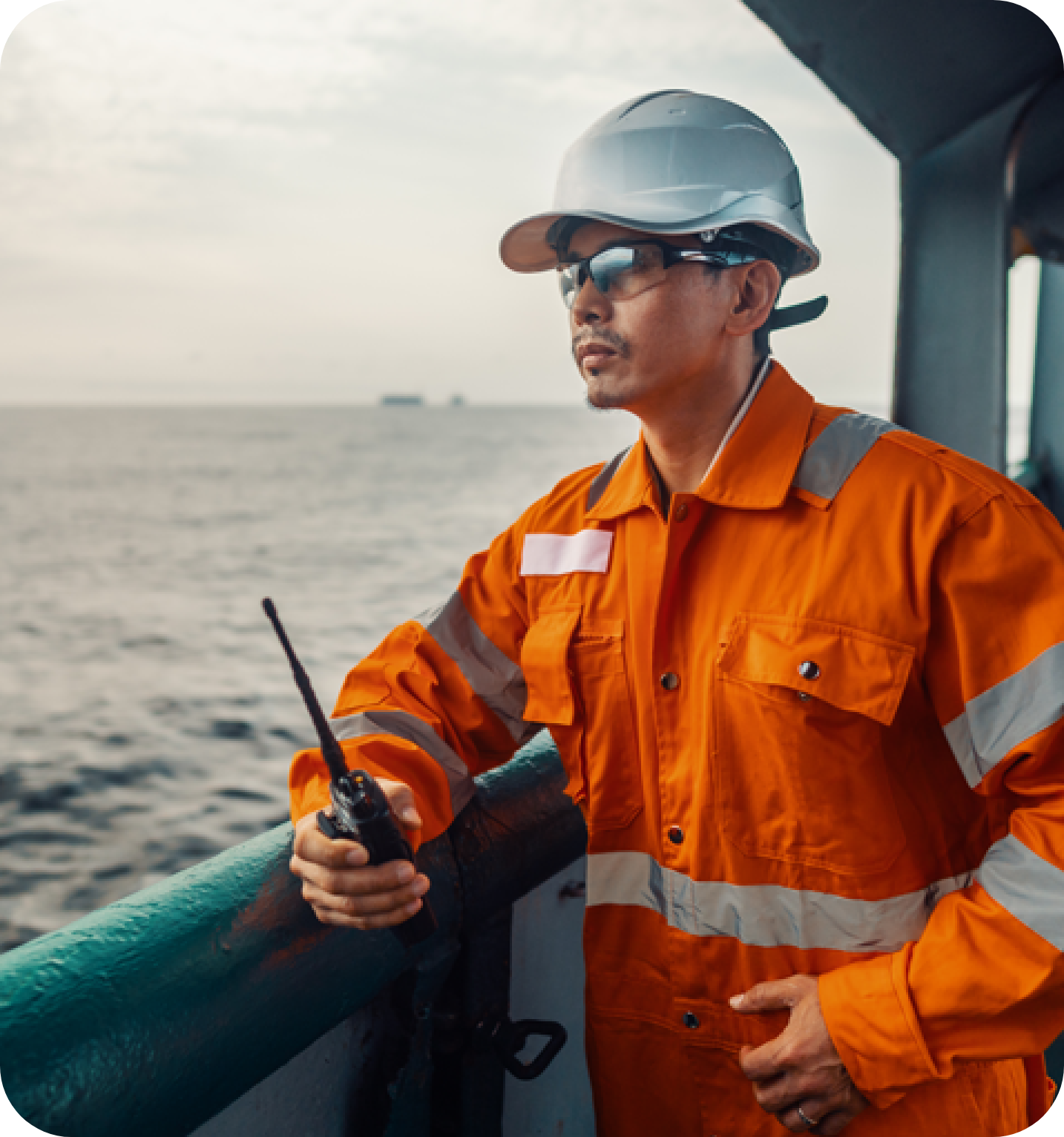
Highlighted words reveal definitions when selected.
In Newfoundland and Labrador, the sea is major part of our heritage and continues to be an important site for work. Work also takes place on, or near, the provinces ponds, lakes, rivers, and man-made water-bodies. Unfortunately, many Newfoundlanders and Labradorians have lost their lives or received serious injuries while working at sea or on or near other sources of water.
When performing marine operations or diving on, over, or near water (or ice), it is important that work is performed in accordance with the safety measures outlined by the OHS Act and Regulations. Marine operations and diving activities often occur in harsh environments with rapidly changing weather conditions. It is important that all persons remain alert to changing conditions and that employers and owners take all necessary precautions to keep workers safe in advance and during these conditions.
Note: If you are self-employed, you are still bound by the OHS Act and Regulations with respect to the duties of employers and workers, where applicable. [OHS Act, s. 9]
Employer Responsibilities
The employer must:
- Provide and maintain a workplace and the necessary equipment, systems, and tools in a manner that is safe and without risk to workers. [OHS Act, s. 5(a)]
- Provide the necessary information, instruction, training, supervision, and facilities. [OHS Act, s. 5(b)]
- Make sure workers, particularly supervisors, are made familiar with present and potential workplace hazards. [OHS Act, s. 5(c)]
- Make sure workers are given operating instructions for the personal protective equipment (PPE) or devices required for their protection from hazards. [OHS Act, s. 5(e)]
- Make sure that necessary PPE and devices are used. [OHS Regs., s. 14(2)]
- Make sure that all buildings, structures (both temporary and permanent), excavations, machinery, equipment, workstations, and places of employment:
- Can withstand the stresses likely to be imposed upon them, and can safely perform the function(s) for which they are used or intended. [OHS Regs., s. 14(1)]
- Are inspected regularly to find and correct unsafe working conditions. [OHS Regs., s. 18(1)]
- Make sure that safe work procedures are followed and they promote the safe interaction of workers and their work environment. [OHS Regs., s. 14(3)] [OHS Regs., s. 14(4)]
- Use qualified and properly instructed workers to take emergency action to correct the unsafe condition that has an immediate threat to workers. Take every possible effort to control the hazard while the corrective action is taking place. [OHS Regs., s. 18(3)]
- Make sure that all workers and other persons at the workplace are informed of the hazards to which they are likely to be exposed and what controls they must use to protect themselves and others. [OHS Regs., s. 19(1)]
- Conduct a risk assessment in a workplace that where a need to rescue or evacuate workers may arise. When the risk assessment identifies a need for evacuation or rescue, develop written rescue and evacuation procedures and assign a worker to coordinate their implementation. Written rescue and evacuation procedures are required for work on or over water. [OHS Regs., s. 38]
Travel over and work on ice
Where a worker is to travel over or work on ice and the water beneath the ice is more than one meter deep at any point, the employer must: [OHS Regs., s. 27]
- Make sure the ice is able to support the load to be placed on it; and
- Test the ice before work begins and as often during the work as necessary to make sure a workers' safety is maintained.
Work on a marine vessel
The following safety requirements are essential to eliminate or overcome specific hazards when working on a vessel.
Slipping and tripping hazards
To reduce or eliminate slipping and tripping hazards, the employer must:
- Keep a work area on a vessel clear of unnecessary obstructions and free of slipping and tripping hazards. [OHS Regs., s. 469(1)]
- Have non-skid deck surfaces except where a smooth deck is required for handling fish. [OHS Regs., s. 469(2)]
- Store the tools and equipment when not in use. [OHS Regs., s. 469(3)]
- Install floor drains or other suitable means (e.g., an approved non-combustible spill absorbent) to eliminate slipping or other hazards where the regular work processes result in liquid spilling onto the floor or work areas. [OHS Regs., s. 34(1) and (2)]
- During wet operations, maintain reasonable drainage, provide false floors, platforms, mats, or other dry-standing places, and keep those areas clean. [OHS Regs., s. 34(3)]
Galley requirements
To restrain the movement of cooking equipment and to prevent unintentional contact by a crewmember, the employer must: [OHS Regs., s. 470]
- Fit the galley stove on a vessel with rails and use other means for cooking utensils,
- Fit stove fuel supply tanks and line with a shutoff valve at the tanks and do not locate these valves directly above the stove.
- Secure the galley stoves and have sufficient clearance for effective cleanup of oil and grease.
Wharves, platforms, ladders and gangplanks
To make sure that accessways are safe and adequate on board a vessel, the employer must:
- Keep floors, platforms, wharf decks, and floating equipment in good repair and free from hazards. [OHS Regs., s. 462(1)]
- Provide a clear passageway on a wharf deck when handling lines. [OHS Regs., s. 462(2)]
- Install curbs and bull rails on the open sides of floats, docks, wharves, piers, and other areas where powered mobile equipment is used. [OHS Regs., s. 462(3)]
- Construct the curbs or bull rails substantially with a height of at least 25.40 centimetres above the deck level. [OHS Regs., s. 462(4)]
- Provide a dock, wharf, or pier with ladders regularly spaced at intervals not exceeding 30.5 metres about its perimeter that extend from the deck to a minimum one meter below water level. [OHS Regs., s. 463(1)]
- Provide a fixed or portable ladder, gangplank, or other safe means to board and leave floating equipment. [OHS Regs., s. 463(2)] Secure a portable means of access to prevent it from becoming dislodged. [OHS Regs., s. 463(3)]
- Provide a gangplank with a guardrail and make sure the surface of the gangplank is non-slip. [OHS Regs., s. 463(4) and (5)] Guardrails must be constructed in accordance with legislation. [OHS Regs., s. 28]
- Make sure the ship's ladder is engineered or constructed to a standard acceptable to OHS Division. [OHS Regs., s. 156]
- Make sure a professional engineer or another person acceptable to OHS Division designs a floating work platform. [OHS Regs., s. 465(1)]
- Make sure the floating work platform is stable and without excessive movement. [OHS Regs., s. 465(2)]
Fire prevention and control
To prevent and reduce the risk of a fire onboard a vessel, the employer must:
- Make sure the design and occupancy of structures, and any fire alarm, detection, and fire protection equipment meet the requirements of the Fire Protection Services Act, 1991. Make sure work is carried out according to the Fire Prevention Act and the National Fire Code of Canada. [OHS Regs., s. 443(1)]
- Maintain fire alarms, fire detection, and firefighting equipment according to the manufacturer's instructions and legislative requirements. [OHS Regs., s. 443(2)]
- Notify the local fire department of WHMIS controlled products, explosives, consumer products, or hazardous waste when it is present in quantities at a workplace that may endanger firefighters, if a fire was to occur. [OHS Regs., s. 443(3)] The employer is not required to notify the local fire department where materials are kept on site for less than 5 days and the employer has ensured another effective means to notify the fire department which is appropriate to the hazard, nor where the workplace is not within the service area of a fire department. [OHS Regs., s. 443(4)]
- Institute a system of inspections and tests to determine the presence of a volatile or flammable substances, gases or vapours before work begins in a bilge, tank, compartment, or cargo space of marine equipment. [OHS Regs., s. 444(1)]
- Provide ventilation or other effective means to remove or control volatile or flammable substances, gases, or vapours present, or that arise from a work process. [OHS Regs., s. 444(2)]
- Maintain a flammable liquid, vapour, or gas concentration sufficiently below the lower explosive limit (LEL) of the substance used to protect workers and meet regulatory requirements. [OHS Regs., s. 444(3)]
- Use a container to carry, transfer, or store a flammable solvent that meets the CSA standards. Electrically ground and bonded the container during the transfer of contents from one container to another. [OHS Regs., s. 444(4)]
- Place waste material contaminated with a solvent, oil, grease, paint, or other flammable substance in covered metal containers before disposal and do not store them in work areas. [OHS Regs., s. 444(5)]
- Eliminate or control existing or potential sources of ignition where a volatile or flammable substance, gas, or vapour is present or arises out of material, equipment, or work process. [OHS Regs., s. 444(6) and (7)]
Where work involves more than one employer, a principal contractor must make sure that ignition sources resulting from the work of one employer are eliminated or adequately controlled where flammable gas or a flammable liquid is handled, used, or stored by another employer. [OHS Regs., s. 444(8)]
Lifesaving equipment and personal flotation devices
Where a worker is in danger of drowning, employers must:
- Provide and maintain appropriate lifesaving equipment that is positioned at intervals not exceeding 50 metres, and is located in easily recognised places near dangerous areas. [OHS Regs., s. 464(1)]
- Make sure a throwing line fitted to a lifebuoy or similar equipment is of suitable size and length, and is made of a buoyant material. [OHS Regs., s. 464(2)]
- Provide lifesaving equipment that meets the requirements of standards acceptable to OHS Division. [OHS Regs., s. 464(3)]
- Provide a suitable boat and keep it ready for immediate use where a boat is necessary to rescue or evacuate a worker. [OHS Regs., s. 464(4)]
- Make sure a personal floatation device (PFD):
- Is labelled;
- Meets the requirements and approvals of Transport Canada, or another equivalent standard, such as the Canadian Coast Guard; and [OHS Regs., s. 466(2)]
- Provides a minimum buoyancy of 150 N (or 34 lbs), will inflate automatically upon immersion in water, and can also be inflated by manual activation or inflation by mouth. A PFD must not be used if it relies solely on manually activation to provide the buoyant effect. The manufacturers documentation must verify that the device meets these requirements. [OHS Regs., s. 466(4)]
Note: A personal flotation device (PFD) or lifejacket is not required when a personal fall arrest system, safety net, or other equivalent means is used. [OHS Regs., s. 466(3)]
Boatswain’s chairs
When worker use a boatswain's chair, the employer must:
- Make sure it meets the applicable CSA standard (e.g., CAN3-Z271 Safety code for suspended powered platforms, CAN/CSA-Z91 Health and safety code for suspended equipment operations, etc.), or be stamped, sealed, or otherwise documented as acceptable by a professional engineer. [OHS Regs., s. 243(1)]
- Request permission from OHS Division before using a boatswain chair at heights that exceed 92 metres. [OHS Regs., s. 243(9)]
- Inspect the system before use each day and do not use the system if any component is found to be defective. [OHS Regs., s. 243(10)]
- Make sure it provides stable and adequate support for the user. [OHS Regs., s. 243(2)]
- Make sure it is suspended from a parapet clamp, cornice hook, thrust-out beam, or other solid anchorage that is capable of providing support equivalent to or greater than that of the suspension system for the boatswain's chair. [OHS Regs., s. 243(3)]
- Positively secure the counterweight to thrust outs and tie back to an anchor capable of withstanding 22 kilonewtons static load, where a counterweight configuration is not designed into the building or structure. [OHS Regs., s. 243(4)]
- Make sure rope used to suspend a boatswain's chair is synthetic fibre rope with a breaking strength of at least 27 kilonewtons and be of a type compatible with the rigging hardware used in the suspension system, unless it is part of a block and tackle system. [OHS Regs., s. 243(6)]
- Make sure, when a boatswain's chair is supported by block and tackle: [OHS Regs., s. 243(5)]
- The rope used is synthetic fibre with a breaking strength of at least 22 kilonewtons;
- The rope is threaded through not less than one single lower block and one double upper block and be secured to prevent the rope from moving freely; and
- Block hooks are prevented from slipping from an eye, or be otherwise secured from being dislodged.
- Make sure wire rope used to suspend a boatswain's chair is recommended by the rope manufacturer or a professional engineer, and it is suitable for the hoist being used. [OHS Regs., s. 243(7)]
- Make sure a personal fall arrest system, independent of the boatswain's chair system, is used when workers are working at height. [OHS Regs., s. 243(8)]
Commercial diving
Where workers are involved in commercial diving operations, the employer must follow these standards: [OHS Regs., s. 467(1)]
- CAN/CSA-Z275.4-02 Competency Standard for Diving Operations; and
- CAN/CSA-Z275.2-04 Occupational Safety Code for Diving Operations.
Note: CAN/CSA-Z275.4-02 has been modified by the Newfoundland and Labrador regulations when the standard is applied to seafood harvesting and aquaculture diving operations. In these cases, Clause 7, SCUBA Supervisor (Restricted and Unrestricted) is deleted and replaced with “individuals who have successfully completed a five-day Surface Safety Attendant's course approved by the commission may supervise seafood harvesting and aquaculture diving operations”. [OHS Regs., s. 467(2)]
Fish harvesting
Before each fishing season, the master must: [OHS Regs., s. 468(1)]
- Make sure that all crew members are instructed in the operational characteristics of the fishing vessel, including:
- The location and use of safety equipment, emergency equipment, including firefighting and radio equipment, engine room components, and controls;
- Deck equipment and rigging;
- Navigation equipment and electronic aids;
- Fishing equipment and its use, including safe work practices for each fishery the vessel may be engaged in;
- Procedures for anchoring the vessel; and
- Escape routes in the event of a fire.
- Provide new crew members at the time of their joining the vessel with all the operational instructions. [OHS Regs., s. 468(3)]
- Make sure the instructions given to each crewmember is applied, when required, to protect their health and safety. [OHS Regs., s. 468(2)]
Underwater blasting, misfire, and fire prevention
Where workers are involved in under water blasting, the employer must:
- Make sure blasting is performed under the direct supervision of a blaster who is present at the project and who holds a valid blaster’s certificate which authorizes the performance of the particular type of work that the blaster is to conduct or supervise. [OHS Regs., s. 419]
- Make sure a safe work procedure is developed and employed when: [OHS Regs., s. 440 (1)]
- Handling explosives underwater:
- Using explosives for oil and gas well control; and
- Using explosives for ice control.
- Make sure the blaster has taken appropriate steps to protect leg wires, drill cuttings, and holes before leaving loaded holes unattended, where seismic blasting is carried out in an isolated location. [OHS Regs., s. 441(1)]
- Make sure workers carry out a seismic blasting operation safely. The firing line may only be left connected to the firing switch and disconnected at the hole, where a recorder can confirm complete detonation. [OHS Regs., s. 441(2)]
- A misfired or unfired charge may be left unfired where: [OHS Regs., s. 441(3)]
- It cannot be conventionally and safely detonated;
- It is being used in an isolated location and is a minimum of six metres deep; and
- Its location is marked effectively.
- Do not use a seismic water tank truck with open flame water heaters to transport explosives, unless: [OHS Regs., s. 441(4)]
- The distance between the heat tube and the outside of the tank is at least 35 centimetres;
- A woodburning heater includes a fire box that fully contains the fuel and has two dampers mounted in the heat tube, one at the vent end and one at the fire box, so the flame may be extinguished instantaneously, in the event of an accident; and
- The detonator storage is located on the opposite side of the vehicle from the explosive magazine, and both the detonator storage and the explosive magazine are built to type six magazine standard in accordance with the Explosives Act and Regulations.
- Allow a vehicle to drive over a loaded hole, only where there is no alternate route and the following conditions are met: [OHS Regs., s. 441(5)]
- Bypassing the hole is not practical;
- Operational planning minimizes the requirement to travel through an area with loaded hole(s);
- Safe work procedures are developed and communicated to workers before work is started;
- Loaded holes are left unattended as permitted;
- Explosive charges are at a minimum depth of six metres;
- Radio transmission equipment is turned off, or transmission capability is disabled by disconnecting the microphone; and
- Electrical equipment, including cellular phones and other types of mobile telephone equipment which continuously transmit radio signals are turned off when driving over the loaded hole.
- Make sure that the following steps are taken during a misfired or suspected misfired:
- A person must not move about the danger area until the required waiting time has ended. [OHS Regs., s. 442(1) and (2)]
- A person must not use metallic equipment in the blasting area until a blaster has inspected the site and given authority to use the equipment, and the following conditions are met: [OHS Regs., s. 442(3)]
- The work site is fully illuminated;
- The Blaster is in constant and direct supervision of the work; and
- Precautions are taken to prevent injury from an accidental explosion.
- Treat a misfire at a safe and suitable time and under the direction of a blaster. [OHS Regs., s. 442(4)]
- In consultation with a supervisor, a blaster must determine the safest and most practical means of treating a misfire, either by blasting again or otherwise complying with the requirements in a manner that ensures compliance with the regulations. [OHS Regs., s. 442(5)]
- Identify the cause of a misfire, where practicable, and take corrective action(s) to prevent a similar event from occurring in the future. [OHS Regs., s. 442(6)]
The employer and blaster must make sure the blast site is attended and barricaded, and post warning signs (“Danger”, “Explosives” or “Keep Out”) or flag the blast site when explosive materials and initiating systems are onsite.
If there has been a theft, or attempted theft of explosives, the employer must immediately report the incident to OHS Division by phone.
If there has been a blasting accident resulting in an injury or unusual occurrence, the employer must immediately report the incident to OHS Division by phone. They must also submit a written report to OHS Division within 24 hours. This report must include:
- The names and certificate numbers of all the blasters;
- The names and occupations of the injured workers;
- The types of explosives, detonators, and blasting machines involved;
- The nature of the accident (i.e., what happened);
- The date, time, and place; and
- Any actions taken by the employer.
Worker Responsibilities
Workers must:
- Use or wear all necessary PPE and safety devices according to manufactures instructions and training. This requirement includes wearing a personal floatation device (PFD) when there is a risk of drowning. [OHS Act, s. 7(a.1)] [OHS Regs., s. 17(1)] [OHS Regs., s. 466(1)]
- Follow safe work practices and procedures. [OHS Regs., s. 17(2)]
- Immediately report hazards to the supervisor or employer. [OHS Regs., s. 17(3)]
- Not carry out work, or operate a tool, appliance, or equipment, where a present or potential hazard creates an imminent danger to themselves or others. [OHS Act, s. 8]
- Participate in training and hazard assessments, where it is offered.
- Not use equipment or perform work tasks where the required training has not yet taken place.
Related Topics
Self-employed person
A person who is engaged in an occupation on his or her own behalf. [OHS Act, s. 2(k)]Personal protective equipment
Any equipment or device which protects a worker's body from injury, illness or death. PPE acts as a barrier to protect the worker from the hazard.PPE should only be used:
- Where other controls are not available or adequate.
- As a short-term measure before controls are implemented.
- During activities such as maintenance, clean up, and repair where other controls are not feasible or effective.
- During emergency situations.
Risk assessment
A risk assessment is a thorough check of the work environment and task before work begins.The purpose is to identify potential hazards and appropriate safety measures to be used to eliminate or reduce the hazards.
Fire Protection Services Act
The Fire Protection Act is available fromhttps://www.assembly.nl.ca/Legislation/sr/statutes/f11-01.htm
National Fire Code of Canada
The National Fire Code of Canada is available from the National Research Council athttps://nrc.canada.ca/en/certifications-evaluations-standards/codes-canada/codes-canada-publications/national-fire-code-canada-2015
WHMIS
Workplace Hazardous Materials Information System (WHMIS) is a standardized system which includes rules for hazard classification, labelling, safety data sheets (SDSs), and worker education and training. It provides workers with important health and safety information about hazardous substances in the workplace.
Lower explosive limit (LEL)
Explosive gases and vapours only pose a risk to workers when the fuel to oxygen ratio is in the correct range. This is known as the explosive range.The upper and lower limits of this range are known as the upper explosive limit (UEL) and lower explosive limit (LEL), respectively.
When the fuel to oxygen ratio is below the LEL, there is not enough fuel to ignite the mixture. Likewise, when the fuel to oxygen ratio is above the UEL, there is not enough oxygen to ignite the mixture.
%LEL refers to the amount of fuel relative to the LEL.
Source of ignition
A source of ignition includes an open flame, spark-producing mechanical equipment, welding and cutting processes, smoking, static discharge, electrical equipment or an installation that is not approved for hazardous locations, as specified by the Canadian Electrical Code. [OHS Regs., s. 444(7)]Transport Canada
A federal institution, leading the Transport Canada portfolio and working with our partners. Transport Canada is responsible for transportation policies and programs. They promote safe, secure, efficient and environmentally responsible transportation.https://tc.canada.ca/en
Boatswain's chair
A seat composed of a plank suspended in a horizontal position from ropes, used by persons who work on the exteriors of buildings, ships, etc. Also known as a bosun's chair.CSA
CSA is the Canadian Standards Association Group. Certain CSA standards are available for online viewing.To access these, you must first create an account with "CSA Communities".
Go to: https://community.csagroup.org/login.jspa?referer=%252Findex.jspa
Once you are logged in, click on the text below the "OHS Standards / View Access" graphic.
Click on the jurisdiction of your choice to see the CSA Standards as referenced in that legislation.
Standards may also be purchased from CSA Group: https://store.csagroup.org/
SCUBA
A self-contained underwater breathing apparatus.Master
A person in overall command of a commercial fishing vessel but does not include a pilot. [OHS Regs., s. 461(b)]Blaster
A person who holds a valid blaster’s certificate granted by the province. [OHS Regs., s. 417]OCCUPATIONAL HEALTH AND SAFETY ACT
R.S.N.L. 1990, c. O-3
Section 2 Definitions
2. In this Act
(a) "assistant deputy minister" means an assistant deputy minister appointed under section 9 of the Executive Council Act for the proper conduct of this Act;
(b) "board" means the Labour Relations Board referred to in the Labour Relations Act;
(c) "committee" means an occupational health and safety committee referred to in this Act;
(d) "council" means the Occupational Health and Safety Council referred to in this Act;
(e) "division" means the Occupational Health and Safety Division;
(f) "employer" means a person who employs 1 or more workers;
(g) "minister" means the minister appointed under the Executive Council Act to administer this Act;
(h) "occupation" means employment prescribed by the regulations as an occupation;
(i) "officer" means an occupational health and safety officer appointed under this Act and includes a medical practitioner providing services under section 20 while he or she is providing those services;
(j) "principal contractor" means the person primarily responsible for the carrying out of a project and includes the person who owns the thing in respect of which the project is being carried out;
(k) "self-employed person" means a person who is engaged in an occupation on his or her own behalf;
(k.1) "supervisor" means a person authorized or designated by an employer to exercise direction and control over workers of the employer;
(l) "supplier" means a person who rents or leases tools, appliances or equipment to be used by a worker;
(m) "worker" means a person engaged in an occupation; and
(n) "workplace" means a place where a worker or self-employed person is engaged in an occupation and includes a vehicle or mobile equipment used by a worker in an occupation.
[S.N.L. 1999, c. 28, s. 1; 2006, c. 16, s. 1; 2009, c. 19, s. 1]
Section 5 Specific duties of employers
5. Without limiting the generality of section 4, an employer
(a) shall, where it is reasonably practicable, provide and maintain a workplace and the necessary equipment, systems and tools that are safe and without risk to the health of his or her workers;
(b) shall, where it is reasonably practicable, provide the information, instruction, training and supervision and facilities that are necessary to ensure the health, safety and welfare of his or her workers;
(c) shall ensure that his or her workers, and particularly his or her supervisors, are made familiar with health or safety hazards that may be met by them in the workplace;
(d) shall, where it is reasonably practicable, conduct his or her undertaking so that persons not in his or her employ are not exposed to health or safety hazards as a result of the undertaking;
(e) shall ensure that his or her workers are given operating instruction in the use of devices and equipment provided for their protection;
(f) shall consult and co-operate with the occupational health and safety committee, the worker health and safety representative or the workplace health and safety designate, where the employer is not the workplace health and safety designate, on all matters respecting occupational health and safety at the workplace;
(f.1) shall respond in writing within 30 days to a recommendation of
(i) the occupational health and safety committee at the workplace,
(ii) the worker health and safety representative at the workplace, or
(iii) where the employer is not the workplace health and safety designate, the workplace health and safety designate at the workplace
indicating that the recommendation has been accepted or that it has been rejected, with a reason for the rejection;
(f.2) shall provide periodic written updates to
(i) the occupational health and safety committee at the workplace,
(ii) the worker health and safety representative at the workplace, or
(iii) where the employer is not the workplace health and safety designate, the workplace health and safety designate at the workplace
on the implementation of a recommendation accepted by the employer until the implementation is complete;
(f.3) shall consult with
(i) the occupational health and safety committee at the workplace,
(ii) the worker health and safety representative at the workplace, or
(iii) where the employer is not the workplace health and safety designate, the workplace health and safety designate at the workplace
about the scheduling of workplace inspections that are required by the regulations, and ensure that the committee, the worker health and safety representative or the workplace health and safety designate participates in the inspection; and
(g) shall co-operate with a person exercising a duty imposed by this Act or regulations.
[S.N.L. 1999, c. 28, s. 2; 2001, c. 10, s. 25; 2004, c. 52, s. 1]
Section 7 Specific duties of workers
7. A worker
(a) shall co-operate with his or her employer and with other workers in the workplace to protect
(i) his or her own health and safety,
(ii) the health and safety of other workers engaged in the work of the employer,
(iii) the health and safety of other workers or persons not engaged in the work of the employer but present at or near the workplace;
(a.1) shall use devices and equipment provided for his or her protection in accordance with the instructions for use and training provided with respect to the devices and equipment;
(b) shall consult and co-operate with the occupational health and safety committee, the worker health and safety representative or the workplace health and safety designate at the workplace; and
(c) shall co-operate with a person exercising a duty imposed by this Act or regulations.
[S.N.L. 1999, c. 28, s. 3; 2001, c. 10, s. 26; 2004, c. 52, s. 2]
Section 8 Imminent danger
8. A worker shall not
(a) carry out work where there exists an imminent danger to his or her or another worker's health or safety or the health or safety of another person; or
(b) operate a tool, appliance or equipment that will create an imminent danger to his or her or another worker's health or safety or the health or safety of another person.
Section 9 Duty of self-employed person
9. A self-employed person is bound by this Act with respect to the duties of employers or workers where these provisions are applicable.
Occupational Health and Safety Regulations, 2012
N.L.R. 5/12
Part III GENERAL DUTIES
Section 14 General duties of employers
14. (1) An employer shall ensure, so far as is reasonably practicable, that all buildings, structures, whether permanent or temporary, excavation, machinery, workstations, places of employment and equipment are capable of withstanding the stresses likely to be imposed upon them and of safely performing the functions for which they are used or intended.
(2) An employer shall ensure that necessary protective clothing and devices are used for the health and safety of the employer’s workers.
(3) The employer shall ensure that safe work procedures are followed at all workplaces.
(4) An employer shall ensure, so far as is reasonably practicable, that work procedures promote the safe interaction of workers and their work environment to minimize the potential for injury.
[N.L.R. 43/22, s. 3]
Section 17 General duties of workers
17. (1) A worker shall make proper use of all necessary safeguards, protective clothing, safety devices, lifting devices or aids, and appliances
(a) designated and provided for the worker’s protection by the employer; or
(b) required under these regulations to be used or worn by a worker.
(2) A worker shall follow the safe work procedure in which the worker has been instructed.
(3) A worker shall immediately report a hazardous work condition that may come to the worker’s attention to the employer or supervisor.
[N.L.R. 43/22, s. 4]
Section 18 Safety inspections
18. (1) Regular inspections of all buildings, excavations, structures, machinery, equipment, work practices and places of employment shall be made by the employer or the employer’s representative at intervals to ensure that safe working conditions are maintained and that unsafe conditions found as a result of the inspection are remedied without delay.
(2) Where an unsafe condition is discovered by a person, it shall be reported as soon as practicable to a supervisor who shall ensure that appropriate action is taken, without delay, to prevent a worker from being injured.
(3) Where emergency action is required to correct a condition that constitutes an immediate threat to workers, only those qualified and properly instructed workers necessary to correct the unsafe condition shall be exposed to the hazard and every possible effort shall be made to control the hazard while the corrective action is taking place.
[N.L.R. 43/22, s. 5]
Section 19 Co-ordination of work
19. (1) An owner shall ensure that all workers and other persons at the workplace are informed of
(a) the hazards of an owner's operations or site conditions; and
(b) the health and safety activities to be used to address the hazards.
(2) A principal contractor shall ensure work schedules and tasks are organized to provide safe working conditions for workers.
Part V GENERAL HEALTH AND SAFETY REQUIREMENTS
Section 27 Travel over and work on ice
27. (1) Where a worker is to travel over or work on ice and the water beneath the ice is more than one metre deep at any point, the employer of the worker shall ensure the ice supports the load to be placed on it.
(2) The employer shall test the ice for the purpose of subsection (1)
(a) before work begins; and
(b) as often during the work as necessary to ensure the safety of the workers.
Section 28 Guardrails
28. (1) Guardrails shall be installed where an open-sided floor, working platform, runway, walkway or balcony is over 1.22 metres above the existing floor or ground level.
(2) Detour guardrails shall be installed where a stairway ends in direct proximity to dangerous traffic or other hazards.
(3) An employer shall ensure that a guardrail is secured so that it cannot move in any direction if it is struck or if a point on it comes in contact with a worker, materials or equipment.
(4) Guardrails shall be installed on walkways over open tanks containing harmful substances or over open tanks 1.22 metres or more in depth.
(5) Walkways and platforms installed over machinery and work areas shall be equipped with toe boards at least 10 centimetres high along all sides of the walkway or platform.
(6) A guard rail shall have a top rail located at least .9 metres but not more than 1.1 metres above the working surface and an intermediate rail located midway between the top rail and the working surface.
Section 34 Slipping hazards
34. (1) Where the regular work process results in liquid spilling on to the floor or work areas, and where this spillage could introduce a slipping or other hazard, floor drains shall be installed or other suitable means used or adopted to eliminate this hazard.
(2) Only an approved non-combustible grease and oil absorbent shall be used to eliminate a hazard referred to in subsection (1).
(3) Where wet processes are used, an employer or contractor shall ensure that reasonable drainage is maintained and that false floors, platforms, mats or other dry standing places are provided and kept clean.
Section 38 Emergency plan risk assessment
38. (1) An employer shall conduct a risk assessment in a workplace in which a need to rescue or evacuate workers may arise.
(2) Where the risk assessment required by subsection (1) shows a need for evacuation or rescue, appropriate written procedures shall be developed and implemented and a worker assigned to coordinate their implementation.
(3) Written rescue and evacuation procedures are required for but not limited to
(a) work at high angles;
(b) work in confined spaces or where there is a risk of entrapment;
(c) work with hazardous substances;
(d) underground work;
(e) work in close proximity to power lines;
(f) work on or over water; and
(g) workplaces where there are persons who require physical assistance to be moved.
(4) Where a workplace is a low risk workplace in the opinion of an employer, the employer shall post information about escape routes and conduct emergency drills the employer considers appropriate.
[N.L.R. 43/22, s. 10]
Part XI SCAFFOLDS, STAGES AND WORK PLATFORMS
Section 156 Special purpose ladders
156. A special purpose ladder, including a ship's ladder, escape ladder, individual rung ladder or a ladder visible to the audience in a theatre scenic unit or prop, shall be engineered or constructed to a standard acceptable to the minister.
Section 243 Boatswain's chairs
243. (1) A boatswain's chair shall meet the requirements of the applicable CSA standard or be acceptable to a professional engineer.
(2) A boatswain's chair shall provide stable and adequate support for the user.
(3) A boatswain's chair shall be suspended from a parapet clamp, cornice hook, thrust-out beam or other solid anchorage having a working load limit at least equivalent to that of the suspension system for the boatswain's chair.
(4) A counter weight shall be
(a) positively secured to thrust outs; and
(b) tied back to an anchorage that is capable of withstanding 22 kilonewtons static load where a counter weight configuration has not been designed into the building.
(5) Where a boatswain's chair is supported by block and tackle
(a) the rope shall be synthetic fibre rope with a breaking strength of at least 22 kilonewtons;
(b) the rope shall be reeved through not less than one single lower block and one double upper block and secured to prevent the line from free running; and
(c) block hooks shall be moused, or otherwise secured against dislodgement.
(6) Fibre rope used to suspend a boatswain's chair other than with a block and tackle system shall be synthetic fibre rope having a breaking strength of at least 27 kilonewtons and of a type compatible for use with the rigging hardware in the suspension system.
(7) Wire rope used to suspend a boatswain's chair shall be a type recommended for that use by the rope manufacturer or a professional engineer and suitable for the hoist being used.
(8) A worker in a boatswain's chair which is 3 metres or more above grade or a safe lower landing, or where a fall from a lesser height may involve an unusual risk of injury, shall use a personal fall arrest system meeting the requirements of Part X independent of the boatswain's chair system.
(9) A boatswain's chair shall not be used where the suspension height exceeds 92 metres without the prior permission of the minister.
(10) A thorough inspection shall be made of a boatswain's chair and associated equipment before use each day and defective equipment shall not be used.
Part XIX GENERAL BLASTING
Section 417 Definitions
417. In this Part
(a) "blaster" means a person who holds a valid blaster's certificate granted by the province;
(b) "blasting activity" includes storing, handling, transporting, preparing and using explosives, and drilling conducted at a blasting area or in relation to the use of explosives;
(c) "blasting area" means the zone extending at least 50 metres in all directions from the place in which explosives are prepared, handled or loaded for firing, or in which misfired explosives exist or are believed to exist and from which hazards shall be excluded to avoid an accidental explosion;
(d) "blasting machine" means an electrical or electro-mechanical device which provides electrical energy for the purpose of energizing electric detonators and electrical circuits for continuity, resistance, stray currents and other pertinent measurements;
(e) "blasting switch" means a device used to permit the firing of electric blasting circuits from power lines and constructed so that the door may be closed and locked with the switch in the "OFF" position;
(f) "danger area" means the zone in which there exists a possibility of hazard to person or property from fly rock, fume, air blast or ground vibrations;
(g) "day box" means a portable unit used for keeping explosives in during the day and which meets the requirements of "Storage Standards for Industrial Explosives" published by the Explosives Division of Natural Resources Canada;
(h) "detonator" includes electric blasting caps of instantaneous and delay types, blasting caps for use with safety fuses, detonating cord, delay connectors and non-electric instantaneous and delay blasting caps which use detonating cord, shock tube, gas tube and another replacement for electric leg wires and another similar device;
(i) "explosive" means a substance, including a detonator or primed explosive, that is manufactured or used to produce an explosion by detonation or deflagration and that is regulated by the Explosives Act (Canada), but does not include ammunition for weapons or fireworks;
(j) "extraneous electricity" means unwanted electrical energy greater than 50 milliamps that is present at the blasting area that could enter an electric blasting circuit including stray current, static electricity, radio frequency energy and time-varying electric and magnetic fields;
(k) "magazine" means a fixed unit used for the unattended storage of explosives overnight and which meets the requirements of the "Storage Standards for Industrial Explosives" published by the Explosives Division of Natural Resources Canada;
(l) "misfired hole" means a charge of explosives in a hole or part of a hole which has failed to fire as planned and "misfire" has a corresponding meaning;
(m) "prime charge" means to position a detonator for use in firing an explosive charge;
(n) "primed explosive" means an explosive containing a detonator; and
(o) "stemming" means clean, crushed angular shaped stone, 12.5% of the borehole diameter in size, which provides confinement for explosive energy.
Section 419 Role of certified blaster
419. (1) Blasting shall be performed under the direct supervision of a blaster who is present at the project and who holds a valid blaster's certificate which authorizes the performance of the particular type of work that the blaster is to conduct or supervise.
(2) Direct supervision under subsection (1) includes a requirement that the blaster have a direct line of sight of the work area.
(3) The site supervisor shall consult with a blaster so that both are aware of all work being conducted in a blasting area and no work shall be conducted in a manner which creates risk of an accidental explosion.
(4) Where more than one blaster is involved in a blasting operation, an employer shall
(a) before the commencement of the blasting operation, designate one blaster who shall have principal responsibility for the blast;
(b) ensure that all persons in the blasting area are advised of the identity of the principal blaster; and
(c) ensure that all blasters and supervisors performing or directing the work in a blasting area consult sufficiently to coordinate the safety of the activity.
(5) A person, other than a blaster, shall not
(a) prime a charge;
(b) make a connection which leads or which may lead from the explosive charge to a blasting machine, a blasting switch, safety fuse or a shock tube initiating system including a NONEL;
(c) connect a delay or sequencing device or program the delay or sequence for the blast; or
(d) fire an explosive charge.
(6) An explosive charge shall not be fired until the blaster or principal blaster, where one is designated, has ensured that the placement of the charge and all other features of the blasting activity are adequate to ensure the safety of persons at or near the workplace.
Section 440 Unique blasting operation
440. (1) An employer shall ensure that, in addition to the requirements of these regulations, a safe work procedure is developed for the use and handling of explosives in the following circumstances:
(a) in a confined space other than underground;
(b) underwater;
(c) for demolition of above-ground buildings, stacks, or other structures including beaver dams;
(d) for ice control;
(e) in theatrical applications where the special effects are explosives other than fireworks;
(f) for oil and gas well control;
(g) where black powder is used; or
(h) at the request of an officer who concludes that a procedure involves an unusual use of explosives in the operation.
(2) In the case of a conflict between the safe work procedure referred to in subsection (1) and these regulations, these regulations shall apply.
Section 441 Seismic blasting
441. (1) Where seismic blasting is carried out in an isolated location, loaded holes may be left unattended only where the blaster has first ensured that
(a) leg wires are shunted together;
(b) drill cuttings are spread out and levelled;
(c) leg wires are coiled as close to the ground as possible while not exceeding 15 centimetres above the ground level; and
(d) holes are suitably user identified, recorded in the blasting log and blasted within 30 days.
(2) In a seismic blasting operation the firing line may be left connected to the firing switch and disconnected at the hole where a recorder can confirm complete detonation.
(3) A misfired or unfired charge in a seismic blasting operation, may be left unfired only where
(a) it cannot be conventionally and safely detonated;
(b)it is in an isolated location and at least 6 metres deep; and
(c)its location is effectively marked.
(4) A seismic water tank truck with open flame water heaters shall not be used to transport explosives unless
(a) the distance between the heat tube and the outside of the tank is at least 35 centimetres;
(b) the heater, where woodburning, has a fire box of a type that fully contains the fuel and 2 dampers mounted in the heat tube, one at the vent end and the other at the fire box, so the flame may be shut in instantaneously in the event of an accident; and
(c) the detonator storage is located on the opposite side of the vehicle from the explosive magazine and both are built to type 6 magazine standard.
(5) In a seismic operation where there is no alternate route, a vehicle may be driven over a loaded hole where
(a) bypassing the hole is not practicable;
(b) operational planning minimizes the requirement to travel through a loaded area;
(c) safe work procedures are developed and communicated to workers before work is started;
(d) loaded holes comply with subsection (1);
(e) explosive charges are at a minimum depth of 6 metres;
(f) radio transmission equipment is turned off or transmission capability is disabled by disconnecting the microphone; and
(g) electrical equipment, including cellular phones and other types of mobile telephone equipment which continuously transmit a radio signal when turned on shall be turned off when driving over a loaded hole.
Section 442 Misfire
442. (1) Where a charge has misfired or is suspected of having misfired, a person shall not move about the danger area until the expiry of the required waiting time in subsection (2).
(2) Where a charge has misfired or is suspected of having misfired, a blaster shall
(a) where using a safety fuse, wait 30 minutes after the last charge was due to explode before entering the blasting area;
(b) where using a means of initiation other than a safety fuse, wait 10 minutes after the last charge was due to explode before entering the blasting area; and
(c) where using an electric detonator, immediately disconnect the firing cable from the blasting machine or blasting switch and shunt the lead line
and at the end of the required waiting time, approach the misfired hole to assess the potential hazard.
(3) Where there is a misfire or a suspected misfire, a person shall not use metallic equipment in a blasting area until a blaster has inspected the site and authorized the use of the equipment and the following procedure shall be used:
(a) the site shall be fully illuminated;
(b) the work shall be directly and constantly supervised by a blaster; and
(c) precautions shall be taken to prevent injury from accidental explosion.
(4) An employer shall ensure that a misfire is treated at a safe and suitable time under the direction of a blaster in order to ensure the removal of hazards from the misfire in a manner that complies with these regulations.
(5) A blaster, in consultation with a supervisor, shall determine the safest and most practicable means of treating a misfire, either by reblasting or otherwise, and shall ensure compliance with these regulations.
(6) An employer shall, where practicable, ensure that the cause of a misfire is established and that corrective action is taken to prevent recurrence.
Part XX FIRE PREVENTION AND CONTROL
Section 443 Fire protection
443. (1) The design and occupancy of structures and the provision of fire alarm and detection equipment and fire protection equipment, in places of employment, shall comply with the Fire Prevention Act, 1991 and an employer shall ensure that work is carried out according to the applicable provisions of that Act and the National Fire Code.
(2) Fire alarm and detection equipment and fire protection equipment shall be maintained according to the manufacturer's instructions and any other requirements of provincial legislation.
(3) An employer that has
(a) controlled products as defined in the Workplace Hazardous Materials Information System (WHMIS) Regulations, 2018 ;
(b) explosives;
(c) pesticides;
(d) radioactive material;
(e) consumer products; or
(f) hazardous waste
in quantities which may endanger fire-fighters at a workplace shall ensure that the local fire department is notified of the nature and location of the hazardous materials or substances and methods to be used in their safe handling.
(4) Subsection (3) does not apply to a workplace:
(a) where materials are kept on site for less than 5 days, where the employer ensures that an alternate and effective means of notification of the fire department, appropriate to the hazard, is in place in the event of a fire or other emergency; or
(b) which is not within the service area of a fire department.
[S.N.L. 2019, c. 8, s. 20]
Section 444 Fire and explosion
444. (1) Where a worker is employed in or about a bilge, tank, compartment or cargo space of marine equipment or in an area where there is a possibility of the presence of a volatile or flammable substance, gas or vapour, an employer shall institute a system of inspections and tests to determine the presence of that substance, gas or vapour before work is commenced.
(2) Where a volatile or flammable substance, gas or vapour is present or arises from the work process, the hazard shall be removed or controlled by ventilation or other effective means.
(3) Where work or manufacturing processes involve the use of a flammable liquid, vapour or gas, the concentration of the liquid, vapour or gas in the work area shall be maintained below the lower explosive limit (LEL) of the substance involved.
(4) A container used to carry, transfer, or store a flammable solvent shall meet the requirements of the CSA Standards and shall be electrically grounded or bonded while the contents are transferred from one container to another.
(5) Waste material contaminated with a solvent, oil, grease, paint or other flammable substance shall be placed in covered metal containers before disposal and shall not be stored in work areas.
(6) Where a volatile or flammable substance, gas or vapour is present, or arises out of material or equipment or from a work process, existing or potential sources of ignition shall be controlled or eliminated.
(7) For the purpose of subsection (6), a source of ignition includes an open flame, spark-producing mechanical equipment, welding and cutting processes, smoking, static discharge, electrical equipment or an installation that is not approved for hazardous locations, as specified by the Canadian Electrical Code.
(8) Where work involves more than one employer, a principal contractor shall ensure that sources of ignition resulting from the work of one employer are eliminated or adequately controlled where a flammable gas or a flammable liquid is handled, used or stored by another employer.
Part XXIII DIVING AND OTHER MARINE OPERATIONS
Section 461 Definitions
461. In this Part
(a) "lifejacket" means a device that, when worn correctly, provides a specified buoyancy that turns the wearer face-up on entering the water and keeps the wearer in this position;
(b) "master" means a person in overall command of a commercial fishing vessel but does not include a pilot; and
(c) "personal flotation device" means a device that, when worn correctly, provides a specified buoyancy to support a conscious person in an upright or backward leaning position, but is not designed to turn a person from a face-down to a face-up position in the water.
[N.L.R. 43/22, s. 37]
Section 462 Wharves, platforms, etc.
462. (1) Floors, platforms and decks of wharves and floating equipment shall be kept in good repair and free from hazards.
(2) Clear passageway shall be provided on a wharf deck in an area where lines may be handled.
(3) Curbs and bullrails shall be installed on open sides of floats, docks, wharves, piers and other areas where mobile equipment is used.
(4) Curbs or bullrails shall be of substantial construction and shall be a height of at least 25.40 centimetres above the deck level.
Section 463 Ladders and gang planks
463. (1) A dock, wharf or pier shall be provided with ladders regularly spaced at intervals not exceeding 30.5 metres about its perimeter and which extend from the deck to at least one metre below water level.
(2) A fixed or portable ladder, gangplank or other safe means shall be provided and used where necessary to board and leave floating equipment.
(3) Portable means of access shall be secured to prevent dislodgement.
(4) A gangplank shall be provided with a guardrail in accordance with section 28, and where practicable, equipped with intermediate rails.
(5) The surface of a gangplank shall be provided with a means to prevent slipping.
Section 464 Lifesaving equipment
464. (1) Appropriate lifesaving equipment shall
(a) be provided and maintained for the rescue of a worker in danger of drowning; and
(b) be positioned at intervals not exceeding 50 metres in conspicuous locations as near as practicable to the danger area.
(2) A throwing line fitted to a lifebuoy or similar equipment shall be of suitable size and length and made of buoyant material.
(3) Lifesaving equipment shall meet the requirements of standards acceptable to the minister.
(4) A suitable boat shall be provided and kept ready for immediate use where a worker is employed in a situation where a boat is necessary for rescue or evacuation.
Section 465 Floating work platforms
465. (1) A floating work platform shall be designed by a professional engineer or other person acceptable to the minister.
(2) A floating work platform shall be used in such a manner that a worker is not endangered by instability or excessive movement of the platform.
Section 466 Personal flotation devices
466. (1) Where a worker is employed under conditions which expose the worker to a risk of drowning, the worker shall wear a personal flotation device appropriate to the work environment and hazards.
(2) The personal flotation device referred to in subsection (1) shall be labelled and meet the requirements and standards of the Canadian General Standards Board.
(3) A personal flotation device or lifejacket is not required when a personal fall protection system, safety net or other satisfactory means is being used according to Part X.
(4) A personal floatation device shall not be dependent on manual manipulation to provide the buoyant effect.
[N.L.R. 43/22, s. 38]
Section 467 Occupational diving operations
467. (1) The following standards respecting diving operations are adopted and constituted as part of these regulations:
(a) CAN/CSA-Z275.4-02 "Competency Standard for Diving Operations" ; and
(b) CAN/CSA-Z275.2-04 "Occupational Safety Code for Diving Operations" .
(2) Notwithstanding paragraph (1)(a), the following modifications to CAN/CSA-Z275.4-02 "Competency Standard for Diving Operations" apply to seafood harvesting and aquaculture diving operations:
(a) clause 7, SCUBA Supervisor (Restricted and Unrestricted) is struck and the following substituted:
(i) individuals who have successfully completed a five-day Surface Safety Attendant's course approved by the commission may supervise seafood harvesting and aquaculture diving operations.
Section 468 Instruction
468. (1) Before the start of each fishing season, the master shall ensure that each crewmember is instructed in the operational characteristics of the fishing vessel including
(a) the location and use of safety equipment, engine room components and controls;
(b) deck equipment and rigging;
(c) navigation equipment and electronic aids;
(d) fishing equipment and its use, including safe work practices for each fishery the vessel may be engaged in;
(e) procedures for anchoring the vessel;
(f) the location and use of emergency equipment, including firefighting and radio equipment; and
(g) escape routes in the event of fire.
(2) A master shall ensure, where reasonably practicable, that the instruction required by subsection (1) results in each crew member being able to apply the information where needed to protect the crew member’s health and safety.
(3) A new crewmember joining the vessel shall be instructed in accordance with the requirements of this section at the time that the crew member joins the vessel.
[N.L.R. 43/22, s. 39]
Section 469 Slipping and tripping hazards
469. (1) A work area on a vessel shall be kept
(a) clear of unnecessary obstructions; and
(b) free of slipping and tripping hazards.
(2) Decks shall have non-skid surfaces except in those locations where a smooth deck is required for handling fish.
(3) Tools and equipment shall be securely stowed when not in use.
Section 470 Galley requirements
470. (1) A galley stove on a vessel shall be fitted with rails or other means to restrain the movement of cooking utensils, and to prevent inadvertent contact by a crewmember.
(2) Stove fuel supply tanks and line
(a) shall be fitted with a shutoff valve at the tank; and
(b) shall not be located directly above the stove.
(3) Galley stoves shall
(a) be secured to prevent movement; and
(b) have sufficient clearance to permit the effective cleanup of oil and grease.
CCOHS


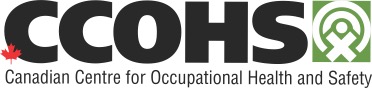