Lift Trucks
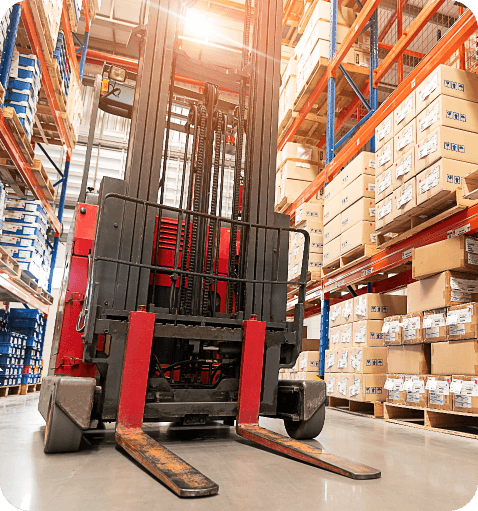
Highlighted words reveal definitions when selected.
Lift trucks are devices used to lift and position materials. They play an important role in the day-to-day operation of many workplaces. Some common types include forklifts, telehandlers, and pallet jacks.
Lift trucks must be inspected, maintained, modified, repaired, and operated in accordance with the manufacturer’s instructions, applicable standards, and legislation. Operators must be properly trained to operate the equipment.
Employer Responsibilities
Inspect, repair, maintain, modify, and operate
Employers must:
- Inspect the lift truck platform at appropriate intervals and in accordance with the manufacturer’s instructions to maintain safe working conditions and correct unsafe conditions. If emergency action is required to correct a condition, only qualified persons may be exposed to the hazard, and every effort must be made to control the hazard while it is being corrected. [OHS Regs., s. 18 (1)]
- Make sure a lift truck is capable of safely performing the functions for which it is used, and that it is selected, used, and operated according to the manufacturer’s instructions, applicable standards, and legislation. [OHS Regs., s. 88 (1)]
- Maintain lift trucks in a safe operating condition. [OHS Regs., s. 251(1)]
- Make sure inspection, repair, maintenance, modification, and operation are carried out according to the manufacturer’s instructions or, if there are no instructions, according to a professional engineer. [OHS Regs., s. 251(1)]
- Make sure service, maintenance, and repair of lift trucks is done when the equipment is: [OHS Regs., s. 251(2)]
- Not in operation; or
- Is in operation, but the continued operation is essential and work can be done safely.
- Make sure the design, fabrication, use, inspection, and maintenance of lift trucks meet the requirements of CSA B335 "Safety standard for lift trucks". [OHS Regs., s. 251(3)]
- Operators of lift trucks must be trained in accordance with CSA B335 “Safety standard for lift trucks”. Lift truck training expires after three years. [OHS Regs., s. 251(3)]
- Keep maintenance and inspection records up to date and make them available to the operator and maintenance personnel. [OHS Regs., s. 251(4)]
- Make sure the lift truck is appropriate for the intended use, when used off maintained roads. [OHS Regs., s. 251(5)]
- Provide appropriate fire suppression equipment aboard lift trucks, where required. [OHS Regs., s. 251(6)]
- Make sure the lift truck is equipped with the required safety features, such as warning devices, lights, mirrors, rollover protection structures, seats and seat belts. See the powered mobile equipment topic for more information.
Loading
When using lift equipment, a lifting device, or accessory to lift, suspend, or lower a load, or another similar operation the employer must make sure:
- Operators follow the safe working load (SWL) specified by the manufacturer, unless instructed otherwise by legislation. [OHS Regs., s. 16(1)]
- The SWL is certified by a professional engineer, or another person acceptable to OHS Division, when: [OHS Regs., s. 16(2)]
- The manufacturer’s specifications or warranty cannot be provided;
- The equipment has been modified in a way that changes its SWL;
- Wear, corrosion, damage, or signs of fatigue are found that may affect the SWL;
- The equipment is used in a way or for a purpose other than what it was designed for that changes the SWL; or
- An OHS Officer considers certification necessary.
- A lift truck has a permanent marking indicating the SWL, which can be easily seen and read by the operator. [OHS Regs., s. 259]
- Make sure a load is not left unattended by the operator unless it has been immobilized and secured against unintended movement. [OHS Regs., s. 270(1)]
- Cylindrical objects (e.g., compressed or liquefied gas cylinders, fire extinguishers, etc.) transported on their sides are restrained to prevent unintended movement. [OHS Regs., s. 276]
- Unitized loads do not project a distance greater than half its height above the fork carriage, back rest, or back rest extension of the lift truck. [OHS Regs., s. 277(1)]
- Loose objects that are part of the load do not project above the fork carriage, back rest, or back extension of a lift truck. [OHS Regs., s. 277(2)]
- Loads that may shift during transportation are restrained if shifting could result in the instability of the load or the lift truck. [OHS Regs., s. 277(3)]
Protection of pedestrian traffic
Where a lift truck operates near pedestrian traffic, the employer must make sure: [OHS Regs., s. 274(1)]
- Designated walkways are used to separate pedestrian traffic from areas where a lift truck operates, where practical.
- Where designated walkways are not practical, adequate safe work procedure(s) are in place to minimize the risk of a collision in hazardous work areas. These procedures must include:
- Use of a traffic control system;
- Enforcement of speed limits for lift truck; and
- Requirement for pedestrians and operators to acknowledge each other’s presence before a pedestrian can proceed through a hazardous work area, or another effective procedure.
Ventilation requirements
Where a lift truck is used indoors or in an enclosed area, the employer must make sure: [OHS Regs., s. 45(1), (2), (7) and (8)]
- There is adequate ventilation and appropriate circulation of clean air in accordance with standards established by ASHRAE and ACGIH.
- Workers are protected from dust, fumes, vapour, mist, or other harmful substances by using a properly maintained ventilation system that is sufficient for preventing worker overexposure.
- The engine is serviced to minimize the concentration of air contaminants in the exhaust according to ACGIH standards; and
- The work area is assessed to determine potential worker exposure to harmful levels of exhaust components, and that appropriate controls are used when there is a potential for exposure above ACGIH occupational exposure limits (TLVs).
Using a lift truck to support an elevating work platform
Where a lift truck is used to support an elevating work platform, the employer must:
- Provide a safe means for workers to get on and off the platform. [OHS Regs., s. 208]
- Make sure a work platform mounted on the forks of a lift truck are designed by an engineer or conform to a standard acceptable to OHS Division, and: [OHS Regs., s. 216]
- Are securely attached to the lifting carriage or lift truck forks;
- Have perimeter guardrails;
- Have guarding to prevent individuals on the platform from contacting hazardous parts of the lift truck; and
- Are clearly marked with the platform’s rated load.
- Make sure: [OHS Regs., s. 217]
- The lift truck operator remains at the controls;
- The lift truck mast is kept vertical;
- The lift truck is not moved except for minor adjustments to position the platform; and
- The worker on the platform uses a personal fall arrest system.
- Make sure workers do not use fall protection equipment unless they hold a current certification in fall protection, obtained from an approved training provider. Fall protection training expires after three years. [OHS Regs., s. 139]
Supervisors Responsibilities
Supervisors must:
- Make all reasonable efforts to protect the health, safety and welfare of the workers under their supervision. [OHS Act, s. 5.1]
- Advise workers under their supervision of present and potential workplace hazards, and provide written or oral instructions about safety precautions that must be followed. [OHS Act, s. 5.2(a)(b)]
- Make sure the operator of lift trucks are trained in accordance with CSA B335 “Safety standard for lift trucks”. Lift truck training expires after three years. [OHS Regs., s. 251(3)]
- Make sure the workers under their supervision use or wear personal protective equipment (PPE) and safety devices required for their protection. [OHS Act, s. 5.2(c)]
- Take appropriate action when an unsafe condition is reported to them without delay. [OHS Regs., s. 18(2)]
- Make sure workers wear high visibility apparel when they are exposed to the danger of contacting moving lift trucks. The high visibility apparel must be suitable for daytime or nighttime, as appropriate. [OHS Regs., s. 81]
- Make sure workers use a personal fall arrest system while working on a work platform mounted on a lift truck. [OHS Regs., s. 217(d)]
- Make sure workers do not use fall protection equipment unless they hold a current certification in fall protection, obtained from an approved training provider. Fall protection training expires after three years. [OHS Regs., s. 139]
- Supervise, or make sure a qualified instructor is overseeing any trainee operating equipment as authorized by the employer. [OHS Regs., s. 252(2)]
- Not operate or permit a worker to operate, a lift truck that could put the health and safety of a person at risk, or which is in violation of the Regulations. [OHS Regs., s 254]
- Make sure that the equipment operator and passengers wear seat belts at all times while the equipment is in motion, or when operated in a stationary mode. [OHS Regs., s. 266(4)]
- Make sure equipment is not operated until necessary repair or adjustment is made, where inspection finds an unsafe condition. [OHS Regs., s. 267(2)]
- Make sure the lift truck is equipped with the required safety features, such as warning devices, lights, mirrors, rollover protection structures, seats and seat belts. See the powered mobile equipment topic for more information.
Worker Responsibilities
Workers must:
- Make all reasonable efforts to protect their own health and safety, and that of workers and other persons at, or near, the workplace. [OHS Act, s. 6]
- Cooperate with the employer and co-workers to protect the health and safety of everyone in the workplace. [OHS Act, s. 7(a)]
- Use or wear all necessary PPE and safety devices according to manufacturers’ instructions and training. [OHS Act, s. 7(a.1)] [OHS Regs., s. 17(1)]
- Follow safe work practices and procedures. [OHS Regs., s. 17(2)]
- Immediately report hazards to the supervisor or employer. [OHS Regs., s. 17(3)]
- Cooperate with a person exercising a duty imposed by the OHS Act or Regulations, such as an OHS Officer. [OHS Act, s. 7(c)]
- Not carry out work, or operate a tool, appliance, or equipment, where a present or potential hazard creates imminent danger to themselves or others. [OHS Act, s. 8]
- Not stand or pass beneath a suspended load unless no practical alternative exists and a lifting procedure has been communicated to all affected workers. [OHS Regs., s. 318]
The operator of a lift truck must:
- Wear high visibility apparel when they are exposed to the danger of contacting moving lift trucks. The high visibility apparel must be suitable for daytime or nighttime, as appropriate. [OHS Regs., s. 81]
- Use a personal fall arrest system while working on a work platform mounted on a lift truck. [OHS Regs., s. 217(d)]
- Operate equipment safely, maintain full control, and comply with all applicable laws. [OHS Regs., s. 253(1)]
- Wear seat belts at all times, if available and required, when the equipment is in motion, or when operated in a stationary mode. It is the responsibility of the operator to make sure all passengers use seat belts. [OHS Regs., s. 266(4)]
- Inspect the equipment before it is used for each shift, and at appropriate intervals to make sure the equipment is safely maintained. Any defects or other conditions that may impact safe operation must be reported immediately to the supervisor or employer, and the equipment must not be used until repairs or adjustments are made. [OHS Regs., s. 267]
- Not leave an elevated load, part, extension, or machine unattended unless it has been immobilized and secured against inadvertent movement. [OHS Regs., s. 270(1)]
- Not move a load, cab, counterweight, or other part of the powered mobile equipment (PME), if movement will create a hazard to the operator or another person. [OHS Regs., s. 271]
- Not move PME if their view is obstructed. The equipment should only be moved if the view is obstructed and the following conditions are met: [OHS Regs., s. 272]
- The operator inspects the work area on foot immediately before moving;
- At the direction of a signaller:
- Located in a safe position in the continuous view of the operator;
- Having an unobstructed view of the area into which the equipment is being moved; and
- Having no other duties to distract them from viewing the PME; or
- Under the direction of a traffic control system.
- Make sure unitized loads do not project a distance greater than half its height above the fork carriage, back rest, or back rest extension of the lift truck. [OHS Regs., s. 277(1)]
- Make sure loose objects that are part of the load do not project above the fork carriage, back rest, or back extension of a lift truck. [OHS Regs., s. 277(2)]
- Makes sure loads that may shift during transportation are restrained if shifting could result in the instability of the load or the lift truck. [OHS Regs., s. 277(3)]
- Make sure a worker does not stand or pass beneath a suspended load unless no practical alternative exists and a lifting procedure has been communicated to all affected workers. [OHS Regs., s. 318]
- Make sure the lift truck is equipped with the required safety features, such as warning devices, lights, mirrors, rollover protection structures, seats and seat belts. See the powered mobile equipment topic for more information.
Related Topics
CSA
CSA is the Canadian Standards Association Group. Certain CSA standards are available for online viewing.To access these, you must first create an account with "CSA Communities".
Go to: https://community.csagroup.org/login.jspa?referer=%252Findex.jspa
Once you are logged in, click on the text below the "OHS Standards / View Access" graphic.
Click on the jurisdiction of your choice to see the CSA Standards as referenced in that legislation.
Standards may also be purchased from CSA Group: https://store.csagroup.org/
Safe working load (SWL)
The maximum safe force that a piece of lifting equipment, lifting device or accessory can exert to lift, suspend, or lower, a given mass without fear of breaking.Overloading powered mobile equipment can result in the accidental release of the load or the structural or mechanical failure of the lifting equipment. In simple terms, the SWL is the maximum load a piece of equipment can safely lift safely.
The SWL is usually marked on the equipment by the manufacturer.
OHS Officer
An occupational health and safety officer appointed under this Act and includes a medical practitioner providing services under section 20 while he or she is providing those services. [OHS Act, s. 2(i)]Traffic control
Traffic control includes the use of:
- Patrol vehicles
- Traffic lights
- Signs
- Barricades
- Cones
- Detours
- Traffic control persons
- Other necessary techniques and devices [OHS Regs., s. 373(1)]
ASHRAE
ASHRAE, founded in 1894, is a global society advancing human well-being through sustainable technology for the built environment. The Society and its members focus on building systems, energy efficiency, indoor air quality, refrigeration and sustainability within the industry. Through research, standards writing, publishing and continuing education, ASHRAE shapes tomorrow’s built environment today. ASHRAE was formed as the American Society of Heating, Refrigerating and Air-Conditioning Engineers by the merger in 1959 of American Society of Heating and Air-Conditioning Engineers (ASHAE) founded in 1894 and The American Society of Refrigerating Engineers (ASRE) founded in 1904.
https://www.ashrae.org/ACGIH (American Conference of Governmental Industrial Hygienists)
The American Conference of Governmental Industrial Hygienists (ACGIH) is a scientific organization that develops occupational exposure limits for chemical and physical hazards. These limits can be found in their TLVs® and BEIs® book.In Newfoundland and Labrador, acceptable occupational exposure limits are established by the ACGIH.
Threshold Limit Values (TLVs)
Threshold limit values represent conditions under which it is believed that nearly all workers may be repeatedly exposed, day after day, over a working lifetime, without adverse health effects.
Guardrails
A system of vertical and horizontal members that warns of a fall hazard and reduces the risk of a fall. [OHS Regs., s. 138]
Fall arrest system
A system of physical components attached to a worker that stops a worker during a fall. [OHS Regs., s. 138]Approved training provider
Some types of training, such as confined space entry, fall protection and power line hazards, must be delivered by WorkplaceNL approved training provider. A list of approved trainers and available courses can be found in the Certification Training Registry (CTR) https://ctr.bluedrop.io/#/.OCCUPATIONAL HEALTH AND SAFETY ACT
R.S.N.L. 1990, c. O-3
Section 2 Definitions
2. In this Act
(a) "assistant deputy minister" means an assistant deputy minister appointed under section 9 of the Executive Council Act for the proper conduct of this Act;
(b) "board" means the Labour Relations Board referred to in the Labour Relations Act;
(c) "committee" means an occupational health and safety committee referred to in this Act;
(d) "council" means the Occupational Health and Safety Council referred to in this Act;
(d.1) "department" means the department presided over by the minister;
(e) "division" means the Occupational Health and Safety Division;
(f) "employer" means a person who employs one or more workers;
(g) "minister" means the minister appointed under the Executive Council Act to administer this Act;
(h) "occupation" means employment prescribed by the regulations as an occupation;
(i) "officer" means an occupational health and safety officer appointed under this Act and includes a medical practitioner providing services under section 20 while the medical practitioner is providing those services;
(j) "principal contractor" means the person primarily responsible for the carrying out of a project and includes the person who owns the thing in respect of which the project is being carried out;
(k) "self-employed person" means a person who is engaged in an occupation on the person's own behalf;
(k.1) "supervisor" means a person authorized or designated by an employer to exercise direction and control over workers of the employer;
(l) "supplier" means a person who rents or leases tools, appliances or equipment to be used by a worker;
(m) "worker" means a person engaged in an occupation; and
(n) "workplace" means a place where a worker or self-employed person is engaged in an occupation and includes a vehicle or mobile equipment used by a worker in an occupation.
[S.N.L. 1999, c. 28, s. 1; 2006, c. 16, s. 1; 2009, c. 19, s. 1; 2023, c. 15, s. 1]
Section 5.1 Supervisors' general duty
5.1 A supervisor shall ensure, where it is reasonably practicable, the health, safety and welfare of all workers under the supervisor's direction and control.
[S.N.L. 2009, c. 19, s. 2; 2023, c. 15, s. 4]
Section 5.2 Specific duties of supervisors
5.2 A supervisor shall
(a) advise workers under the supervisor's direction and control of the health and safety hazards that may be met by them in the workplace;
(b) provide proper written or oral instructions regarding precautions to be taken for the protection of all workers under the supervisor's direction and control; and
(c) ensure that a worker under the supervisor's direction and control uses or wears protective equipment, devices or other apparel that this Act, the regulations or the worker's employer requires to be used or worn.
[S.N.L. 2009, c. 19, s. 2; 2023, c. 15, s. 5]
Section 6 Workers' general duty
6. A worker, while at work, shall take reasonable care to protect the worker's own health and safety and that of workers and other persons at or near the workplace.
[S.N.L. 2023, c. 15, s. 6]
Section 7 Specific duties of workers
7. A worker
(a) shall co-operate with the worker's employer and with other workers in the workplace to protect
(i) the worker's own health and safety,
(ii) the health and safety of other workers engaged in the work of the employer,
(iii) the health and safety of other workers or persons not engaged in the work of the employer but present at or near the workplace;
(a.1) shall use devices and equipment provided for the worker's protection in accordance with the instructions for use and training provided with respect to the devices and equipment;
(b) shall consult and co-operate with the occupational health and safety committee, the worker health and safety representative or the workplace health and safety designate at the workplace; and
(c) shall co-operate with a person exercising a duty imposed by this Act or regulations.
[S.N.L. 1999, c. 28, s. 3; 2001, c. 10, s. 26; 2004, c. 52, s. 2; 2023, c. 15, s. 7]
Section 8 Imminent danger
8. A worker shall not
(a) carry out work where there exists an imminent danger to the health or safety of the worker, another worker or another person; or
(b) operate a tool, appliance or equipment that will create an imminent danger to the health or safety of the worker, another worker or another person.
[S.N.L. 2023, c. 15, s. 8]
Occupational Health and Safety Regulations, 2012
N.L.R. 5/12
Part III GENERAL DUTIES
Section 16 Safe working load of equipment
16. (1) Except as provided elsewhere in these regulations, the safe working load of equipment shall be that specified by the manufacturer.
(2) The safe working load of equipment shall be certified by a suitably qualified and registered professional engineer or other person named by the employer and acceptable to the assistant deputy minister where
(a) the manufacturer's specification or other acceptable warranty cannot be produced;
(b) the equipment has been modified in a manner that changes its safe working load;
(c) wear, corrosion, damage or signs of fatigue are found which may reduce the safe working load;
(d) the equipment is used in a manner or for a purpose other than that for which it was originally designed, where that use changes the safe working load; or
(e) the provision of the certification is considered to be necessary by an officer.
Section 17 General duties of workers
17. (1) A worker shall make proper use of all necessary safeguards, protective clothing, safety devices, lifting devices or aids, and appliances
(a) designated and provided for the worker’s protection by the employer; or
(b) required under these regulations to be used or worn by a worker.
(2) A worker shall follow the safe work procedure in which the worker has been instructed.
(3) A worker shall immediately report a hazardous work condition that may come to the worker’s attention to the employer or supervisor.
[N.L.R. 43/22, s. 4]
Section 18 Safety inspections
18. (1) Regular inspections of all buildings, excavations, structures, machinery, equipment, work practices and places of employment shall be made by the employer or the employer’s representative at intervals to ensure that safe working conditions are maintained and that unsafe conditions found as a result of the inspection are remedied without delay.
(2) Where an unsafe condition is discovered by a person, it shall be reported as soon as practicable to a supervisor who shall ensure that appropriate action is taken, without delay, to prevent a worker from being injured.
(3) Where emergency action is required to correct a condition that constitutes an immediate threat to workers, only those qualified and properly instructed workers necessary to correct the unsafe condition shall be exposed to the hazard and every possible effort shall be made to control the hazard while the corrective action is taking place.
[N.L.R. 43/22, s. 5]
Part VI OCCUPATIONAL HEALTH REQUIREMENTS
Section 45 Ventilation
45. (1) An employer shall ensure that
(a) there is appropriate circulation of clean and wholesome air;
(b) there is adequate ventilation; and
(c) impurities are made harmless and inoffensive
in a workplace in accordance with standards established by ASHRAE and ACGIH.
(2) Where a work or process gives off dust, fumes, vapour, mist or other impurity of a kind and quantity liable to be injurious or offensive to a worker, an employer shall provide, maintain and ensure the proper use of a ventilation system sufficient to protect the worker against inhalation of impurities and to prevent impurities accumulating in the work space.
(3) Where practicable, local exhaust ventilation shall be installed and maintained near to the point of origin of an impurity to prevent it entering the air of the workplace and the breathing zone of its workers.
(4) Impurities removed under subsections (2) and (3) shall be exhausted clear of a workplace and prevented from entering a workplace.
(5) An employer shall ensure that,
(a) all parts of a ventilation system are maintained;
(b) louvers are cleaned regularly; and
(c) ventilation openings are free of obstruction and sources of contamination.
(6) Where possible, exhaust from an internal combustion engine operated indoors shall be vented to the outdoors.
(7) Where mobile equipment powered by an internal combustion engine is operated indoors or in an enclosed work area
(a) the engine shall be adequately serviced and maintained to minimize the concentration of air contaminants in the exhaust to the applicable ACGIH Standards, and
(b) the work area shall be assessed to determine the potential for exposure of workers to harmful levels of exhaust components.
(8) Where a worker is or may be exposed to an exhaust gas component in concentrations exceeding the applicable exposure limits, exhaust gas scrubbers, catalytic converters, or other engineering controls shall be installed.
(9) An employer, contractor or owner shall ensure that
(a) the mechanical ventilation system
(i) including humidification equipment, is constructed and maintained to minimize the growth and dissemination of micro-organisms, insects and mites through the ventilation system, and
(ii) where reasonably practicable, is readily accessible for cleaning and inspection;
(b) a qualified person inspects and maintains all parts of a mechanical ventilation system, cleans all louvers and replaces or adequately cleans all filters at a frequency that is sufficient to protect the health and safety of workers;
(c) a record of all inspections, maintenance and cleaning of the mechanical ventilation system is
(i) completed by a qualified person who performs the work, and
(ii) readily available for examination by the occupational health and safety committee, or worker representative or designate or, where there is no committee, representative or designate, by the workers and the occupational health and safety officer;
(d) when mechanical ventilation is required, the ventilating fans are located to prevent recirculation of contaminated air; and
(e) measurements of the air volume of the mechanical ventilation system are taken at suitable intervals to ensure compliance with the minimum air volume requirements in accordance with standards established by ASHRAE, ACGIH or other applicable standard approved by the minister.
(10) An employer shall ensure that, wherever possible, a less hazardous substance or work process is used in preference to a more hazardous substance or process.
(11) A ventilation system used to control airborne contaminants shall have electrical and mechanical systems designed to control all potential ignition sources and meet the requirements of the Canadian Electrical Code.
Part VII PERSONAL PROTECTIVE EQUIPMENT
Section 81 High visibility apparel
81. A worker whose duties are regularly performed in areas and under circumstances where the worker is exposed to the danger of moving vehicles or heavy equipment shall wear distinguishing apparel containing highly visible material suitable for daytime or night time use, as appropriate.
[N.L.R. 43/22, s. 17]
Part VIII MACHINERY AND EQUIPMENT
Section 88 Safe machinery and equipment
88. (1) An employer shall ensure that each tool, machine and piece of equipment in the workplace is
(a) capable of safely performing the functions for which it is used; and
(b) selected, used and operated in accordance with
(i) the manufacturer's recommendations and instructions, where available,
(ii) safe work practices, and
(iii) the requirements of these regulations.
(2) Except as otherwise provided in these regulations, the installation, inspection, testing, repair, maintenance or modification of a tool, machine or piece of equipment shall be carried out
(a) in accordance with the manufacturer's instructions or a standard acceptable to the minister; or
(b) as specified by a professional engineer.
(3) Where equipment or a structure is dismantled in whole or in part and subsequently reassembled, it shall not be used until completely checked and found to be safe for operation or occupancy.
Part X FALL PROTECTION
Section 138 Definitions
138. In this Part
(a) "anchorage point" means a secure point of attachment for a lifeline or lanyard;
(b) "arborist" means a worker trained and employed, in whole or in part, to climb trees for an economic or scientific purpose, including
(i) detection and treatment of disease, infections or infestations,
(ii) pruning, spraying or trimming,
(iii) repairing damaged trees,
(iv) assessing growth or harvesting potential, or
(v) scientific research;
(c) "body belt" means a belt worn by a worker as a means of fall restraint;
(d) "debris net" means a net that is used to catch material and debris that can drop from work areas;
(e) "fall arrest system" means a system of physical components attached to a worker that stops a worker during a fall;
(f) "full body harness" means a harness consisting of leg and shoulder straps and an upper back suspension unit that distributes and reduces the impact force of a fall;
(g) "guardrail" means a system of vertical and horizontal members that warns of a fall hazard and reduces the risk of a fall;
(h) "lanyard" means a flexible line used to secure a worker to a lifeline, a static line or a fixed anchor point;
(i) "lifeline" means a vertical line attached to a fixed anchor point or a static line and to which a lanyard and a ropegrab may be attached;
(j) "means of fall protection" means a fall protection system and includes a harness, net, rope, body belt, structure or other equipment or device or means of
(i) restraining a worker who is at risk of falling, or
(ii) stopping a worker who has fallen;
(k) "personnel safety net" means a net that is used to catch a worker during a fall;
(l) "ropegrab" means a mechanical fall-arrest device that
(i) is attached to a lifeline and a lanyard, and
(ii) locks itself immediately on the lifeline in the event of a fall;
(m) "safe surface" means a surface at a workplace that
(i) has sufficient size and strength to adequately support a worker who falls on to the surface, and
(ii) is sufficiently horizontal to prevent a further fall from the surface by a worker who has fallen on to the surface;
(n) "softener" means padding or hoses that are used with a lifeline or static line to prevent a rope from being cut or chafed; and
(o) "static line" or "horizontal life line" means a rope
(i) that is attached horizontally to 2 or more fixed anchor points, and
(ii) to which a fall arrest system is attached.
Section 139 Training requirement
139. A worker shall not use fall protection equipment after January 1, 2012 unless the worker has completed a training program on fall protection prescribed by the commission.
[N.L.R. 43/22, s. 23]
Part XI SCAFFOLDS, STAGES AND WORK PLATFORMS
Section 208 Safe access
208. Safe means shall be provided to get on and off the platform of an elevating work platform.
Section 216 Lift truck platform
216. A work platform mounted on the forks of a lift truck shall be designed by an engineer or conform to a standard acceptable to the minister and
(a) securely attached to the lifting carriage or forks;
(b) provided with perimeter guardrails meeting the requirements of sections 28 and 30;
(c) equipped with guarding to prevent occupants from contacting a hazardous part of the lifting machinery; and
(d) clearly marked with the rated load of the platform.
Section 217 Fall protection - lift truck
217. Where a worker is elevated on a work platform supported by a lift truck,
(a) the lift truck operator shall remain at the controls of the lift truck;
(b) the lift truck mast shall be kept vertical;
(c) the lift truck shall not be moved except for minor adjustments necessary to facilitate positioning of the platform; and
(d) a platform occupant shall use a personal fall protection system as required by Part X.
Part XII POWERED MOBILE EQUIPMENT
Section 251 Operation and maintenance
251. (1) Mobile equipment shall be maintained in safe operating condition and operation, inspection, repair, maintenance and modification shall be carried out in accordance with the manufacturer's instructions or, in the absence of instructions, as approved by a registered professional engineer.
(2) Servicing, maintenance and repair of mobile equipment shall be done
(a) when the equipment is not in operation; or
(b) when the equipment is in operation, where continued operation is essential to the process and a safe means is provided.
(3) The design, fabrication, use, inspection and maintenance of mobile equipment shall meet the requirements of the following applicable standard or other standards acceptable to the minister:
Table
Equipment | Applicable Standard |
Mobile and Locomotive Cranes | CSA Standard Z150 , "Safety Code for Mobile Cranes" |
Vehicles with Mounted Aerial Devices (except fire-fighting equipment) | CSA Standard C225 "Vehicle-Mounted Aerial Devices" |
Vehicles with Mounted Aerial Devices (fire fighting equipment) | NFPA 1911 "Standard for Inspection, Maintenance, Testing and Retirement of In-Service Automotive Fire Apparatus, 2007 Edition" |
Safety and Hazard Warnings | ISO Standard 9244:1995 "Earth moving machinery - safety signs and hazard pictorials - General principles |
Lift Truck and Associated Operator training | CSA Standard B335 "Safety Standard for Lift Trucks" |
(4) Maintenance and inspection records shall be maintained and made reasonably available to the operator and maintenance personnel during work hours.
(5) Mobile equipment used off maintained roads shall be appropriate and safe for the intended use taking into account factors including the nature of the travel surface and its slope and the activities to be undertaken.
(6) Adequate and approved fire suppression equipment shall be provided where required by the minister.
Section 252 Competency and testing operators
252. (1) A person shall not operate mobile equipment unless the person
(a) has received adequate instruction and has demonstrated to a supervisor or instructor that the person is a competent equipment operator;
(b) has been authorized to operate mobile equipment;
(c) is familiar with the operating instructions for particular equipment before the person attempts to operate it; and
(d) has, where required to operate an air brake equipped vehicle, evidence of successful completion of a course on air brake systems issued by an organization acceptable to the minister.
(2) Subsection (1) does not apply where a trainee operates the equipment under the supervision of a qualified instructor or supervisor as authorized by the employer.
[N.L.R. 43/22, s. 25]
Section 253 Operator's responsibility
253. (1) The operator of mobile equipment shall operate the equipment safely, maintain full control of the equipment, and comply with the laws governing the operation of the equipment.
(2) The operator of mobile equipment shall ensure that a worker is not in close proximity to the swing radius of the equipment while it is in operation.
Section 254 Supervisor's responsibility
254. A supervisor shall not knowingly operate, or permit a worker to operate, mobile equipment which is, or which could create, an undue hazard to the health or safety of a person, or which is in violation of these regulations.
Section 259 Load ratings
259. (1) Mobile equipment designed and used for lifting, hoisting or similar operations shall have a permanently affixed notation, legible and visible to the operator, stating the rated load of the equipment.
(2) A load chart shall be displayed in the operator's cab where the rated load varies with the reach of the equipment.
Section 266 Seating and standard requirements
266. (1) A well designed and constructed, safely located and securely mounted seat and seat belt or other safe facilities shall be provided for the operator of powered mobile equipment and a passenger.
(2) Safe facilities for an equipment operator, referred to in subsection (1), shall include:
(a) footboards or platforms upon which the workers stand or sit, located to protect workers from accidental contact; and
(b) handholds; or
(c) safety-belts, harnesses, guardrails or other effective means of restraint.
(3) Subsection (1) does not apply to mobile equipment designed to be controlled by an equipment operator in a standing position.
(4) Where mobile equipment is equipped with seat belts, in conformity with these regulations or other applicable federal or provincial legislation, the installations shall be maintained and they shall be worn by the equipment operator and passengers at all times while the equipment is in motion, or when operated in a stationary mode.
(5) Where a road grader is operated with cab doors open, and the equipment operator is necessarily in a standing position and unable to comply with subsection (4), additional restraining devices approved by the minister shall be installed and used to prevent occupants from falling from the cab.
(6) Where an equipment operator is required to operate in a standing position, there shall be protection provided equivalent to the protection required under subsection (5) in the form of a restraining harness designed to prevent the equipment operator being thrown from the cab in a roll-over situation, but the restraining harness shall have a quick release device.
Section 267 Start of shift inspection
267. (1) An operator shall inspect the mobile equipment before the start of operation on the shift and after that where required to ensure the safe operating condition of the equipment and a defect or other condition affecting the safe operation of the equipment shall be reported immediately to the supervisor or employer.
(2) A repair or adjustment necessary for the safe operation of the equipment shall be made before the equipment is used.
Section 270 Securing elevated loads
270. (1) An elevated load, part, extension or machine, shall not be left unattended by an operator unless it has been immobilized and secured against inadvertent movement.
(2) Where a worker is required to work beneath an elevated part of mobile equipment, the elevated part shall be securely blocked.
(3) An hydraulic or pneumatic jack shall not be used for blocking unless it has been fitted with a device to prevent collapse in the event of loss of hydraulic or pneumatic pressure.
Section 271 Swinging equipment
271. Where the swinging movement of a load, cab, counterweight or other part of mobile equipment creates a hazard, a worker shall not be within range of the swinging load or equipment, and the operator shall not move the equipment when a worker is so exposed.
Section 272 Obstructed view
272. Where a mobile equipment operator's view of the work area is obstructed, the operator shall not move the equipment until precautions have been taken to protect the operator and another worker from injury, including
(a) immediately before the movement, the inspection by the operator on foot of the area into which the equipment is being moved;
(b) direction by a signaller
(i) stationed in a safe position in continuous view of the operator,
(ii) having an unobstructed view of the area into which the equipment is being moved, and
(iii) not being otherwise occupied while the equipment is in motion; or
(c) direction by a traffic control or warning system.
Section 274 Pedestrian and equipment traffic
274. (1) Where practicable, designated walkways shall be used to separate pedestrian traffic from areas of operation of mobile equipment.
(2) Where it is impracticable to provide designated walkways, adequate safe work procedures to minimize the possibility of collision shall be used in hazardous work areas, including
(a) use of a traffic control system;
(b) enforcement of speed limits for mobile equipment; and
(c) a requirement for the pedestrian and the mobile equipment operator to acknowledge each other's presence before the pedestrian proceeds through the hazardous area; or
(d) other effective means.
Section 276 Restraint for cylindrical objects
276. Cylindrical objects transported on their sides shall be effectively restrained against inadvertent movement.
Section 277 Lift truck loads
277. (1) A unitized load transported on a lift truck shall not project a distance greater than half its height above the fork carriage, back rest or back rest extension of the lift truck.
(2) No part of a load comprised of loose objects may project above the fork carriage, back rest or back extension of a lift truck.
(3) A load which could shift during transportation shall be restrained where shifting would result in the instability of the load or the lift truck.
Part XIV CRANES, HOISTS AND OTHER LIFTING EQUIPMENT
Section 318 Loads over work areas
318. (1) An employer shall arrange work to prevent passing a load over workers wherever possible.
(2) A crane or hoist operator shall not pass a load over workers unless no practicable alternative exists and the lifting procedure has been communicated to all affected workers.
(3) A worker shall not stand or pass beneath a suspended load except as permitted under subsection (2).
Part XVI TRAFFIC CONTROL
Section 373 Traffic control
373. (1) For the purpose of this Part, "traffic control" includes
(a) patrol vehicles;
(b) traffic lights;
(c) signs;
(d) barricades;
(e) cones;
(f) detours;
(g) traffic control persons; and
(h) other techniques and devices necessary according to the particular circumstances.
(2) Where the movement of vehicular traffic constitutes a hazard to workers, effective traffic control shall be provided.
(3) Traffic control procedures shall at minimum meet the requirements of the Department of Transportation and Works "Traffic Control Manual for Roadway Work Operations" or procedures established by a municipality that have been approved by the minister and all relevant specifications.
(4) Notwithstanding subsection (3), an officer may require those additional or alternate traffic control procedures and equipment that are necessary in the particular circumstances.
CCOHS
- Battery Charging
- Forklift Trucks - Batteries
- Forklift Trucks - Common Factors in Forklift Incidents
- Forklift Trucks - Daily Checks
- Forklift Trucks - Fork Safety
- Forklift Trucks - Hazards of Propane
- Forklift Trucks - Load Handling
- Forklift Trucks - Loading and Unloading Vehicles
- Forklift Trucks - Maintaining Truck Control
- Forklift Trucks - Maintenance
- Forklift Trucks - Professional Operator
- Forklift Trucks - Safe Handling of Propane (LPG) Fuel
- Forklift Trucks - Traffic Management
- Forklift Trucks - Work Platforms to Elevate Personnel


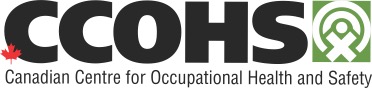